A controlled atmosphere furnace is highly desirable in sintering due to its ability to create an environment that prevents unwanted surface reactions, ensures precise temperature control, and enhances material properties. By using specific gas atmospheres like nitrogen-hydrogen, hydrogen, or vacuum, the furnace safeguards materials from oxidation and contamination, which is critical for achieving high-quality sintered products. Additionally, the controlled atmosphere allows for tailored chemical reactivity or inertness, enabling processes like carburizing and tempering. The furnace's thermal homogeneity, energy efficiency, and safety features further contribute to its suitability for sintering, making it an indispensable tool in manufacturing durable and precise metal components.
Key Points Explained:
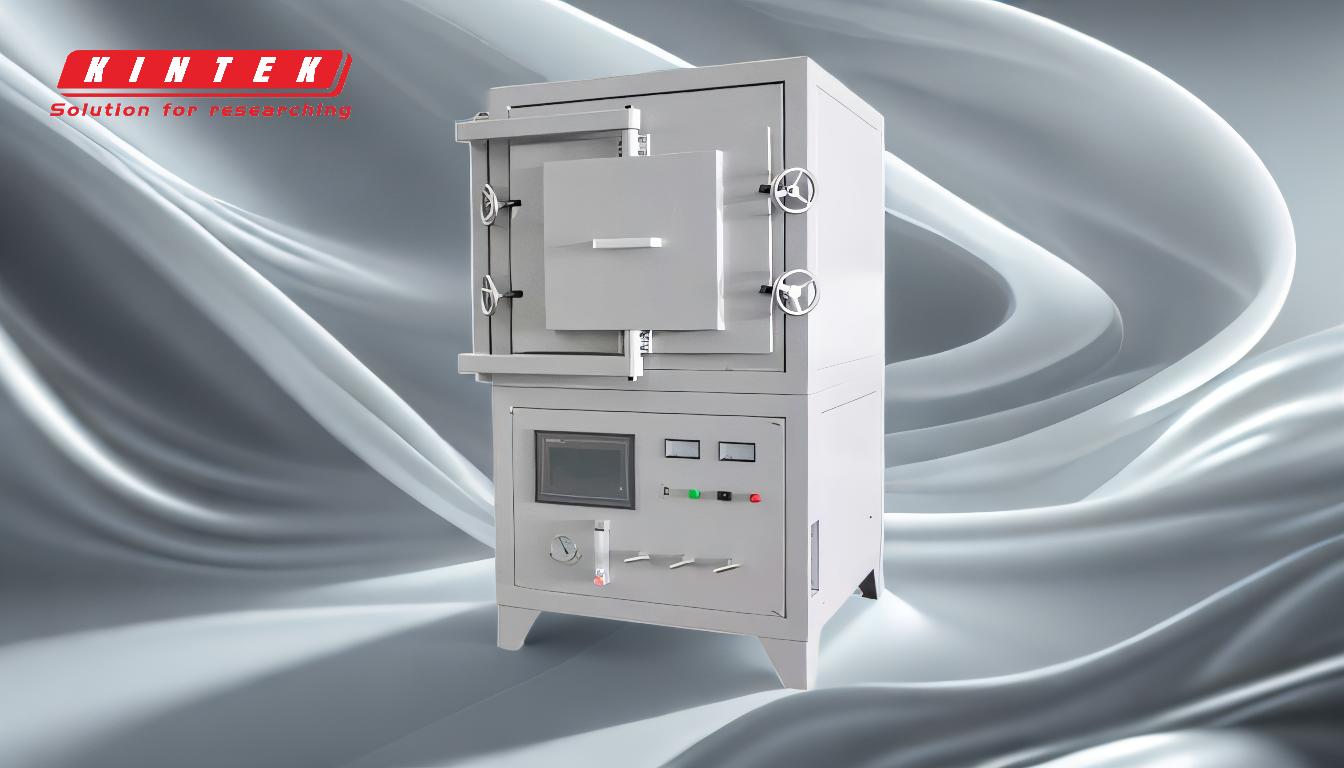
-
Prevention of Surface Reactions:
- A controlled atmosphere furnace prevents oxidation, decarburization, and other surface reactions that can degrade material quality during sintering. By maintaining a specific gas environment (e.g., nitrogen-hydrogen or hydrogen), the furnace ensures that the material surface remains clean and free from contaminants, which is critical for achieving the desired mechanical properties and surface finish.
-
Tailored Chemical Reactivity or Inertness:
- The furnace allows for precise control over the chemical environment, enabling processes like carburizing, tempering, and sintering. For example, a hydrogen atmosphere can reduce oxides on the material surface, while a vacuum environment can eliminate impurities. This flexibility ensures that the sintering process can be optimized for specific materials and applications.
-
Precise Temperature Control:
- Controlled atmosphere furnaces provide accurate and uniform heating, which is essential for sintering. The ability to maintain consistent temperatures ensures that the material undergoes proper compaction and strengthening without defects. This precision is particularly important for achieving the desired microstructure and mechanical properties in the final product.
-
Enhanced Material Properties:
- By avoiding contamination and ensuring uniform heating, controlled atmosphere furnaces produce sintered components with superior strength, durability, and dimensional accuracy. This is especially important for applications requiring high-performance materials, such as aerospace or automotive parts.
-
Energy Efficiency and Cost Savings:
- Controlled atmosphere furnaces are designed to minimize energy consumption and operating costs. Their high efficiency and thermal homogeneity reduce the need for excessive heating, making them a cost-effective solution for sintering processes.
-
Versatility in Processing:
- These furnaces can handle parts of any shape or size, making them suitable for a wide range of applications. Whether sintering small intricate components or large industrial parts, the controlled atmosphere furnace ensures consistent results.
-
Safety and Reliability:
- Equipped with advanced safety devices and controls, controlled atmosphere furnaces provide a secure environment for sintering. This reduces the risk of accidents and ensures reliable operation, even during high-temperature processes.
-
Environmental Benefits:
- By using inert or reducing atmospheres, controlled atmosphere furnaces minimize the release of harmful byproducts, making them an environmentally friendly choice for sintering.
In summary, a controlled atmosphere furnace is indispensable for sintering due to its ability to prevent surface reactions, ensure precise temperature control, and enhance material properties. Its versatility, energy efficiency, and safety features make it a preferred choice for manufacturing high-quality sintered components.
Summary Table:
Key Benefits | Description |
---|---|
Prevention of Surface Reactions | Prevents oxidation, decarburization, and contamination for high-quality results. |
Tailored Chemical Reactivity | Enables processes like carburizing, tempering, and sintering with precise control. |
Precise Temperature Control | Ensures uniform heating for defect-free sintering and optimal material properties. |
Enhanced Material Properties | Produces durable, high-strength components with superior dimensional accuracy. |
Energy Efficiency & Cost Savings | Minimizes energy consumption and operating costs. |
Versatility in Processing | Handles parts of any shape or size for consistent results. |
Safety and Reliability | Advanced safety features ensure secure, reliable operation. |
Environmental Benefits | Reduces harmful byproducts, making it an eco-friendly choice. |
Upgrade your sintering process with a controlled atmosphere furnace—contact us today to learn more!