Diamond is extensively used for making or coating tools due to its exceptional physical and chemical properties. As the hardest known natural material, diamond offers unparalleled hardness, wear resistance, and a low friction coefficient, making it ideal for machining difficult-to-cut materials like graphite, high-silicon aluminum alloys, and ceramics. Its high thermal conductivity and low thermal expansion coefficient ensure stability during high-precision and high-temperature operations. Additionally, diamond-coated tools combine the durability of diamond with the cost-effectiveness of carbide substrates, making them suitable for industries such as aerospace, electronics, and precision machining. Synthetic diamonds further enhance these properties, offering superior performance in cutting, polishing, and optical applications.
Key Points Explained:
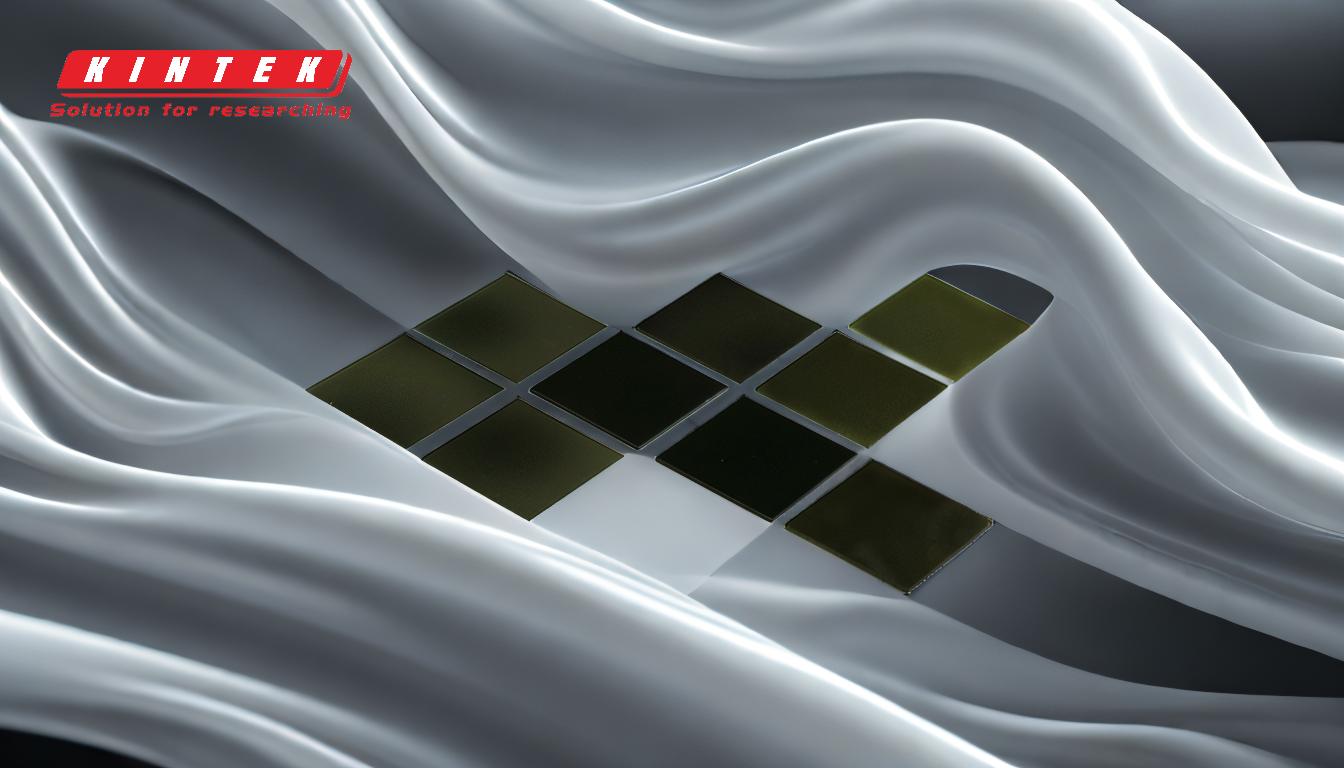
-
Unmatched Hardness and Wear Resistance:
- Diamond is the hardest material in nature, scoring a perfect 10 on the Mohs scale. This extreme hardness makes it highly resistant to wear and abrasion, even when cutting or machining tough materials like graphite, ceramics, and high-silicon aluminum alloys.
- Tools coated or made with diamond maintain their sharpness and integrity over extended periods, reducing the need for frequent replacements and improving efficiency.
-
Low Friction Coefficient:
- Diamond has an exceptionally low friction coefficient, which minimizes heat generation during cutting or machining processes. This property is crucial for maintaining tool performance and preventing material deformation or damage.
- The low friction also reduces energy consumption and enhances the precision of machining operations.
-
High Thermal Conductivity:
- Diamond exhibits extremely high thermal conductivity, allowing it to dissipate heat quickly during high-speed or high-temperature operations. This prevents overheating and thermal damage to both the tool and the workpiece.
- The ability to manage heat effectively makes diamond tools suitable for applications in precision machining and industries like aerospace, where thermal stability is critical.
-
Chemical Inertness:
- Diamond is chemically inert, meaning it does not react with most materials or chemicals. This property ensures that diamond tools remain stable and effective even when exposed to corrosive environments or reactive materials.
- Chemical inertness also contributes to the longevity of diamond-coated tools, as they are less likely to degrade over time.
-
Versatility in Applications:
- Diamond tools are widely used in industries such as aerospace, electronics, and precision machining. They are particularly effective for processing materials like graphite molds, ceramic teeth, 5G circuit boards, and carbon fiber.
- The ability to machine difficult-to-cut materials with high precision makes diamond tools indispensable in advanced manufacturing processes.
-
Cost-Effectiveness of Diamond Coatings:
- Diamond-coated tools involve depositing a thin layer (10–30 μm) of diamond onto carbide substrates. This combines the hardness and wear resistance of diamond with the affordability and versatility of carbide tools.
- The production cycle for diamond-coated tools is short, and their preparation costs are relatively low, making them a cost-effective solution for high-performance machining.
-
Superiority of Synthetic Diamonds:
- Synthetic diamonds, produced through advanced manufacturing processes, often exhibit properties superior to natural diamonds, such as enhanced hardness, thermal conductivity, and electron mobility.
- These synthetic diamonds are widely used in abrasives, cutting tools, heat sinks, and even electronic applications like high-power switches and UV detectors.
- Approximately 98% of industrial-grade diamond demand is met by synthetic diamonds, highlighting their importance in modern manufacturing.
-
Dimensional Stability in Precision Machining:
- Diamond tools are ideal for ultra-precision and micro-machining due to their extreme hardness and dimensional stability. They can achieve very tight tolerances and high surface finishes, which are essential for applications in electronics and optics.
- The stability of diamond tools ensures consistent performance and accuracy over time, even in demanding environments.
-
Durability and Longevity:
- Tools made with chemical vapor deposition (CVD) diamond coatings are significantly more durable than traditional carbide tools. They last longer and require less maintenance, reducing downtime and operational costs.
- The combination of hardness and toughness in CVD diamond makes it optimal for cutting operations, ensuring tools remain effective even under heavy use.
-
Optical and Electronic Applications:
- Beyond cutting tools, synthetic diamonds are increasingly used in optical components, thermal spreaders, and electronic devices. Their unique combination of thermal and chemical stability, low thermal expansion, and high optical transparency makes them ideal for high-power lasers and gyrotrons.
- These properties open up new possibilities for diamond in advanced technologies, further expanding its industrial applications.
In summary, diamond's exceptional hardness, wear resistance, thermal conductivity, and chemical inertness make it an ideal material for tool manufacturing and coating. Its versatility, cost-effectiveness, and superior performance in precision machining and advanced applications ensure its continued prominence in modern industry.
Summary Table:
Property | Benefits |
---|---|
Hardness | Perfect 10 on Mohs scale; resists wear and abrasion |
Low Friction Coefficient | Minimizes heat generation, reduces energy consumption |
High Thermal Conductivity | Dissipates heat quickly, prevents overheating |
Chemical Inertness | Resists corrosion, ensures tool longevity |
Versatility | Ideal for aerospace, electronics, and precision machining |
Cost-Effectiveness | Combines diamond durability with affordable carbide substrates |
Synthetic Diamonds | Enhanced properties for cutting, polishing, and optical applications |
Dimensional Stability | Achieves tight tolerances and high surface finishes |
Durability | Longer lifespan, reduced maintenance, and operational costs |
Optical & Electronic Use | Suitable for high-power lasers, thermal spreaders, and electronic devices |
Unlock the full potential of diamond tools for your industry—contact us today to learn more!