Blast furnaces are critical in the production of iron, and the choice of raw materials significantly impacts their efficiency and performance. While sinter is a commonly used material in blast furnaces, using 100% sinter is not practical due to several technical and operational reasons. Sinter, a pre-processed iron ore product, offers advantages like improved permeability and reduced energy consumption. However, relying solely on sinter can lead to challenges such as reduced furnace stability, increased slag volume, and limitations in controlling gas flow and temperature. A balanced mix of sinter, pellets, and lump ore is typically used to optimize furnace performance, ensuring smooth operation and high-quality iron production.
Key Points Explained:
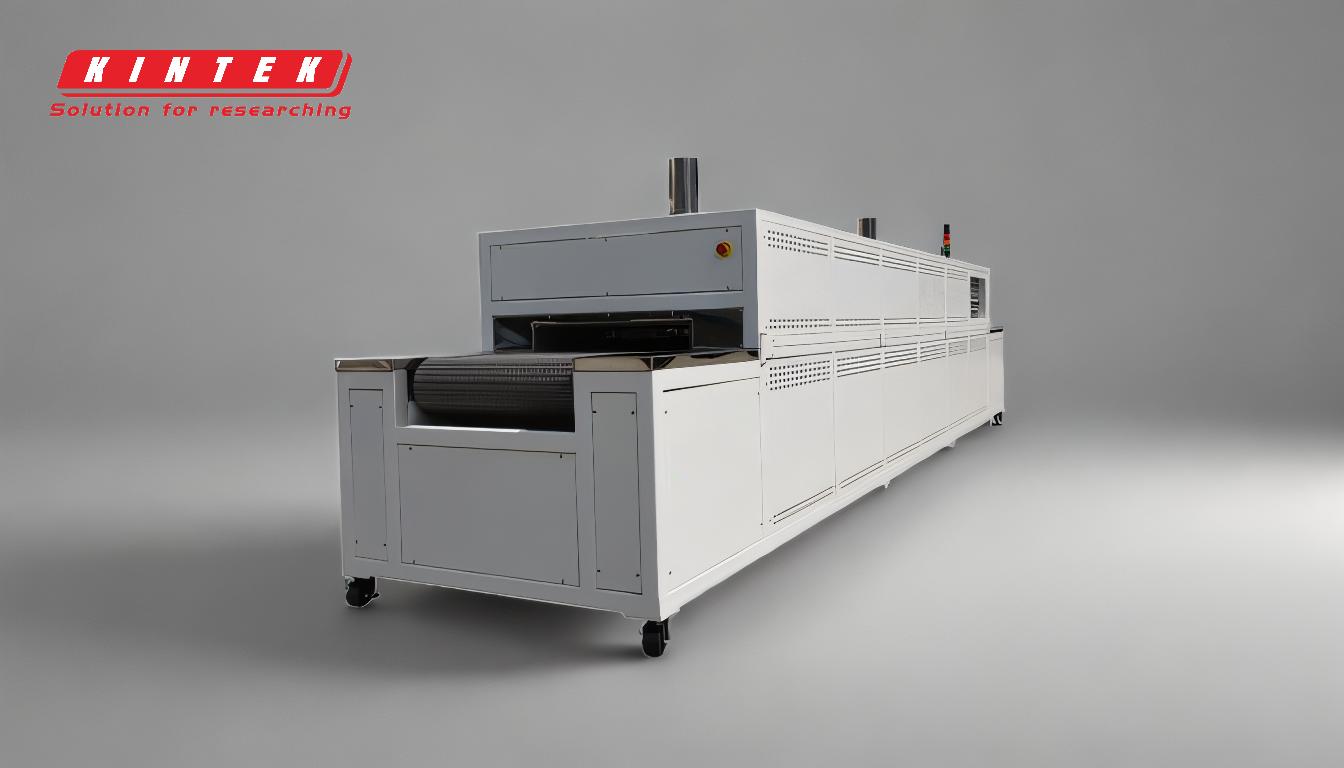
-
Furnace Stability and Permeability:
- Sinter improves the permeability of the blast furnace, allowing for better gas flow and heat distribution. However, using 100% sinter can lead to uneven gas distribution and reduced permeability, as the sinter particles may pack too densely. This can cause instability in the furnace, leading to operational inefficiencies and potential disruptions.
- A mix of sinter, pellets, and lump ore ensures a more uniform particle size distribution, enhancing gas flow and maintaining furnace stability.
-
Slag Formation and Volume:
- Sinter contains fluxes like limestone, which help in slag formation during the ironmaking process. However, excessive use of sinter can lead to higher slag volumes due to the increased flux content. This not only increases the energy required to melt the slag but also reduces the furnace's efficiency.
- A balanced mix of raw materials helps control slag volume and composition, optimizing the furnace's performance and reducing energy consumption.
-
Temperature Control and Gas Flow:
- The use of 100% sinter can make it challenging to control the temperature and gas flow within the blast furnace. Sinter has a higher melting point compared to other materials like pellets, which can lead to localized hot spots and uneven temperature distribution.
- By incorporating pellets and lump ore, the furnace operator can better regulate the temperature and gas flow, ensuring a more consistent and efficient ironmaking process.
-
Cost and Availability:
- While sinter is cost-effective and readily available, relying solely on it may not be economically viable in the long run. The production of sinter requires significant energy and resources, and its availability can be limited by raw material supply and production capacity.
- A diversified mix of raw materials, including pellets and lump ore, allows for greater flexibility in sourcing and cost management, ensuring a more sustainable and economical operation.
-
Quality of Iron Produced:
- The quality of iron produced in a blast furnace is influenced by the raw materials used. Sinter alone may not provide the desired chemical composition and physical properties needed for high-quality iron.
- A combination of sinter, pellets, and lump ore ensures a more balanced chemical composition, resulting in higher-quality iron with fewer impurities.
-
Operational Flexibility:
- Using a mix of raw materials provides operational flexibility, allowing furnace operators to adjust the feed based on changing conditions and requirements. This adaptability is crucial for maintaining consistent production levels and meeting quality standards.
- Relying solely on sinter limits this flexibility, making it harder to respond to fluctuations in raw material quality, market demand, or operational challenges.
In conclusion, while sinter is a valuable component in blast furnace operations, using 100% sinter is not feasible due to its impact on furnace stability, slag volume, temperature control, cost, and iron quality. A balanced mix of sinter, pellets, and lump ore is essential for optimizing blast furnace performance, ensuring efficient and high-quality iron production.
Summary Table:
Factor | Impact of 100% Sinter | Solution with Mixed Raw Materials |
---|---|---|
Furnace Stability | Uneven gas flow, reduced permeability, and instability | Uniform particle size distribution with sinter, pellets, and lump ore enhances stability |
Slag Volume | Increased slag volume due to higher flux content | Balanced mix controls slag volume, reducing energy consumption |
Temperature Control | Localized hot spots and uneven temperature distribution | Pellets and lump ore improve temperature regulation and gas flow |
Cost and Availability | Limited by raw material supply and high production costs | Diversified mix ensures cost-effectiveness and operational flexibility |
Iron Quality | Suboptimal chemical composition and physical properties | Balanced mix ensures higher-quality iron with fewer impurities |
Operational Flexibility | Limited adaptability to changing conditions | Mixed materials allow adjustments based on raw material quality and market demand |
Optimize your blast furnace performance with the right raw material mix—contact our experts today for tailored solutions!