When your aluminium brazing rod is not melting, it could be due to several factors, including incorrect temperature settings, improper flux application, or issues with the rod's composition or quality. Brazing requires precise conditions to ensure the filler metal (the brazing rod) melts and flows properly to join the base metals. If the rod isn't melting, it may indicate that the heat source isn't reaching the required temperature, the flux isn't activating correctly, or the rod itself is unsuitable for the job. Understanding these factors and troubleshooting them systematically can help resolve the issue.
Key Points Explained:
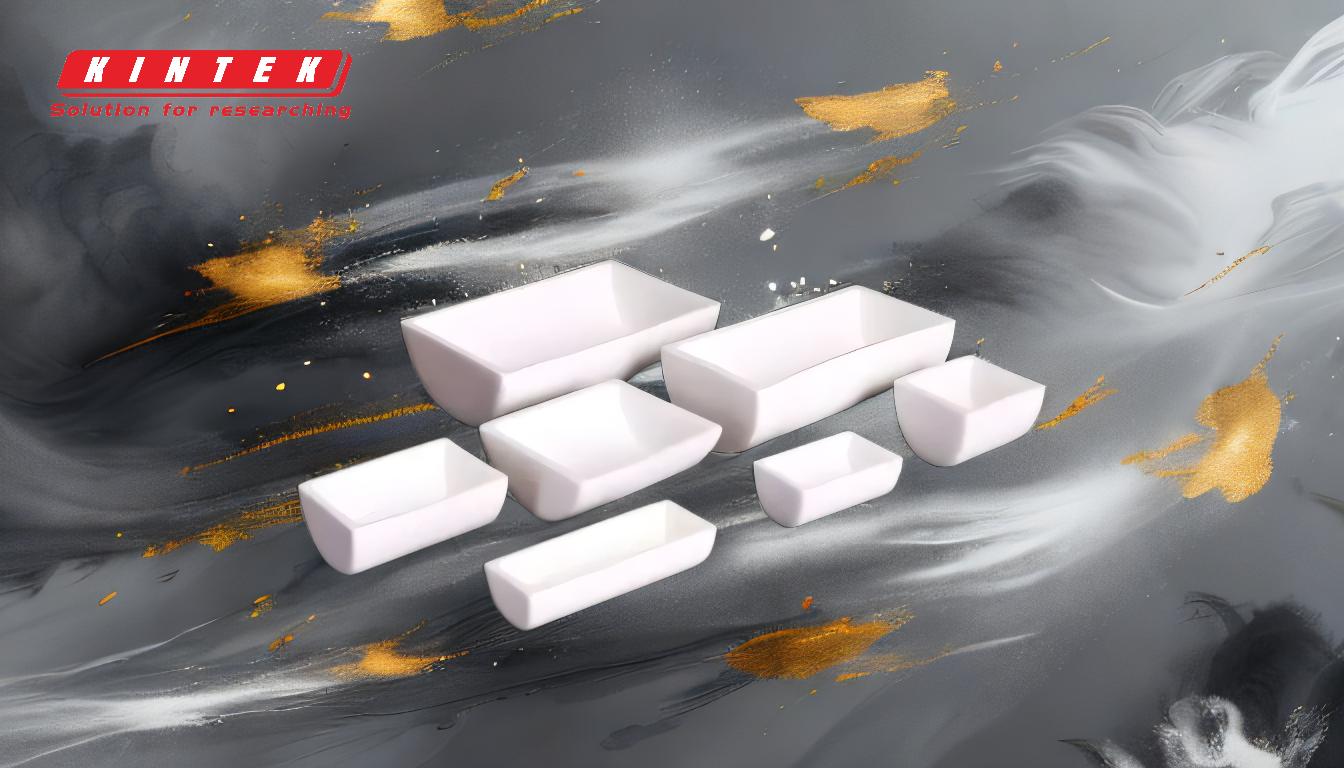
-
Insufficient Heat Source
- Brazing aluminium typically requires temperatures between 570°C and 620°C (1058°F and 1148°F). If your heat source (e.g., torch or furnace) isn't reaching this temperature range, the brazing rod won't melt.
- Check the specifications of your heat source to ensure it can generate sufficient heat. For example, a propane torch may not be adequate for aluminium brazing, whereas an oxy-acetylene torch is more suitable.
- Ensure the heat is evenly distributed across the joint area to avoid localized cold spots.
-
Incorrect Flux Application
- Flux is essential for aluminium brazing as it removes oxides from the metal surface and promotes the flow of the filler metal. If the flux isn't applied correctly or is of poor quality, the brazing rod may not melt properly.
- Use a flux specifically designed for aluminium brazing. Ensure it is applied evenly and in the right quantity.
- If the flux has expired or been contaminated, it may not activate properly, preventing the rod from melting.
-
Rod Composition or Quality Issues
- Not all brazing rods are created equal. Some may have a higher melting point or be incompatible with the base metal. Ensure you are using a brazing rod specifically designed for aluminium.
- Check the rod's specifications to confirm its melting temperature aligns with your heat source capabilities.
- Low-quality or counterfeit rods may not perform as expected. Always purchase rods from reputable suppliers.
-
Oxide Layer Formation
- Aluminium forms a thin oxide layer when exposed to air, which can prevent the brazing rod from adhering to the base metal. Proper surface preparation is crucial.
- Clean the aluminium surface thoroughly before brazing using a wire brush or chemical cleaner.
- Ensure the flux is applied immediately after cleaning to prevent re-oxidation.
-
Environmental Factors
- Brazing in a drafty or cold environment can cause heat loss, making it difficult to reach the required temperature. Work in a controlled environment to minimize heat dissipation.
- High humidity can affect the performance of the flux and the brazing process. Store flux and rods in a dry place and avoid brazing in damp conditions.
-
Technique and Experience
- Brazing aluminium requires skill and practice. Inexperienced users may struggle to maintain the correct temperature or apply the flux and rod properly.
- Take time to learn the proper techniques, such as heating the base metal first and then introducing the brazing rod.
- Consider seeking guidance from experienced professionals or training resources to improve your technique.
By addressing these factors systematically, you can identify and resolve the issue preventing your aluminium brazing rod from melting. Always ensure you are using the right tools, materials, and techniques for the job.
Summary Table:
Issue | Solution |
---|---|
Insufficient Heat Source | Ensure heat source reaches 570°C–620°C (1058°F–1148°F). Use an oxy-acetylene torch. |
Incorrect Flux Application | Use aluminium-specific flux, apply evenly, and avoid expired/contaminated flux. |
Rod Composition/Quality | Verify rod specs and melting point. Purchase from reputable suppliers. |
Oxide Layer Formation | Clean aluminium surface thoroughly and apply flux immediately. |
Environmental Factors | Work in a controlled, draft-free environment. Avoid high humidity. |
Technique and Experience | Learn proper brazing techniques or seek professional guidance. |
Struggling with aluminium brazing? Contact our experts today for personalized advice and solutions!