Stainless steel is harder to work with compared to other metals due to its unique properties, such as high strength, work hardening tendency, and resistance to corrosion. These characteristics make it more challenging to cut, shape, and weld. Its high chromium content contributes to its hardness and durability, but also increases its resistance to deformation. Additionally, stainless steel generates more heat during machining, which can lead to tool wear and requires specialized equipment and techniques. Understanding these factors is crucial for effectively working with stainless steel in manufacturing and construction.
Key Points Explained:
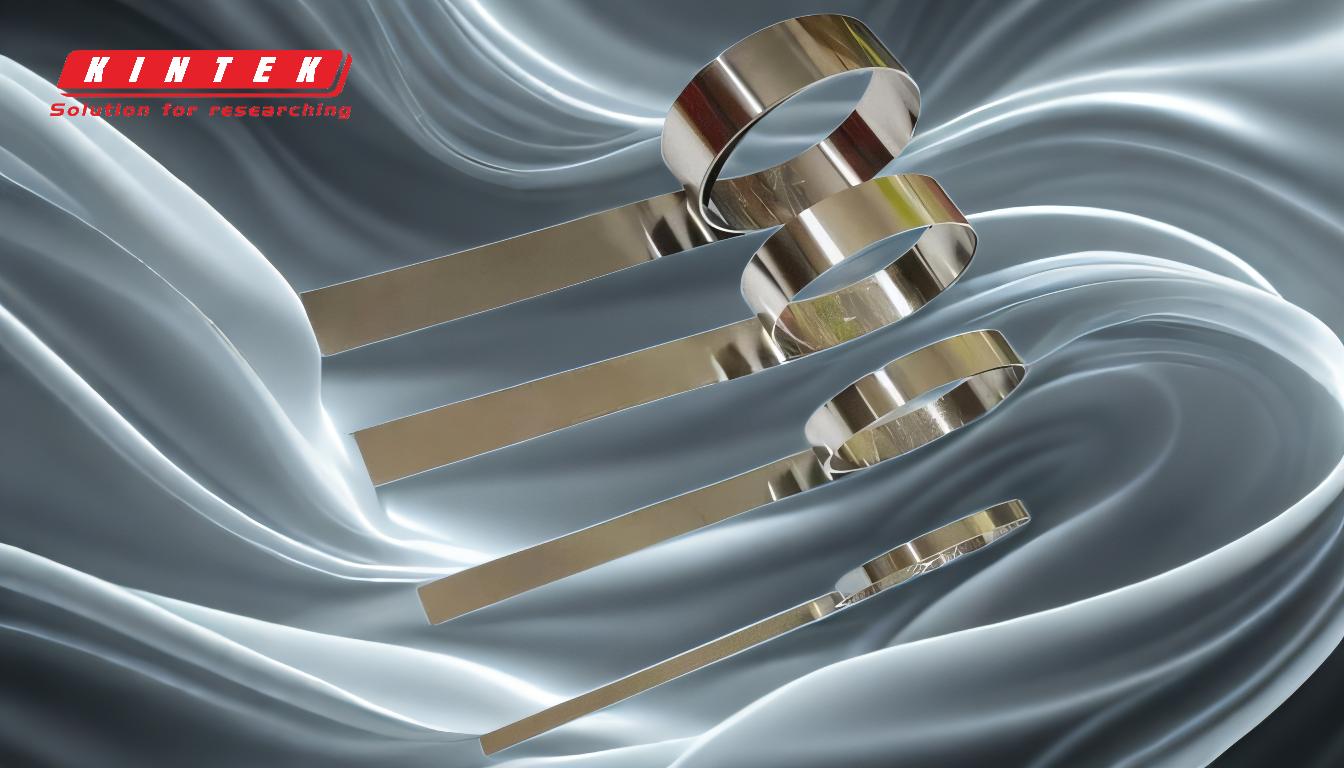
-
High Strength and Hardness
- Stainless steel contains a significant amount of chromium, which forms a passive oxide layer that enhances its hardness and resistance to wear.
- This hardness makes it more difficult to cut, drill, or shape compared to softer metals like aluminum or mild steel.
- Tools used for working with stainless steel must be made of harder materials, such as carbide, to withstand the stress and avoid premature wear.
-
Work Hardening Tendency
- Stainless steel has a tendency to work harden, meaning it becomes harder and more brittle as it is deformed or machined.
- This property requires careful handling during processes like bending or cutting to avoid cracking or excessive tool wear.
- Slower machining speeds and proper lubrication are often necessary to manage work hardening.
-
Heat Generation During Machining
- Stainless steel's high thermal conductivity is lower than that of metals like aluminum, causing heat to concentrate at the cutting point.
- Excessive heat can damage tools and affect the material's structural integrity.
- Coolants and specialized cutting fluids are often used to dissipate heat and prolong tool life.
-
Corrosion Resistance and Surface Finish
- While stainless steel's corrosion resistance is a benefit, it also makes it more challenging to weld or join.
- The oxide layer must be properly cleaned before welding to ensure strong, defect-free joints.
- Achieving a smooth surface finish often requires additional polishing or grinding steps.
-
Specialized Equipment and Techniques
- Working with stainless steel often requires specialized tools, such as high-speed steel or carbide-tipped cutting tools.
- Techniques like slow and steady machining, proper cooling, and precise control of cutting parameters are essential.
- Welders must use techniques like TIG (Tungsten Inert Gas) welding to maintain the material's corrosion resistance.
-
Cost and Expertise Requirements
- The difficulty of working with stainless steel often translates to higher costs for labor, tools, and equipment.
- Skilled operators with experience in handling stainless steel are essential to achieve high-quality results.
- Training and expertise are critical to overcoming the challenges posed by this material.
By understanding these challenges and applying the appropriate techniques and tools, stainless steel can be effectively worked with to produce durable and high-quality products.
Summary Table:
Key Challenge | Explanation | Solution |
---|---|---|
High Strength and Hardness | Harder to cut, drill, or shape; requires carbide tools. | Use harder tools like carbide and apply steady pressure. |
Work Hardening Tendency | Becomes harder and brittle during machining. | Use slower speeds, proper lubrication, and avoid excessive deformation. |
Heat Generation | Concentrated heat damages tools and material. | Use coolants, cutting fluids, and manage machining speeds. |
Corrosion Resistance | Oxide layer complicates welding and surface finishing. | Clean surfaces before welding and use TIG welding techniques. |
Specialized Equipment | Requires high-speed steel or carbide tools and precise techniques. | Invest in specialized tools and train operators for precise control. |
Cost and Expertise | Higher labor, tool, and equipment costs; skilled operators required. | Train staff and budget for specialized tools and techniques. |
Need help working with stainless steel? Contact our experts today for tailored solutions and advice!