A reducing atmosphere in ceramic firing produces a dark firing core due to the chemical reactions involving iron and other metal oxides present in the clay body. When the kiln environment lacks sufficient oxygen, incomplete combustion occurs, leading to higher carbon levels. This carbon reacts with metal oxides, particularly iron oxide, reducing them to lower oxidation states. Iron oxide (Fe₂O₃), which is typically red or orange in an oxidizing atmosphere, is reduced to ferrous oxide (FeO) or even metallic iron (Fe) in a reducing atmosphere. These reduced forms of iron are darker in color, resulting in a dark core within the clay body. This phenomenon is especially noticeable in stoneware, where iron content is significant.
Key Points Explained:
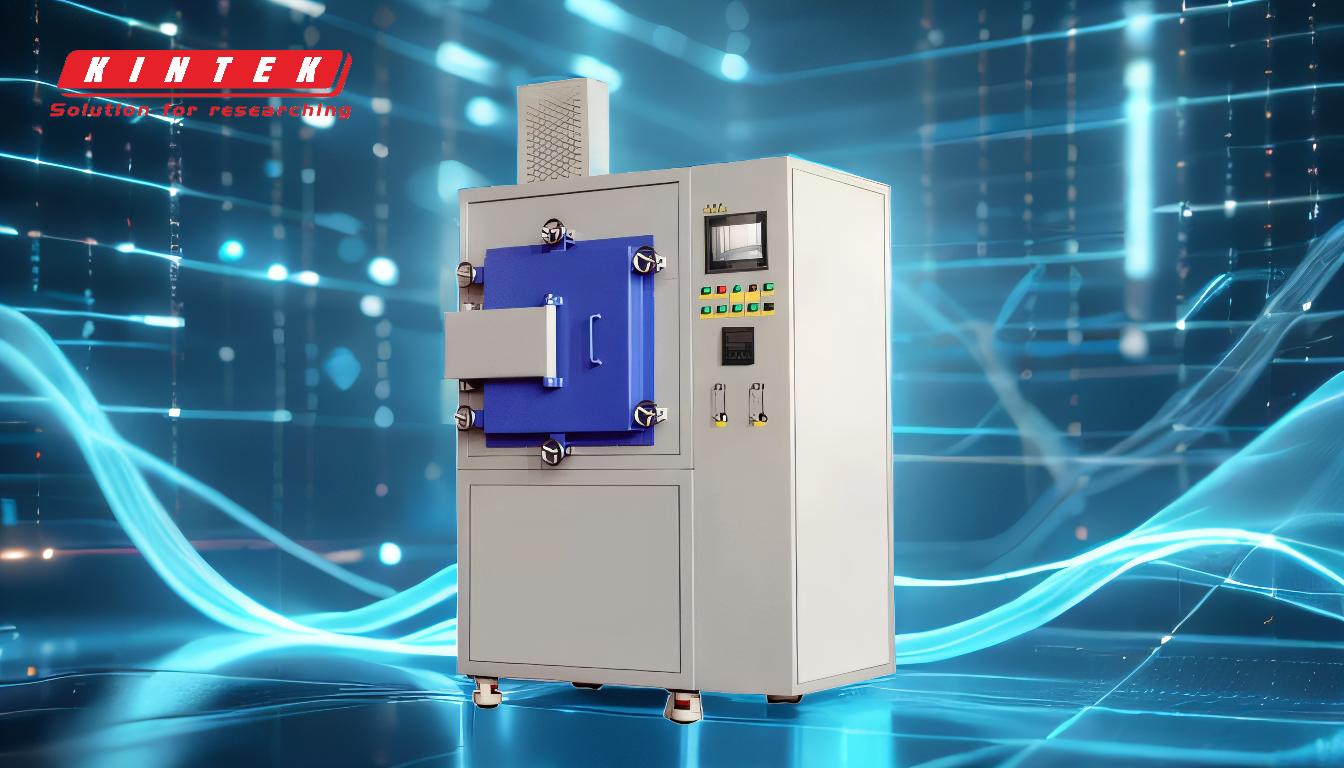
-
Definition of a Reducing Atmosphere:
- A reducing atmosphere is created in a kiln by limiting the oxygen supply, leading to incomplete combustion of the fuel. This increases the presence of carbon monoxide (CO) and other reducing gases.
- In ceramic production, this is often achieved by reducing the draft or partially closing the kiln's air vents.
-
Role of Iron in Clay Bodies:
- Iron is a common impurity in clay, present as iron oxide (Fe₂O₃). In an oxidizing atmosphere, iron oxide remains stable and imparts a red or orange color to the clay.
- In a reducing atmosphere, the chemical state of iron changes due to the lack of oxygen.
-
Chemical Reactions in a Reducing Atmosphere:
- At high temperatures, carbon monoxide (CO) and other reducing gases react with iron oxide (Fe₂O₃) in the clay body.
- The reaction can be simplified as:
[ \text{Fe}_2\text{O}_3 + \text{CO} \rightarrow 2\text{FeO} + \text{CO}_2 ] - In more extreme reducing conditions, iron oxide can be reduced further to metallic iron (Fe): [ \text{FeO} + \text{CO} \rightarrow \text{Fe} + \text{CO}_2 ]
-
Color Changes Due to Reduction:
- Iron oxide (Fe₂O₃) is red or orange, while ferrous oxide (FeO) and metallic iron (Fe) are darker, often gray or black.
- The reduction of iron oxide to these darker compounds results in a dark core within the clay body, especially in thicker sections where oxygen penetration is limited.
-
Impact on Stoneware:
- Stoneware clay typically contains higher amounts of iron, making it more susceptible to color changes in a reducing atmosphere.
- The dark firing core is more pronounced in stoneware due to the higher iron content and the thickness of the clay body, which restricts oxygen diffusion.
-
Practical Implications for Ceramic Production:
- Potters and ceramic artists use reducing atmospheres intentionally to achieve specific aesthetic effects, such as darker colors and unique glaze finishes.
- However, excessive reduction can lead to undesirable effects, such as bloating or weak structures, due to the formation of gases trapped within the clay body.
-
Comparison with Oxidizing Atmosphere:
- In an oxidizing atmosphere, sufficient oxygen is present, and iron remains in its higher oxidation state (Fe₂O₃), resulting in lighter colors.
- The contrast between oxidizing and reducing atmospheres highlights the importance of controlling kiln conditions to achieve desired outcomes.
By understanding these key points, ceramic producers can better control the firing process to achieve specific visual and structural effects in their work. The dark firing core is a direct result of the chemical changes induced by the reducing atmosphere, particularly the reduction of iron oxides within the clay body.
Summary Table:
Key Aspect | Description |
---|---|
Reducing Atmosphere | Created by limiting oxygen, leading to incomplete combustion and reducing gases. |
Iron Oxide Transformation | Fe₂O₃ (red/orange) reduces to FeO or Fe (gray/black) in a reducing atmosphere. |
Color Change | Dark core forms due to reduced iron compounds, especially in thick clay bodies. |
Impact on Stoneware | Higher iron content in stoneware makes it more prone to dark firing cores. |
Practical Use | Used for aesthetic effects but requires careful control to avoid defects. |
Learn more about achieving the perfect ceramic finish—contact our experts today!