Nitrogen is used in sintering due to its inert properties, cost-effectiveness, and ability to enhance material properties. It acts as a protective atmosphere, preventing oxidation and contamination during the sintering process. Nitrogen is particularly beneficial in sintering stainless steels, where it can act as a solid solution strengthening agent. However, its use requires careful control of cooling rates to avoid chromium nitride precipitation, which can compromise corrosion resistance. Nitrogen-based atmospheres are also effective in regulating process factors like decarburization and deoxidization, ensuring high-quality sintered products. Overall, nitrogen is a versatile and economical choice for sintering applications, provided process parameters are well-managed.
Key Points Explained:
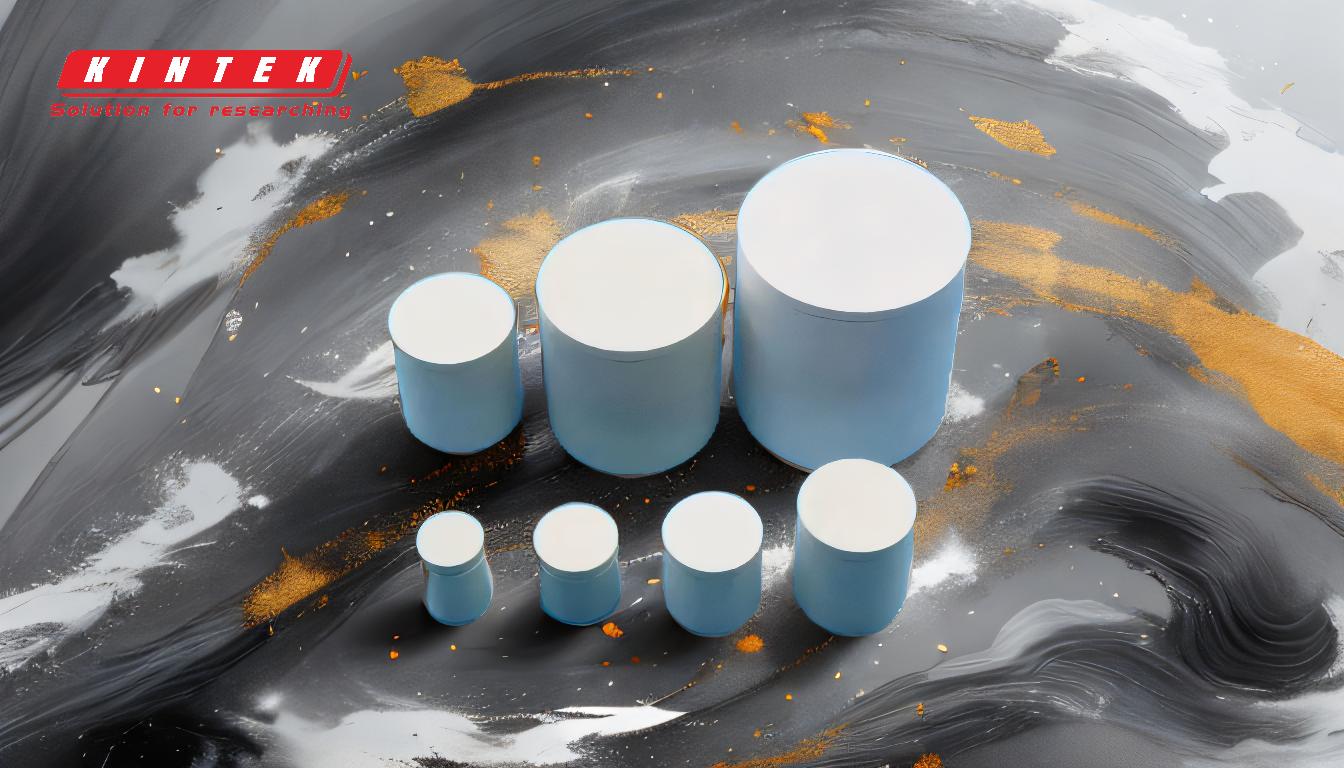
-
Inert/Protective Atmosphere:
- Nitrogen is an inert gas, meaning it does not readily react with other substances. This property makes it ideal for creating a protective atmosphere during sintering, preventing oxidation and contamination of the metal powders being sintered.
- The use of nitrogen helps maintain the integrity and quality of the sintered product by shielding it from reactive gases like oxygen, which could otherwise degrade the material.
-
Cost-Effectiveness:
- Nitrogen is relatively inexpensive compared to other inert gases like argon. Its cost-effectiveness makes it a preferred choice for many industrial sintering processes.
- The ability to generate nitrogen on-site further reduces costs, making it an economical option for large-scale operations.
-
Solid Solution Strengthening in Austenitic Stainless Steels:
- Nitrogen is soluble in the steel matrix, particularly in austenitic stainless steels. This solubility allows nitrogen to act as a solid solution strengthening agent, enhancing the mechanical properties of the steel.
- The presence of nitrogen in the steel matrix can improve hardness, strength, and wear resistance, making it beneficial for certain applications.
-
Risk of Chromium Nitride Precipitation:
- At high temperatures, nitrogen can form nitrides, particularly chromium nitrides, in stainless steels. This precipitation can negatively affect the corrosion resistance of the material.
- To mitigate this risk, high cooling rates are often employed during the sintering process to minimize the formation of chromium nitrides.
-
Regulation of Process Factors:
- Nitrogen-based atmospheres can be used to regulate critical process factors such as decarburization and deoxidization. These factors are essential for maintaining the desired carbon content and ensuring the metal is free from oxides.
- By controlling these factors, nitrogen helps produce high-quality sintered products with consistent properties.
-
Versatility in Applications:
- Nitrogen is widely used in various fields, including metal heat treatment, powder metallurgy, magnetic materials, and semiconductor manufacturing. Its versatility makes it a valuable resource in many industrial processes.
- In addition to sintering, nitrogen is used as a protective gas in annealing, nitride treatment, and furnace purging, further highlighting its broad applicability.
-
Use in Nitrogen-Based Mixtures:
- Nitrogen-based mixtures are particularly useful in cases where high cooling rates can be achieved, and the risk of chromium nitride precipitation is minimal. These mixtures provide an effective and economical solution for sintering a wide range of materials.
- The choice of nitrogen-based mixtures depends on the specific requirements of the sintering process and the materials being used.
In summary, nitrogen is a crucial component in sintering due to its inert nature, cost-effectiveness, and ability to enhance material properties. However, its use requires careful management of process parameters, particularly cooling rates, to avoid detrimental effects like chromium nitride precipitation. By understanding and controlling these factors, nitrogen can be effectively utilized to produce high-quality sintered products across various industries.
Summary Table:
Key Aspect | Description |
---|---|
Inert/Protective Atmosphere | Prevents oxidation and contamination during sintering. |
Cost-Effectiveness | Economical compared to other inert gases; can be generated on-site. |
Solid Solution Strengthening | Enhances hardness, strength, and wear resistance in stainless steels. |
Risk of Chromium Nitride | Requires controlled cooling to avoid compromising corrosion resistance. |
Regulation of Process Factors | Controls decarburization and deoxidization for high-quality sintered products. |
Versatility | Used in heat treatment, powder metallurgy, magnetic materials, and more. |
Nitrogen-Based Mixtures | Effective for sintering with high cooling rates and minimal chromium nitride risk. |
Want to optimize your sintering process with nitrogen? Contact our experts today for tailored solutions!