Mass-producing carbon nanotubes (CNTs) remains a significant challenge due to a combination of technical, economic, and scalability issues. While CNTs possess extraordinary mechanical, electrical, and thermal properties, their large-scale production is hindered by difficulties in achieving consistent quality, high yields, and cost efficiency. Current synthesis methods, such as chemical vapor deposition (CVD), arc discharge, and laser ablation, face limitations in scalability, energy consumption, and material purity. Additionally, post-production processing, such as purification and functionalization, adds complexity and cost. Environmental and safety concerns related to CNT production and handling further complicate mass production efforts. Despite advancements, these challenges collectively make it difficult to produce CNTs at a scale and cost that meet industrial demands.
Key Points Explained:
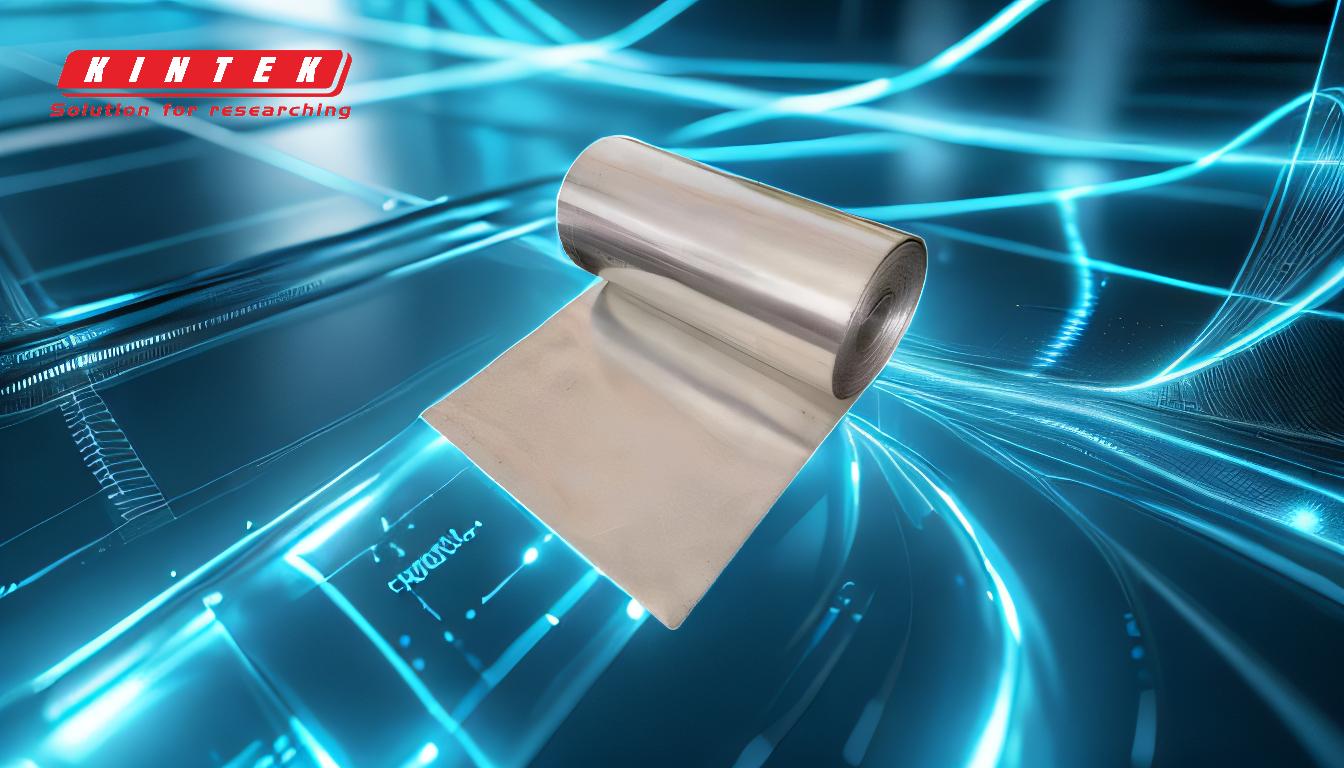
-
Inconsistent Quality and Yield:
- Carbon nanotubes must meet specific structural and functional requirements for various applications, such as electronics, composites, and energy storage. However, achieving uniform diameter, length, and chirality during synthesis is extremely challenging.
- Current production methods often result in a mix of single-walled, multi-walled, and defective nanotubes, which require costly post-processing to separate and purify.
- The yield of high-quality CNTs is often low, making it difficult to produce large quantities efficiently.
-
High Production Costs:
- The synthesis of CNTs, particularly through methods like chemical vapor deposition (CVD), requires expensive precursors, catalysts, and energy-intensive processes.
- Scaling up these methods without compromising quality or increasing costs remains a significant hurdle.
- Post-production steps, such as purification, functionalization, and dispersion, further drive up costs, making CNTs less economically viable for mass-market applications.
-
Scalability Limitations:
- While laboratory-scale production of CNTs is well-established, scaling up to industrial levels presents numerous challenges.
- Maintaining precise control over reaction conditions (e.g., temperature, pressure, and gas flow) becomes increasingly difficult at larger scales, leading to variability in product quality.
- Existing synthesis methods are not easily adaptable to continuous production processes, which are essential for mass manufacturing.
-
Energy Consumption and Environmental Concerns:
- CNT production is energy-intensive, particularly for methods like arc discharge and laser ablation, which require high temperatures and power inputs.
- The use of toxic chemicals and catalysts in some synthesis processes raises environmental and safety concerns, necessitating costly waste management and safety measures.
- Sustainability challenges further complicate efforts to produce CNTs at scale.
-
Post-Production Challenges:
- After synthesis, CNTs often require extensive processing to remove impurities, such as amorphous carbon and metal catalysts, which can affect their performance.
- Functionalization, or modifying the surface of CNTs to enhance compatibility with other materials, adds another layer of complexity and cost.
- Dispersion of CNTs in matrices for composite materials is also challenging, as they tend to agglomerate due to strong van der Waals forces.
-
Technological and Material Limitations:
- The lack of standardized production methods and quality control measures makes it difficult to produce CNTs with consistent properties.
- Alternative materials, such as graphene and carbon fibers, are sometimes preferred due to their easier production processes and lower costs, reducing the incentive to invest in CNT mass production.
-
Market and Application Barriers:
- The high cost and limited availability of CNTs restrict their use to niche applications, such as high-performance electronics and aerospace, where their unique properties justify the expense.
- For broader applications, such as in consumer electronics or construction materials, the cost of CNTs must be significantly reduced to compete with existing materials.
In summary, mass-producing carbon nanotubes is challenging due to a combination of technical, economic, and scalability issues. Overcoming these challenges will require innovations in synthesis methods, post-processing techniques, and cost-effective scaling strategies, as well as addressing environmental and safety concerns. Until these barriers are resolved, the widespread adoption of CNTs in industrial applications will remain limited.
Summary Table:
Challenge | Description |
---|---|
Inconsistent Quality & Yield | Difficulty in achieving uniform diameter, length, and chirality; low yield of high-quality CNTs. |
High Production Costs | Expensive precursors, catalysts, and energy-intensive processes; costly post-processing. |
Scalability Limitations | Challenges in maintaining precise control and adapting to continuous production. |
Energy & Environmental Issues | High energy consumption, toxic chemicals, and sustainability concerns. |
Post-Production Challenges | Purification, functionalization, and dispersion add complexity and cost. |
Technological Limitations | Lack of standardized methods and competition from alternative materials. |
Market Barriers | High costs restrict CNTs to niche applications; broader adoption requires cost reduction. |
Interested in overcoming CNT production challenges? Contact our experts today for innovative solutions!