Brazing is often considered better than welding in many applications due to its unique advantages. Unlike welding, brazing does not melt the base metals, which preserves their properties and reduces the risk of distortion or cracking. It is particularly effective for joining dissimilar materials, filling large gaps, and creating strong, leak-proof joints. Additionally, brazing offers greater control over the process, especially with automated systems, leading to consistent and precise results. It is also more cost-effective, as it reduces labor and production costs while increasing output speed. Furthermore, brazing furnaces and specialized techniques like hydrogen brazing provide clean, high-quality joints with minimal post-processing, making it ideal for high-precision and high-performance applications.
Key Points Explained:
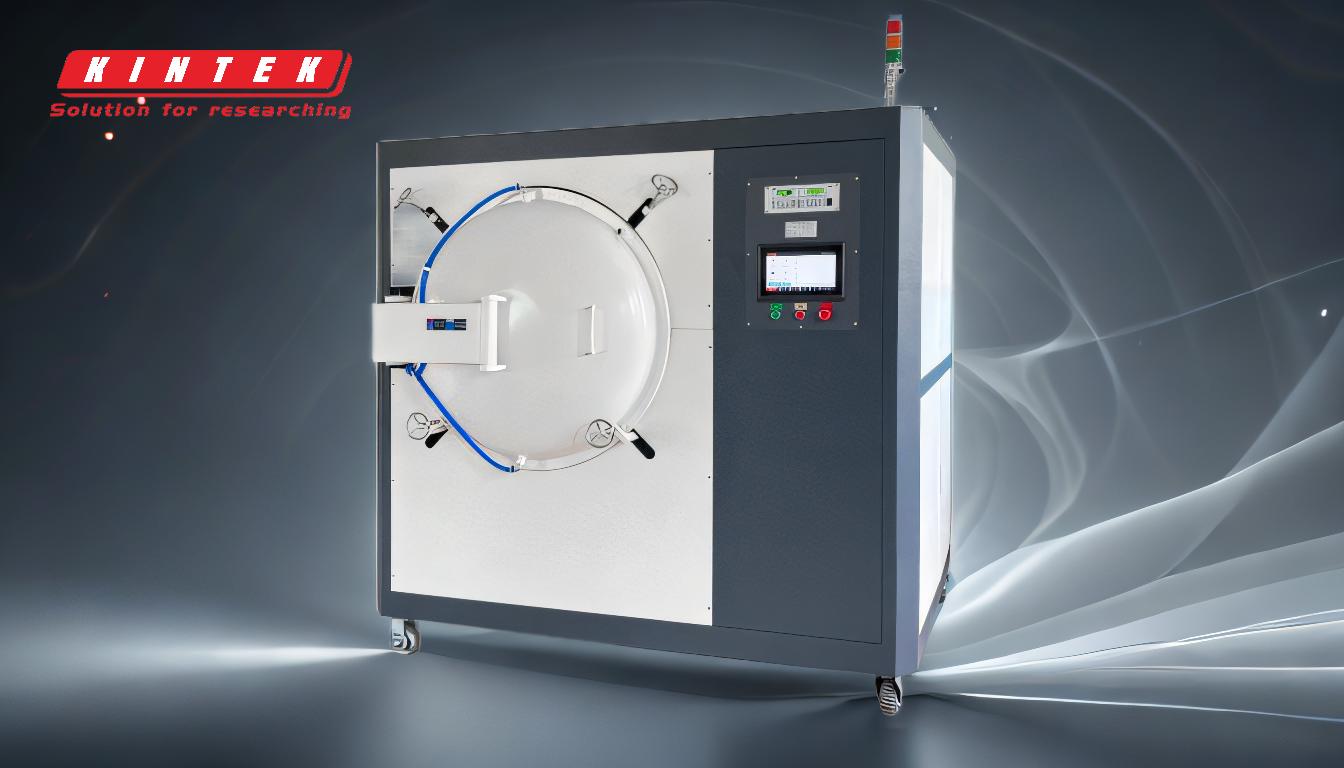
-
Preservation of Base Metal Properties:
- Brazing does not melt the base metals, which helps maintain their structural integrity and mechanical properties. This is particularly important for materials like cast iron, which are prone to cracking when exposed to high heat during welding.
-
Ability to Join Dissimilar Materials:
- Brazing allows for the joining of different metals and alloys, which is often challenging with welding. This versatility makes it suitable for applications where multiple materials need to be combined, such as in heat exchangers or automotive components.
-
Filling Large Gaps and Lap Joints:
- Brazing can fill large gaps and create strong joints in lap configurations without the need for external welds. This is especially useful in applications where precision and uniformity are critical, such as in heat exchangers.
-
Cost-Effectiveness and Efficiency:
- Automated brazing machines and furnace brazing systems reduce labor and production costs while increasing output speed. These systems provide consistent and accurate results, making them ideal for high-volume manufacturing.
-
Clean and High-Quality Joints:
- Techniques like hydrogen brazing produce clean, aesthetically pleasing joints by reducing oxides and removing contaminants. This eliminates the need for extensive post-braze cleaning and ensures superior capillary action for stronger bonds.
-
Minimal Distortion and Residual Stress:
- Brazing offers precise control over heating and cooling cycles, reducing residual stress and minimizing distortion. This makes it suitable for high-precision assemblies where dimensional accuracy is critical.
-
Integration with Heat Treatments:
- Furnace brazing can combine heat treatments like hardening or annealing with the brazing process, saving time and cost. This dual functionality enhances the efficiency of manufacturing processes.
-
Improved Heat Exchanger Performance:
- Brazing furnaces enable the creation of compact and uniform components, such as water pipes and heat-absorbing pieces. This improves heat-exchanging efficiency and extends the service life of the components.
By leveraging these advantages, brazing emerges as a superior joining method in many scenarios, particularly where precision, material compatibility, and cost-effectiveness are paramount.
Summary Table:
Advantage | Description |
---|---|
Preservation of Base Metal Properties | Brazing doesn’t melt base metals, maintaining structural integrity and reducing cracks. |
Joining Dissimilar Materials | Ideal for combining different metals, like in heat exchangers or automotive parts. |
Filling Large Gaps | Creates strong, leak-proof joints without external welds, ensuring precision. |
Cost-Effectiveness | Automated systems reduce labor costs, increase speed, and ensure consistent results. |
Clean, High-Quality Joints | Techniques like hydrogen brazing produce clean joints with minimal post-processing. |
Minimal Distortion | Precise heating and cooling cycles reduce stress and distortion for high-precision assemblies. |
Integration with Heat Treatments | Combines brazing with hardening or annealing, saving time and costs. |
Improved Heat Exchanger Performance | Enables compact, uniform components for better efficiency and longer service life. |
Ready to leverage the advantages of brazing for your applications? Contact us today to learn more!