Magnetron sputtering is a widely used thin-film deposition technique that relies on the presence of a magnetic field to enhance the efficiency and effectiveness of the process. The magnetic field plays a crucial role in confining electrons near the target surface, increasing plasma density, and improving the sputtering rate. This leads to higher deposition rates, better film quality, and more uniform coatings. By trapping secondary electrons and increasing ionization, the magnetic field enables the process to operate at lower pressures, reducing collisions and improving overall efficiency. Below, we explore the key reasons why a magnetic field is essential in magnetron sputtering.
Key Points Explained:
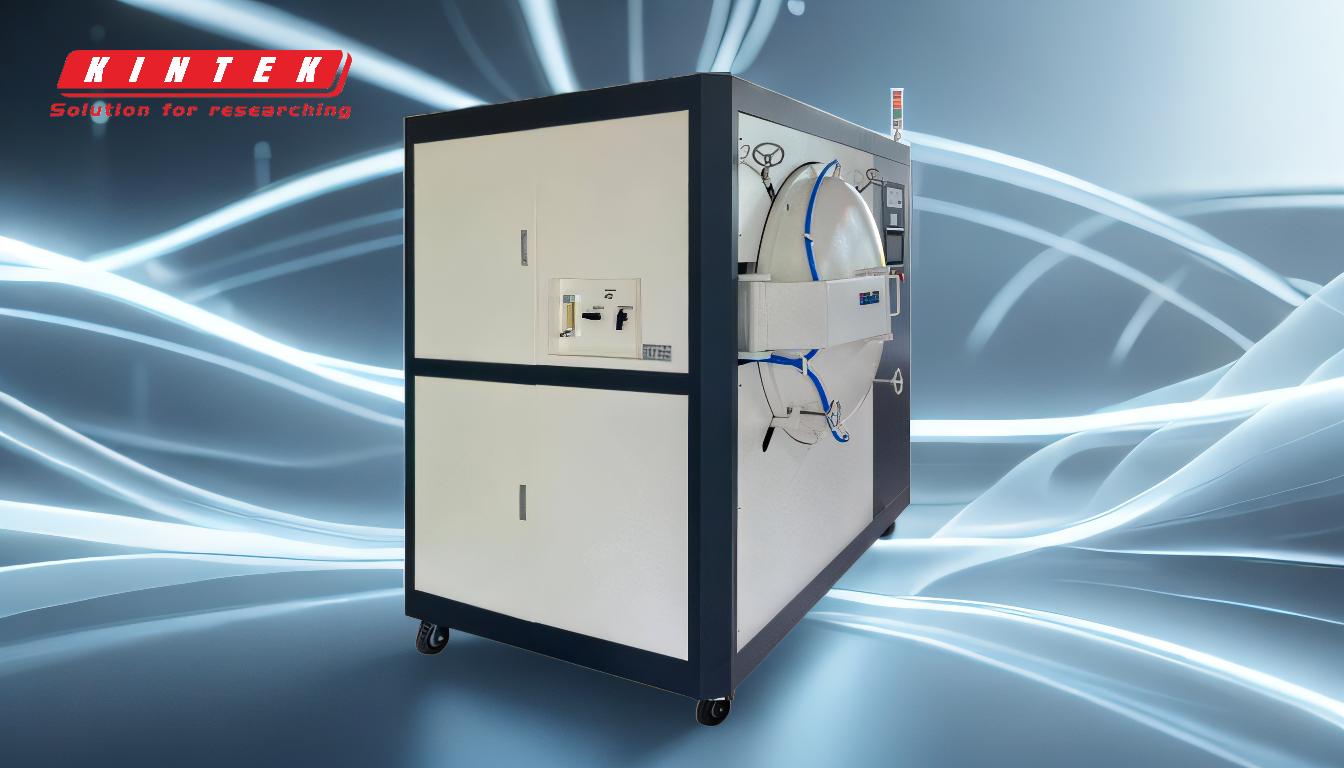
-
Confinement of Electrons Near the Target Surface:
- The magnetic field in magnetron sputtering creates a boundary "tunnel" that traps secondary electrons close to the target surface. This confinement increases the likelihood of collisions between electrons and argon atoms, leading to higher ionization rates.
- By keeping electrons near the target, the magnetic field ensures that the plasma remains dense and localized, which is critical for efficient sputtering.
-
Increased Plasma Density and Ionization:
- The trapped electrons ionize more argon atoms, creating a denser plasma near the target. This high-density plasma enhances the sputtering process by providing more energetic ions to bombard the target material.
- Higher ionization rates result in a more efficient transfer of energy to the target material, leading to faster sputtering and deposition rates.
-
Operation at Lower Pressures:
- The magnetic field allows magnetron sputtering to operate at lower pressures compared to conventional sputtering methods. Lower pressures reduce the number of collisions between sputtered atoms and gas molecules in the chamber, improving the efficiency of the process.
- Operating at lower pressures also minimizes contamination and improves the quality of the deposited film.
-
Higher Sputtering and Deposition Rates:
- The increased plasma density and ionization near the target surface lead to higher sputtering rates. This means more target material is ejected and deposited onto the substrate in a shorter amount of time.
- The magnetic field's ability to enhance the sputtering rate makes magnetron sputtering a preferred method for applications requiring high throughput.
-
Improved Plasma Stability and Uniformity:
- The magnetic field helps stabilize the plasma discharge, ensuring consistent and uniform deposition across the substrate. This is particularly important for achieving high-quality thin films with minimal defects.
- Uniform deposition is critical for applications in electronics, optics, and coatings, where consistency and precision are paramount.
-
Reduced Substrate Damage:
- By confining the plasma near the target, the magnetic field prevents excessive ion bombardment of the substrate. This reduces the risk of damage to the substrate and ensures that the deposited film adheres well without compromising its structural integrity.
-
Versatility in Power Supply Options:
- Magnetron sputtering systems can use either DC (direct current) or RF (radio frequency) power supplies, depending on the material being sputtered and the desired film properties. The magnetic field's role remains consistent across both types, ensuring efficient plasma generation and sputtering.
- DC magnetrons are typically used for conductive materials, while RF magnetrons are suitable for insulating materials.
In summary, the magnetic field in magnetron sputtering is indispensable for creating a dense, stable plasma near the target surface, enhancing ionization, and improving the overall efficiency of the sputtering process. Its ability to operate at lower pressures, increase deposition rates, and ensure uniform coatings makes it a cornerstone of modern thin-film deposition techniques.
Summary Table:
Key Role of Magnetic Field | Benefits |
---|---|
Confinement of Electrons | Increases ionization rates and plasma density near the target surface. |
Increased Plasma Density | Enhances sputtering rates and energy transfer to the target material. |
Operation at Lower Pressures | Reduces collisions and contamination, improving film quality. |
Higher Deposition Rates | Enables faster and more efficient thin-film deposition. |
Improved Plasma Stability | Ensures uniform and consistent coatings for high-quality films. |
Reduced Substrate Damage | Prevents excessive ion bombardment, protecting the substrate. |
Versatility in Power Supply | Supports both DC and RF power supplies for diverse material applications. |
Learn how magnetron sputtering can optimize your thin-film processes—contact our experts today!