Nitrogen is widely used in the annealing process due to its ability to create an inert atmosphere that prevents oxidation and decarburization of materials. This is particularly important in metal heat treatment, powder metallurgy, and other industrial processes where maintaining the integrity and quality of the material is crucial. Nitrogen annealing is beneficial for a variety of materials, including ferrous and non-ferrous metals, and is used in processes like bright annealing, neutral hardening, and sintering. Its inert nature ensures that the material does not react with oxygen, which could otherwise degrade the material's properties. Additionally, nitrogen is cost-effective and readily available, making it a practical choice for industrial applications.
Key Points Explained:
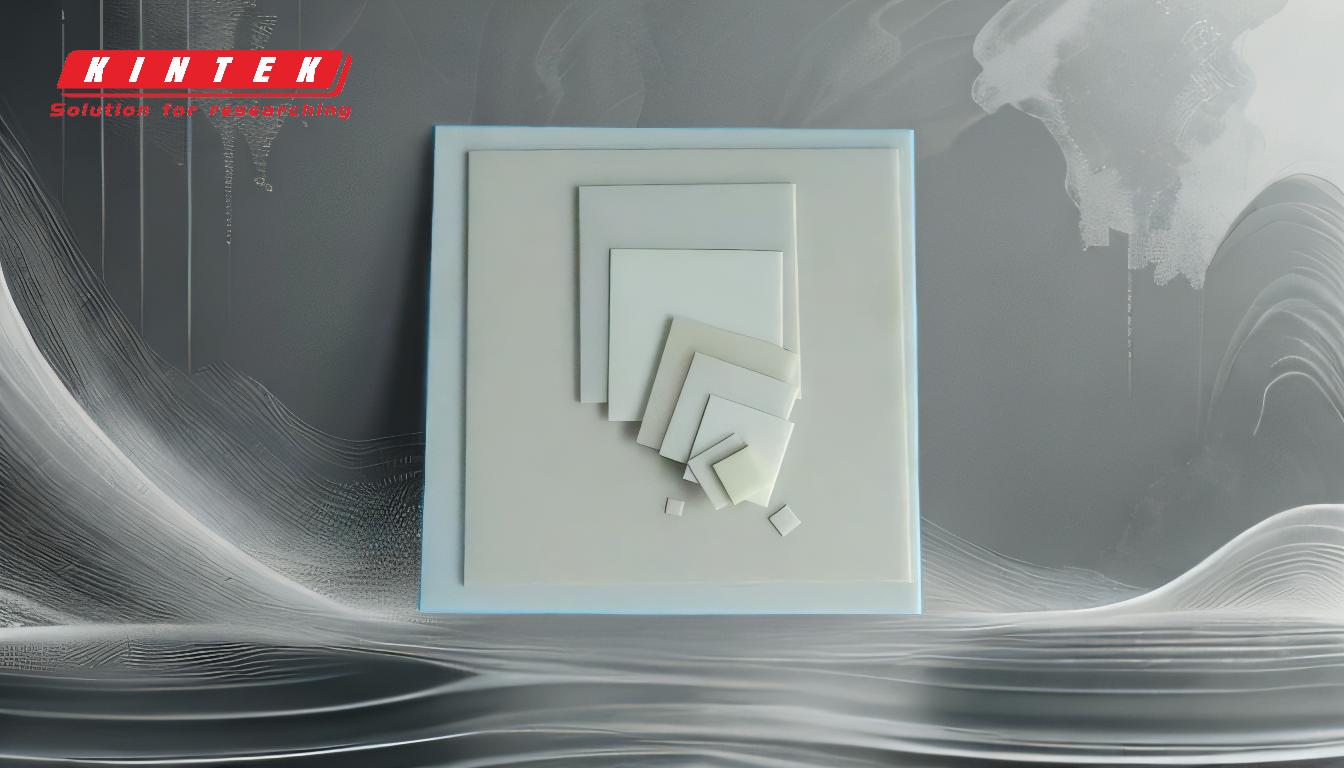
-
Prevention of Oxidation:
- During the annealing process, materials are heated to high temperatures, which makes them susceptible to oxidation when exposed to oxygen. Oxidation can lead to the formation of oxides on the surface of the material, degrading its quality and performance.
- Nitrogen, being an inert gas, does not react with the material, thus preventing oxidation. This is particularly important for metals like steel, copper, and aluminum, where surface integrity is critical.
-
Creation of an Inert Atmosphere:
- Nitrogen is used to create an inert atmosphere within the annealing furnace. This inert environment ensures that no unwanted chemical reactions occur during the heating and cooling phases.
- An inert atmosphere is essential for processes like bright annealing, where the goal is to maintain the material's surface brightness and prevent discoloration.
-
Decarburization Prevention:
- Decarburization is a process where carbon is lost from the surface of steel or other carbon-containing materials, leading to a reduction in hardness and strength.
- Nitrogen helps in preventing decarburization by maintaining a neutral environment that does not allow carbon to escape from the material. This is crucial for maintaining the mechanical properties of the material.
-
Versatility in Applications:
- Nitrogen annealing is used in a wide range of applications, including the heat treatment of tools, screws, springs, bearings, and non-ferrous metals like copper and aluminum.
- It is also employed in specialized processes like nitriding, carbonitriding, and sintering, where maintaining a controlled atmosphere is essential for achieving the desired material properties.
-
Cost-Effectiveness and Availability:
- Nitrogen is relatively inexpensive and readily available, making it a practical choice for industrial applications. Its widespread use in various industries is also due to its safety and ease of handling compared to other gases like hydrogen.
- The cost-effectiveness of nitrogen makes it a preferred option for large-scale industrial processes where the volume of gas required is significant.
-
Comparison with Hydrogen:
- While hydrogen has a higher heat transfer coefficient and can make the annealing process more efficient, it is more reactive and poses safety risks, such as flammability.
- Nitrogen, on the other hand, is safer to handle and provides a more stable environment for annealing, especially in processes where the risk of oxidation is high.
-
Use in Specialized Processes:
- Nitrogen is also used in specialized heat treatment processes like bright quenching and plasma cutting, where maintaining a non-reactive atmosphere is crucial.
- In these processes, nitrogen ensures that the material's surface remains free from oxides and other contaminants, resulting in a higher-quality finish.
In summary, nitrogen is used in the annealing process primarily to prevent oxidation and decarburization, create an inert atmosphere, and maintain the material's integrity. Its versatility, cost-effectiveness, and safety make it an ideal choice for a wide range of industrial applications.
Summary Table:
Key Benefit | Description |
---|---|
Prevents Oxidation | Nitrogen creates an inert atmosphere, preventing material degradation. |
Avoids Decarburization | Maintains carbon content, preserving hardness and strength of materials. |
Versatile Applications | Used in bright annealing, sintering, and heat treatment of metals. |
Cost-Effective & Safe | Affordable, readily available, and safer than reactive gases like hydrogen. |
Specialized Processes | Ideal for bright quenching, plasma cutting, and maintaining surface integrity. |
Learn how nitrogen annealing can improve your industrial processes—contact our experts today!