Silicone oil is a preferred fluid for diffusion pumps because of its unique properties, which make it highly effective and reliable in creating and maintaining high vacuum environments. Its high vapor point ensures efficient operation at elevated temperatures, while its chemical stability allows it to perform consistently over long periods without significant degradation. Additionally, silicone oil's relatively low toxicity and flammability make it a safer choice compared to other fluids. These characteristics collectively make silicone oil an ideal working fluid for diffusion pumps, ensuring both performance and safety in industrial and scientific applications.
Key Points Explained:
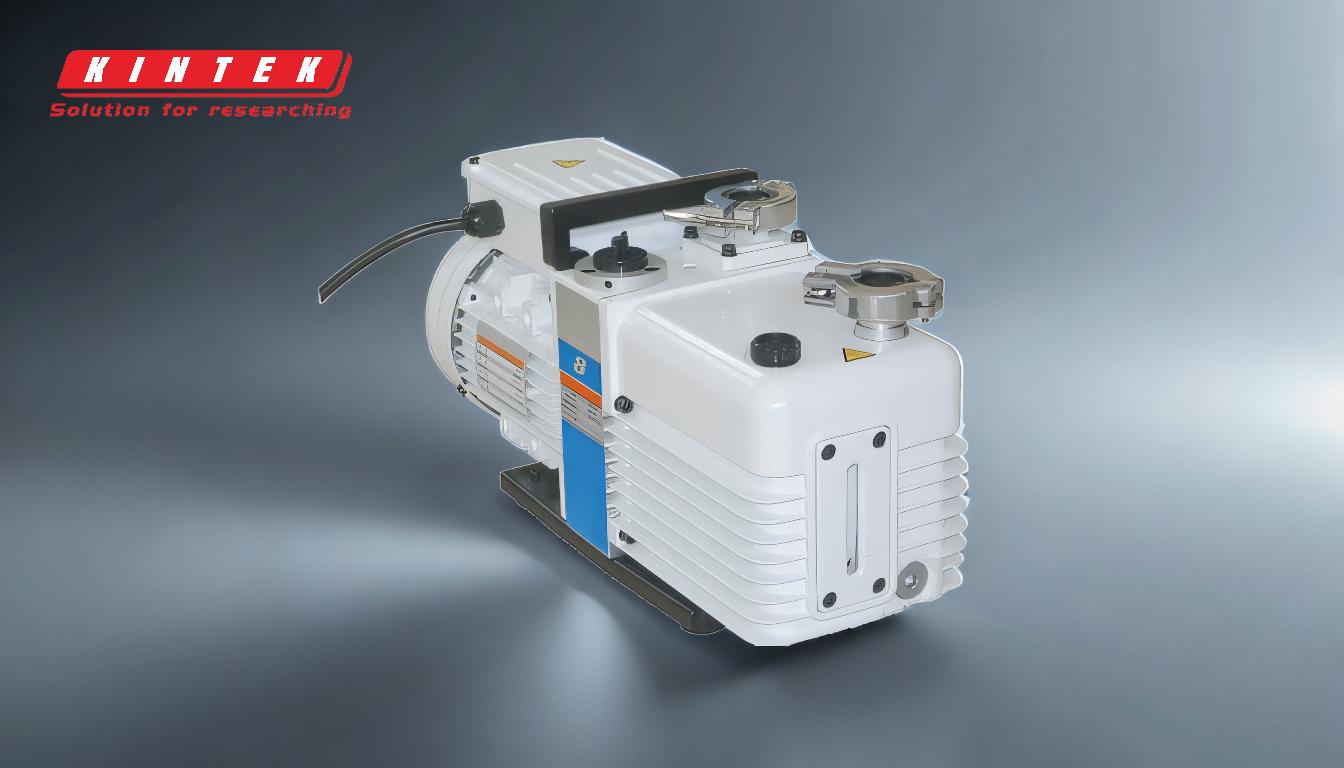
-
High Vapor Point:
- Silicone oil has a high vapor point, which means it can withstand elevated temperatures without evaporating excessively. This is crucial for diffusion pumps, as they operate by heating the fluid to create a high-speed vapor jet that captures and removes gas molecules from the vacuum chamber.
- The high vapor point ensures that the oil remains stable and effective at the high temperatures required for efficient pump operation, preventing breakdown or loss of fluid during use.
-
Chemical Stability:
- Silicone oil is chemically stable, meaning it does not react with other substances or degrade easily under normal operating conditions. This stability is essential for maintaining consistent performance over long periods.
- Unlike some other fluids, silicone oil does not decompose or form harmful byproducts when exposed to heat or vacuum conditions, ensuring a clean and reliable vacuum environment.
-
Low Toxicity and Flammability:
- Compared to alternative fluids like hydrocarbon oils, silicone oil has a relatively low toxicity and flammability profile. This makes it safer to handle and reduces the risk of accidents or health hazards in the workplace.
- Its low flammability is particularly important in high-temperature applications, where the risk of ignition must be minimized to ensure operational safety.
-
Long-Term Performance:
- Silicone oil is known for its durability and ability to perform well over extended periods with minimal degradation. This reduces the need for frequent maintenance or fluid replacement, lowering operational costs.
- Its resistance to breakdown under heat and vacuum conditions ensures that the pump maintains its efficiency and effectiveness over time, making it a cost-effective choice for long-term use.
-
Environmental and Safety Considerations:
- The use of silicone oil aligns with environmental and safety regulations due to its non-toxic nature and low environmental impact. This is particularly important in industries where compliance with safety standards is critical.
- Its stability and safety profile also reduce the risk of contamination in sensitive applications, such as semiconductor manufacturing or scientific research, where even minor impurities can have significant consequences.
-
Versatility in Applications:
- Silicone oil's properties make it suitable for a wide range of applications, from industrial vacuum systems to laboratory equipment. Its ability to perform reliably under various conditions ensures its widespread use in different fields.
- Whether in high-temperature environments or applications requiring long-term stability, silicone oil consistently delivers the performance needed for effective vacuum generation.
In summary, silicone oil's high vapor point, chemical stability, low toxicity, and long-term performance make it an ideal choice for diffusion pumps. These properties ensure efficient and safe operation, making silicone oil a preferred fluid in both industrial and scientific settings.
Summary Table:
Property | Benefit |
---|---|
High Vapor Point | Ensures stability at high temperatures, preventing fluid breakdown. |
Chemical Stability | Resists degradation, maintaining consistent performance over time. |
Low Toxicity & Flammability | Safer handling and reduced risk of accidents in high-temperature applications. |
Long-Term Performance | Durable and cost-effective, requiring minimal maintenance or replacement. |
Environmental Safety | Complies with safety standards, reducing contamination risks. |
Versatility | Suitable for industrial and scientific applications, ensuring reliability. |
Learn more about how silicone oil can optimize your diffusion pump performance—contact our experts today!