Carbon coating is a critical preparation technique in scanning electron microscopy (SEM) and transmission electron microscopy (TEM). It is primarily used to enhance imaging quality and facilitate energy-dispersive X-ray (EDX) analysis. Carbon coating helps reduce charging effects in non-conductive samples, improves the signal-to-noise ratio, and ensures accurate elemental analysis by avoiding interference with other elemental X-ray peaks. This process involves the thermal evaporation of carbon in a vacuum system, where a carbon source is heated to deposit a fine layer onto the specimen. Its applications are particularly valuable in X-ray microanalysis and TEM grid preparation.
Key Points Explained:
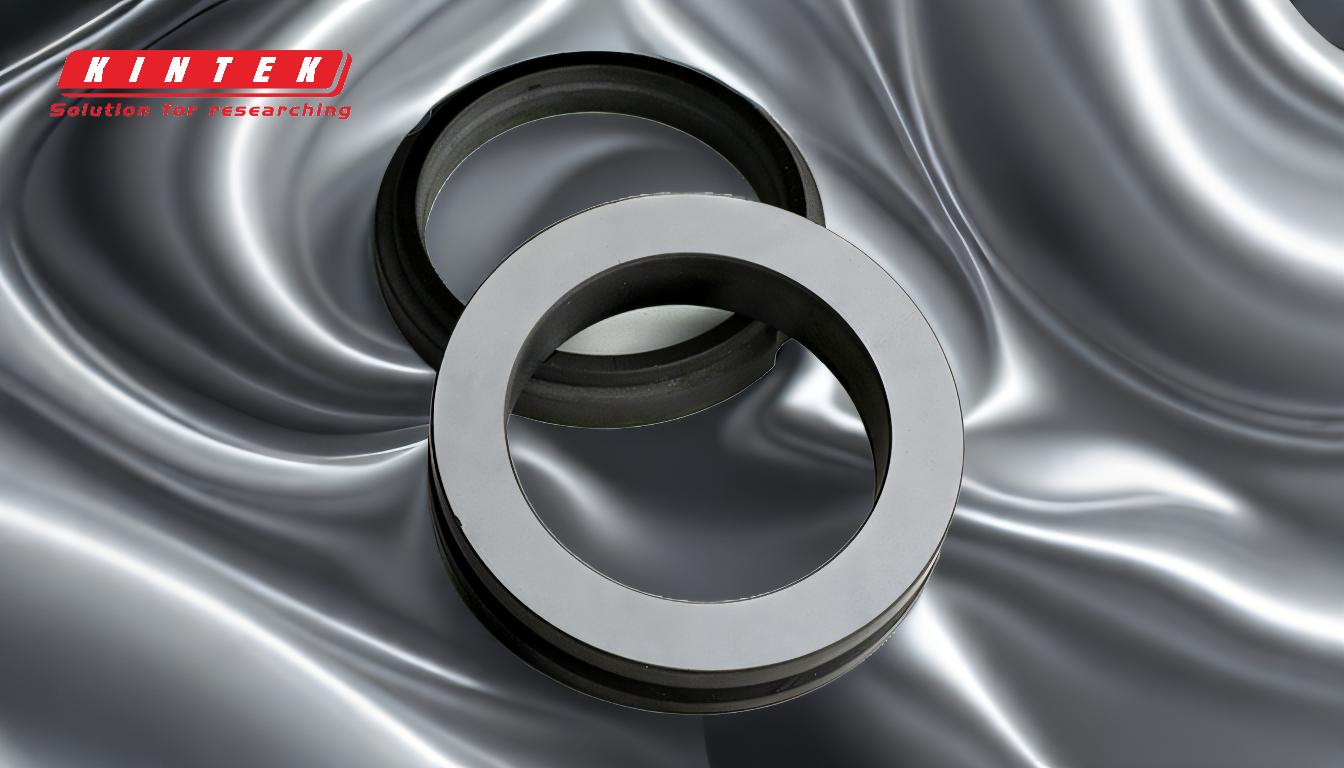
-
Reduction of Charging Effects:
- Non-conductive materials tend to accumulate electrons when exposed to the electron beam in SEM, leading to charging effects. These effects distort the image and make analysis challenging.
- Carbon coating provides a conductive layer on the sample surface, allowing electrons to dissipate and preventing charge buildup. This results in clearer, distortion-free images.
-
Improvement in Signal-to-Noise Ratio:
- Carbon coating enhances the signal-to-noise ratio during SEM imaging. This is particularly important for beam-sensitive samples, which can be damaged by prolonged exposure to the electron beam.
- By providing a uniform conductive layer, carbon coating ensures that the electron beam interacts more effectively with the sample, producing higher-quality images with better contrast and detail.
-
Compatibility with EDX Analysis:
- Carbon is an ideal material for sputter coating when EDX analysis is required. Unlike other coating materials (e.g., gold or platinum), carbon's X-ray peak does not overlap with the peaks of other elements.
- This ensures accurate elemental analysis, as the carbon coating does not interfere with the detection of other elements in the sample.
-
Thermal Evaporation Process:
- Carbon coating is applied through thermal evaporation in a vacuum system. A carbon source, such as a thread or rod, is mounted between high-current electrical terminals.
- When heated to its evaporation temperature, the carbon source releases a fine stream of carbon, which is deposited uniformly onto the specimen. This technique is widely used for preparing TEM grids and samples for X-ray microanalysis.
-
Applications in TEM and X-ray Microanalysis:
- In TEM, carbon coating is used to create thin support films on grids, which hold the specimen in place and provide stability during imaging.
- For X-ray microanalysis, carbon coating ensures that the sample surface is conductive and free from charging effects, enabling precise elemental mapping and analysis.
-
Advantages Over Other Coating Materials:
- Compared to metals like gold or platinum, carbon coating is less likely to interfere with EDX analysis due to its low atomic number and minimal X-ray peak overlap.
- It is also more suitable for high-resolution imaging, as it does not introduce additional artifacts or distortions.
By addressing these key points, carbon coating proves to be an essential technique in electron microscopy, particularly for non-conductive and beam-sensitive samples. Its ability to enhance imaging quality, reduce charging effects, and facilitate accurate elemental analysis makes it a preferred choice for researchers and technicians in the field.
Summary Table:
Key Benefit | Description |
---|---|
Reduces Charging Effects | Prevents electron buildup in non-conductive samples, ensuring distortion-free images. |
Improves Signal-to-Noise | Enhances image quality with better contrast and detail, ideal for beam-sensitive samples. |
Compatible with EDX | Avoids interference with elemental X-ray peaks, ensuring accurate analysis. |
Thermal Evaporation Process | Deposits a fine, uniform carbon layer via vacuum-based thermal evaporation. |
Applications in TEM & X-ray | Supports TEM grid preparation and enables precise elemental mapping in microanalysis. |
Advantages Over Metals | Minimal X-ray peak overlap and no artifacts, making it ideal for high-resolution imaging. |
Learn how carbon coating can optimize your SEM imaging—contact our experts today!