An inert atmosphere is used in the manufacture of alloys to prevent unwanted chemical reactions, such as oxidation or contamination, during processes like heat treatment, sintering, or hot isostatic pressing. By creating a controlled environment with gases like argon or nitrogen, manufacturers can ensure the alloy maintains its desired properties, such as strength, durability, and surface quality. This is especially critical in industries like aerospace, automotive, and petrochemical manufacturing, where material integrity is paramount. The inert atmosphere also reduces risks like fire, explosions, and contamination, ensuring safer and more efficient production processes.
Key Points Explained:
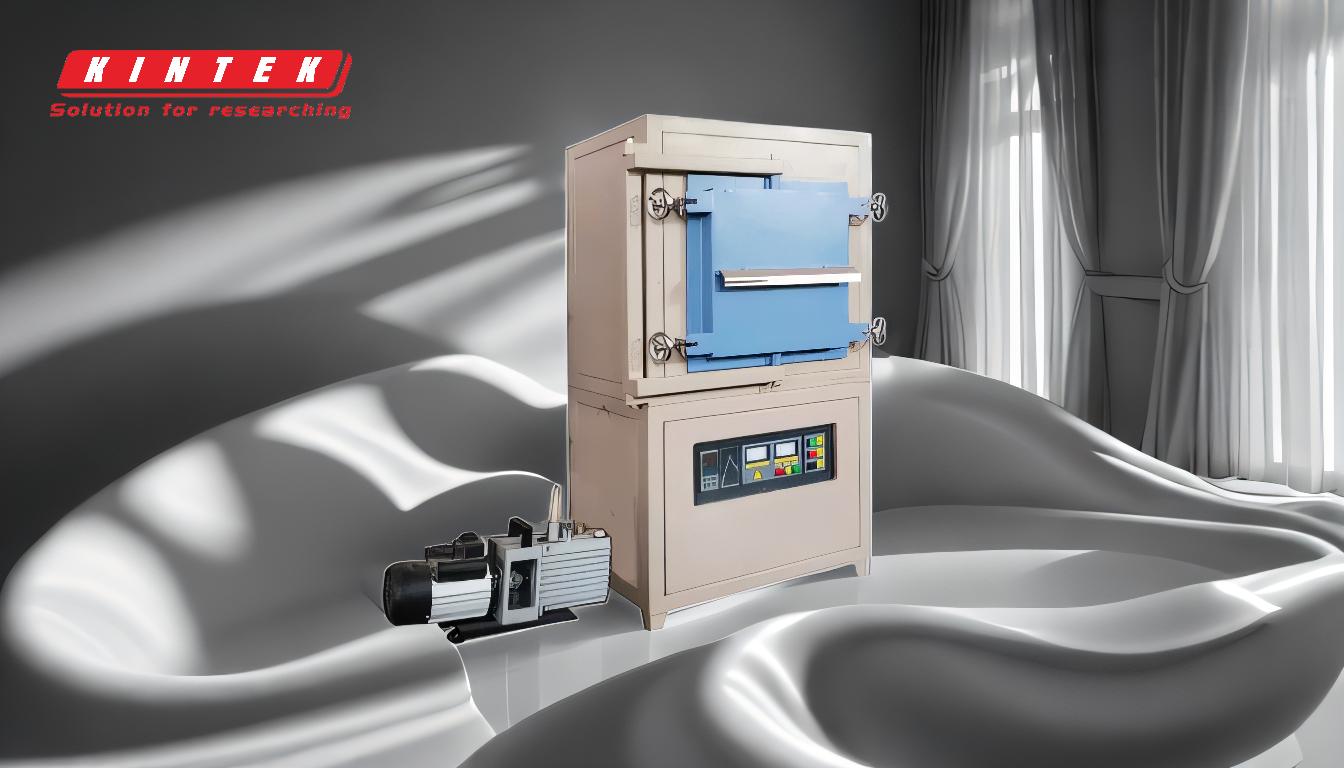
-
Prevention of Oxidation and Contamination
- Oxidation occurs when metals react with oxygen in the air, forming oxides that can degrade the alloy's surface and mechanical properties.
- An inert atmosphere, typically created using gases like argon or nitrogen, displaces oxygen and other reactive gases, preventing oxidation and contamination.
- This ensures the alloy retains its desired chemical composition and surface quality, which is critical for applications requiring high precision and durability.
-
Maintenance of Material Properties
- During heat treatment processes like sintering, bright annealing, or carbonitriding, the alloy's microstructure and mechanical properties are carefully controlled.
- An inert atmosphere ensures that these processes occur without interference from external factors, preserving the alloy's strength, hardness, and other critical properties.
- For example, in aerospace or automotive manufacturing, even minor deviations in material properties can lead to catastrophic failures.
-
Enhanced Process Control
- An inert atmosphere provides a highly controlled environment, reducing variability in the manufacturing process.
- This is particularly important in processes like hot isostatic pressing (HIP) or vacuum operations, where precise control over temperature, pressure, and gas composition is required.
- By minimizing unwanted reactions, manufacturers can achieve consistent results and reduce waste.
-
Safety and Risk Mitigation
- Inert atmospheres reduce the risk of fire and explosions, especially when working with reactive metals or high-temperature processes.
- By displacing oxygen, the likelihood of combustion is significantly lowered, creating a safer working environment.
- This is particularly important in industries like petrochemical manufacturing, where safety is a top priority.
-
Applications in Critical Industries
- Industries such as aerospace, automotive, and petrochemical manufacturing rely on inert atmospheres to produce high-quality alloys with precise specifications.
- For example, in aerospace, alloys must withstand extreme conditions, and any contamination or oxidation could compromise their performance.
- Similarly, in automotive manufacturing, components like engine parts or transmission systems require materials with consistent properties to ensure reliability and longevity.
-
Cost and Efficiency Benefits
- While creating an inert atmosphere may involve additional costs, the long-term benefits often outweigh the initial investment.
- By reducing oxidation and contamination, manufacturers can minimize material waste and rework, leading to cost savings.
- Additionally, the improved consistency and quality of the alloys can enhance the overall efficiency of the manufacturing process.
In summary, an inert atmosphere is essential in alloy manufacturing to prevent oxidation, maintain material properties, ensure process control, enhance safety, and meet the stringent requirements of critical industries. By using inert gases like argon or nitrogen, manufacturers can produce high-quality alloys with consistent performance, making it a vital component of modern industrial processes.
Summary Table:
Key Benefits of Inert Atmosphere | Details |
---|---|
Prevents Oxidation & Contamination | Uses gases like argon or nitrogen to displace oxygen, ensuring alloy integrity. |
Maintains Material Properties | Preserves strength, hardness, and durability during heat treatment processes. |
Enhances Process Control | Reduces variability, ensuring consistent results in processes like HIP or sintering. |
Improves Safety | Lowers risks of fire and explosions by displacing oxygen in high-temperature processes. |
Critical Industry Applications | Essential for aerospace, automotive, and petrochemical manufacturing. |
Cost & Efficiency Benefits | Reduces waste and rework, improving long-term manufacturing efficiency. |
Learn how an inert atmosphere can optimize your alloy manufacturing process—contact our experts today!