Thin film deposition is a critical process in various industries, including semiconductor manufacturing, optics, and energy. It involves applying a thin layer of material onto a substrate, and there are numerous methods to achieve this, categorized into chemical, physical, and electrically-based techniques. These methods vary in complexity, precision, and application, with some capable of depositing layers down to the atomic level. The choice of method depends on the desired film properties, substrate material, and specific application requirements.
Key Points Explained:
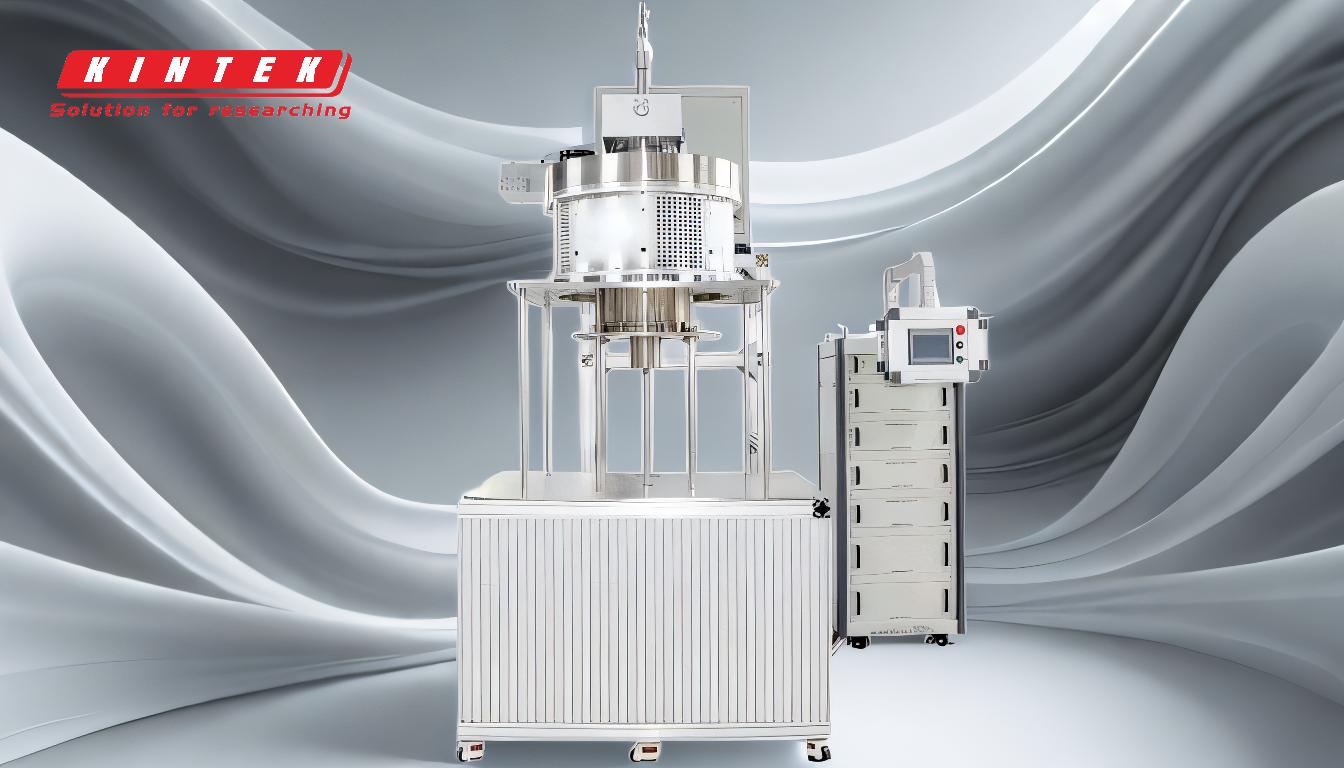
-
Chemical Methods:
- Electroplating: This method uses an electric current to reduce dissolved metal cations so that they form a coherent metal coating on an electrode. It is commonly used for decorative and protective coatings.
- Sol-Gel: This process involves the conversion of a solution (sol) into a solid (gel) phase, which is then dried and sintered to form a thin film. It is widely used for creating optical and protective coatings.
- Dip Coating: The substrate is dipped into a solution containing the coating material and then withdrawn at a controlled speed. This method is simple and used for creating uniform coatings on flat or curved surfaces.
- Spin Coating: A solution of the coating material is applied to a substrate, which is then spun at high speed to spread the solution evenly. This method is commonly used in the semiconductor industry.
- Chemical Vapor Deposition (CVD): In CVD, gaseous reactants are introduced into a reaction chamber, where they decompose and react on the substrate surface to form a thin film. It is used for high-quality, high-purity films.
- Plasma-Enhanced CVD (PECVD): This is a variation of CVD that uses plasma to enhance the chemical reaction rates, allowing deposition at lower temperatures. It is used for depositing films on temperature-sensitive substrates.
- Atomic Layer Deposition (ALD): ALD is a precision technique where thin films are deposited one atomic layer at a time. It is used for applications requiring extremely thin and uniform coatings.
-
Physical Methods:
- Sputtering: This method involves bombarding a target material with high-energy ions, causing atoms to be ejected and deposited onto a substrate. It is widely used for depositing metals and alloys.
- Thermal Evaporation: The target material is heated in a vacuum until it evaporates, and the vapor condenses on the substrate to form a thin film. It is used for depositing metals and simple compounds.
- Carbon Coating: This method involves depositing a thin layer of carbon onto a substrate, often used in electron microscopy to improve conductivity.
- Electron Beam Evaporation: An electron beam is used to heat the target material, causing it to evaporate and deposit onto the substrate. This method is used for high-purity films.
- Molecular Beam Epitaxy (MBE): MBE is a highly controlled process where beams of atoms or molecules are directed onto a substrate to grow thin films layer by layer. It is used for high-quality semiconductor films.
- Pulsed Laser Deposition (PLD): A high-power laser pulse is used to ablate material from a target, which then deposits onto the substrate. This method is used for complex materials like oxides and nitrides.
-
Electrically-Based Methods:
- Ion Beam Sputtering: This method uses an ion beam to sputter material from a target onto a substrate. It is used for high-precision applications.
- Magnetron Sputtering: A magnetic field is used to enhance the sputtering process, increasing the deposition rate and film quality. It is widely used in the semiconductor and optical industries.
-
Applications and Considerations:
- Semiconductor Industry: Methods like CVD, PECVD, and ALD are crucial for depositing thin films in semiconductor devices.
- Optics: Techniques such as sputtering and evaporation are used to create optical coatings for lenses and mirrors.
- Energy: Thin films are used in solar cells and OLEDs, where methods like PLD and spin coating are employed to create efficient and flexible layers.
-
Process Optimization:
- Annealing: After deposition, thin films may undergo annealing to improve their properties, such as crystallinity and adhesion.
- Analysis: The film properties are analyzed to ensure they meet the required specifications, and the deposition process may be adjusted accordingly.
In conclusion, the choice of thin film deposition method depends on the specific requirements of the application, including the type of material, substrate, and desired film properties. Each method has its advantages and limitations, and often, a combination of techniques is used to achieve the best results.
Summary Table:
Category | Methods | Applications |
---|---|---|
Chemical Methods | Electroplating, Sol-Gel, Dip Coating, Spin Coating, CVD, PECVD, ALD | Decorative coatings, optical layers, semiconductor devices |
Physical Methods | Sputtering, Thermal Evaporation, Carbon Coating, Electron Beam Evaporation, MBE, PLD | Metals, alloys, high-purity films, semiconductor films, complex materials |
Electrically-Based | Ion Beam Sputtering, Magnetron Sputtering | High-precision applications, semiconductor and optical industries |
Need help selecting the right thin film deposition method for your application? Contact our experts today!