Zirconia is sintered primarily to enhance its mechanical properties, such as strength, density, and structural integrity. The sintering process involves heating zirconia to high temperatures without melting it, which reduces porosity and binds the material into a unified mass. This process is critical for achieving the final hardness and durability required for applications like dental restorations, industrial components, and other high-performance uses. Sintering also ensures cost-effectiveness and versatility, making it a preferred method for producing zirconia-based products.
Key Points Explained:
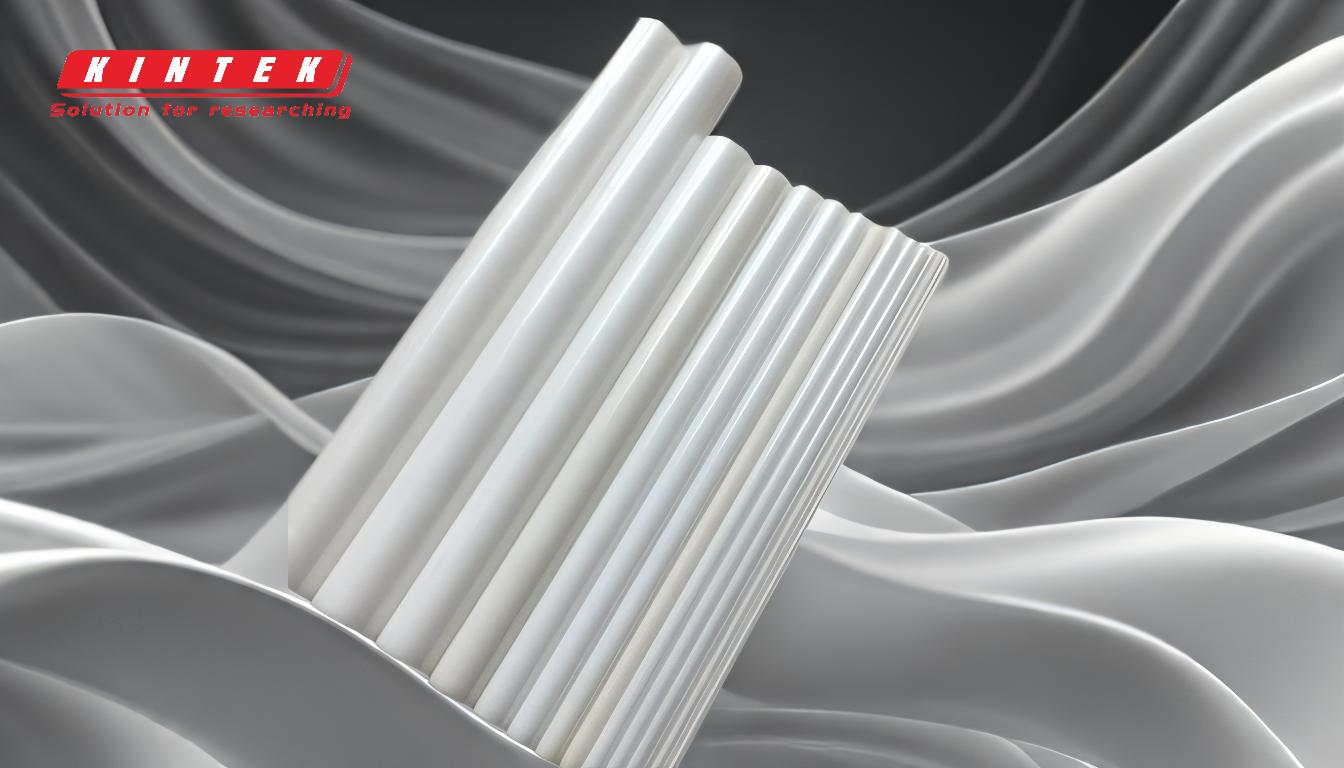
-
Reduction of Porosity and Increased Density:
- Sintering significantly reduces the porosity of zirconia, leading to a denser material. This is crucial because porosity can weaken the material, making it less durable and more prone to failure. By eliminating voids and increasing density, sintering enhances the overall strength and hardness of zirconia, making it suitable for demanding applications.
-
Enhancement of Mechanical Properties:
- The sintering process improves zirconia's mechanical properties, such as its strength and structural integrity. This is achieved through the application of heat and sometimes pressure, which binds the zirconia particles together without melting them. The result is a material that is both strong and durable, ideal for use in dental restorations and industrial components.
-
Linear Sintering Shrinkage:
- Zirconia undergoes significant shrinkage during sintering. This shrinkage is predictable and can be controlled, which is essential for manufacturing precise components like dental crowns and bridges. Understanding and managing this shrinkage ensures that the final product meets the required specifications and fits perfectly in its intended application.
-
Cost-Effectiveness and Efficiency:
- Sintering is a cost-effective and efficient process. It allows for the production of high-quality zirconia products without the need for melting, which can be energy-intensive and expensive. The versatility of sintering also means it can be used across various industries, from dentistry to manufacturing, making it a widely adopted technique.
-
Versatility Across Industries:
- The sintering process is highly versatile and has applications in many industries. For example, it is used to produce gears, couplings, bearings, and other mechanical components. In dentistry, sintering furnaces have revolutionized the production of zirconia restorations, making it faster and easier to create strong and durable dental prosthetics.
-
Clinical Suitability:
- The sintering behavior of zirconia is critical for its clinical suitability. By comparing the sintering shrinkage and mechanical properties of different zirconia blocks, manufacturers can ensure that the material meets the standards required for medical and dental applications. This ensures that the final product is both safe and effective for patient use.
In summary, sintering zirconia is essential for transforming it into a high-performance material with reduced porosity, increased density, and enhanced mechanical properties. This process not only improves the material's strength and durability but also ensures its suitability for a wide range of applications, from industrial components to dental restorations.
Summary Table:
Key Benefit | Description |
---|---|
Reduction of Porosity | Eliminates voids, increasing density and strength for demanding applications. |
Enhanced Mechanical Properties | Improves strength, durability, and structural integrity without melting. |
Linear Sintering Shrinkage | Predictable shrinkage ensures precision in dental and industrial components. |
Cost-Effectiveness | Energy-efficient process for high-quality zirconia production. |
Versatility Across Industries | Used in dentistry (crowns, bridges) and manufacturing (gears, bearings). |
Clinical Suitability | Ensures safe, effective zirconia products for medical and dental applications. |
Learn how sintering can optimize your zirconia products—contact our experts today!