Physical Vapor Deposition (PVD) is a coating process that transforms solid materials into a vapor phase, which then condenses onto a substrate to form a thin, durable, and high-performance coating. This method is widely used in industries requiring corrosion resistance, abrasion resistance, and high-temperature tolerance. PVD is environmentally friendly compared to traditional coating techniques like electroplating and painting, as it avoids harmful chemicals and reduces waste. It is versatile, allowing the deposition of nearly any inorganic material and some organic materials, and offers precise control over coating composition and thickness. PVD is particularly valued for its ability to create long-lasting, high-quality coatings that rarely require additional protective layers.
Key Points Explained:
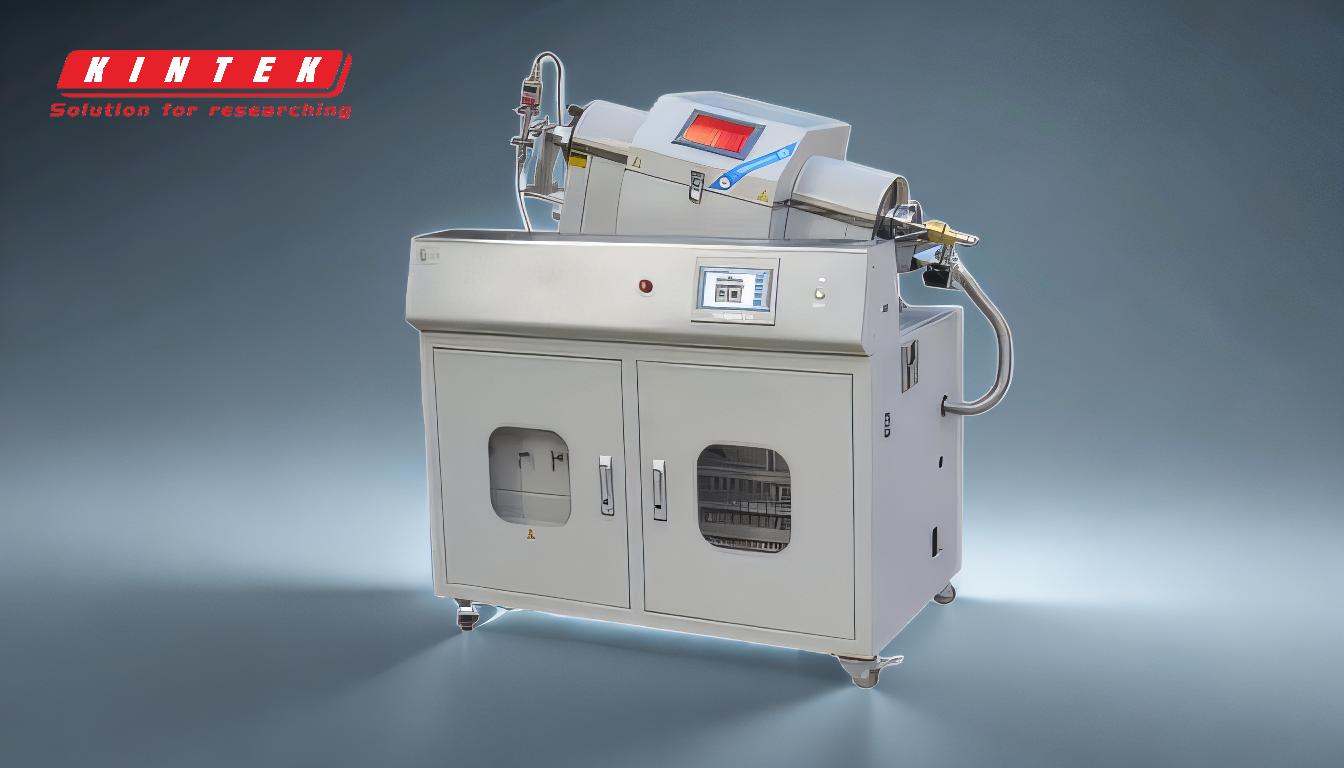
-
Process of PVD:
- PVD involves converting a solid material into a vapor phase through methods like thermal evaporation or sputtering.
- The vaporized material travels through a low-pressure chamber and condenses onto a substrate, forming a thin film coating.
- This process is typically carried out in a controlled environment with temperatures ranging from 50 to 600 degrees Celsius.
-
Advantages of PVD:
- Durability and Resistance: PVD coatings are highly durable, corrosion-resistant, and can withstand high temperatures and mechanical impacts.
- Versatility: Almost any inorganic material and some organic materials can be deposited using PVD, making it suitable for a wide range of applications.
- Environmental Friendliness: PVD is less harmful to the environment compared to traditional coating methods like electroplating, as it does not require chemical reagents or post-treatment cleaning.
- Precision and Control: The process allows for precise control over the composition and thickness of the coatings, ensuring consistent quality.
-
Applications of PVD:
- PVD is used in various industries, including aerospace, automotive, medical devices, and electronics, to enhance the performance and longevity of components.
- It is particularly useful for creating coatings that require high abrasion resistance, such as cutting tools and wear-resistant parts.
-
Comparison with Other Coating Methods:
- Electroplating: Unlike electroplating, which involves chemical baths and can produce hazardous waste, PVD is a dry process that minimizes environmental impact.
- Painting: PVD coatings are more durable and resistant to wear and corrosion compared to traditional paint coatings, and they do not require protective topcoats.
-
Types of PVD Techniques:
- Sputtering: A technique where atoms are ejected from a solid target material due to bombardment by energetic ions, which then deposit onto the substrate.
- Thermal Evaporation: Involves heating the target material until it vaporizes, and the vapor then condenses onto the substrate.
-
Benefits for Equipment and Consumable Purchasers:
- PVD coatings can significantly extend the lifespan of equipment and consumables by providing superior protection against wear, corrosion, and high temperatures.
- The environmental benefits of PVD can help companies meet regulatory requirements and reduce their ecological footprint.
- The versatility and precision of PVD allow for customization of coatings to meet specific performance requirements, offering a cost-effective solution for enhancing product quality.
In summary, Physical Vapor Deposition (PVD) is a highly effective and environmentally friendly coating process that offers numerous advantages in terms of durability, versatility, and precision. Its applications span across various industries, providing long-lasting and high-performance coatings that meet the demanding requirements of modern technology and manufacturing.
Summary Table:
Aspect | Details |
---|---|
Process | Converts solid materials into vapor, condenses onto substrate as thin film. |
Advantages | Durable, corrosion-resistant, versatile, precise, eco-friendly. |
Applications | Aerospace, automotive, medical devices, electronics, cutting tools. |
Comparison | Superior to electroplating and painting in durability and environmental impact. |
Techniques | Sputtering, thermal evaporation. |
Benefits for Buyers | Extends equipment lifespan, meets regulatory standards, cost-effective. |
Discover how PVD coatings can enhance your products—contact us today for expert advice!