Yes, an induction heater can heat brass. Induction heating works by generating eddy currents within conductive materials, causing them to heat up due to electrical resistance. Brass, being a conductive metal alloy primarily composed of copper and zinc, is suitable for induction heating. This method is efficient for melting brass and is commonly used in industrial applications for processing non-ferrous metals like brass, copper, and aluminum. Below, I will explain the key points in detail.
Key Points Explained:
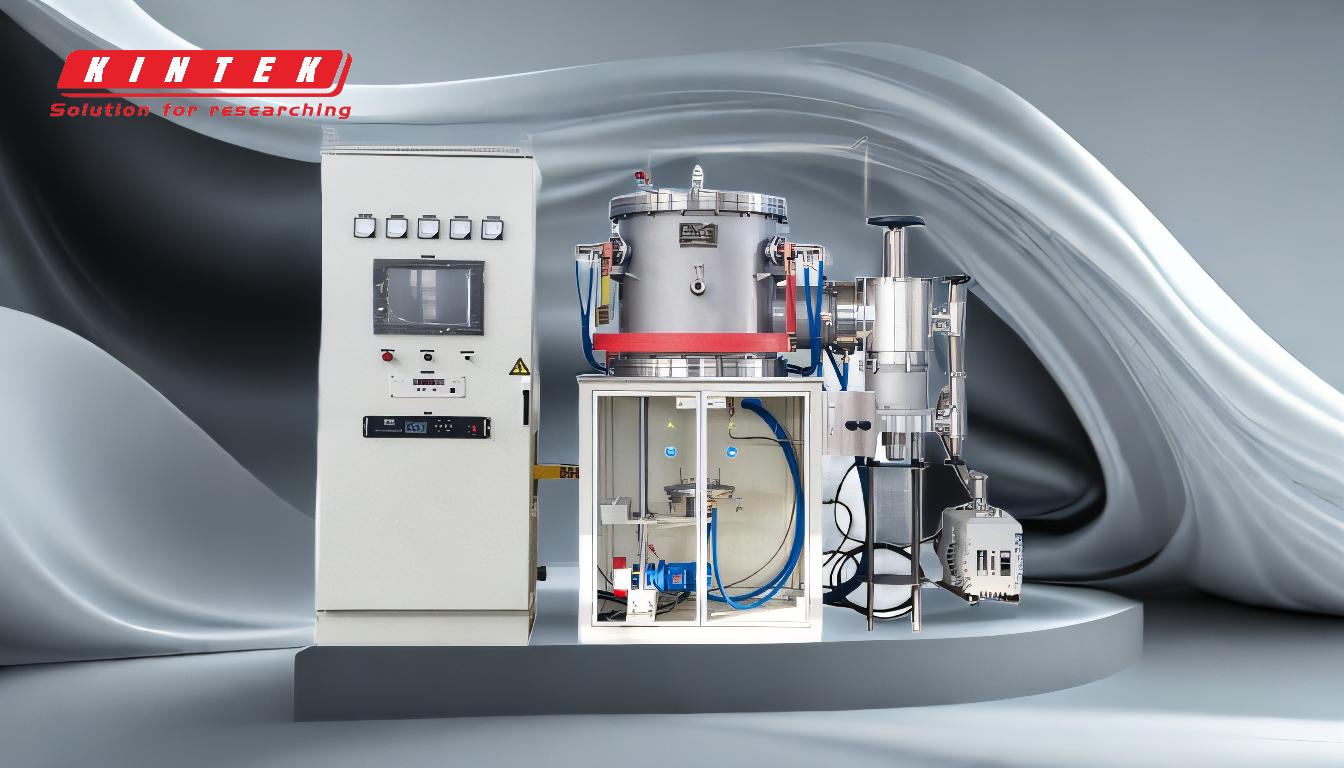
-
Principle of Induction Heating:
- Induction heating relies on electromagnetic induction to generate heat within conductive materials. An alternating current passes through a coil, creating a magnetic field. When a conductive material (like brass) is placed within this field, eddy currents are induced, causing the material to heat up due to its electrical resistance.
- This method is highly efficient because it directly heats the material without requiring an external heat source, making it ideal for metals like brass.
-
Brass as a Conductive Material:
- Brass is an alloy composed mainly of copper (60-70%) and zinc (30-40%), both of which are highly conductive metals. This conductivity makes brass an excellent candidate for induction heating.
- The electrical resistance of brass ensures that the induced eddy currents generate sufficient heat for melting or heating purposes.
-
Applications of Induction Heating for Brass:
- Induction heating is widely used in industries for melting and processing brass. This includes applications such as:
- Melting brass for casting or alloy production.
- Heat treatment processes like annealing or brazing.
- Precision heating for manufacturing components.
- The ability to control the heating process precisely makes induction heating suitable for both small-scale and large-scale brass processing.
- Induction heating is widely used in industries for melting and processing brass. This includes applications such as:
-
Advantages of Using Induction Heating for Brass:
- Efficiency: Induction heating directly heats the brass, minimizing energy loss and reducing heating times.
- Precision: The process allows for precise temperature control, which is critical for applications like annealing or brazing.
- Cleanliness: Since induction heating does not require direct contact with a flame or heating element, it produces a cleaner process with minimal oxidation or contamination.
- Safety: The absence of open flames or hot surfaces reduces the risk of accidents in industrial settings.
-
Limitations and Considerations:
- While induction heating is effective for brass, the efficiency depends on factors such as the alloy composition, the size and shape of the brass piece, and the frequency of the induction heater.
- For example, brass with higher zinc content may have slightly different heating characteristics compared to brass with higher copper content.
- Additionally, the induction heater must be appropriately sized and configured for the specific application to ensure optimal performance.
-
Comparison with Other Heating Methods:
- Induction heating is often preferred over traditional methods like gas or electric furnaces for brass due to its speed, efficiency, and precision.
- Unlike flame heating, induction heating does not produce harmful emissions, making it more environmentally friendly.
- It also eliminates the need for preheating or prolonged heating cycles, reducing overall processing time.
-
Industrial Use Cases:
- Induction heating is commonly used in industries such as:
- Jewelry manufacturing (for brass components).
- Automotive and aerospace (for brass fittings and parts).
- Foundries (for melting and casting brass alloys).
- The versatility of induction heating makes it a valuable tool for various brass-related processes.
- Induction heating is commonly used in industries such as:
In summary, induction heating is an effective and efficient method for heating brass due to its conductive properties. It offers numerous advantages, including precision, cleanliness, and safety, making it a preferred choice in industrial applications. However, the specific heating requirements and configuration of the induction heater must be carefully considered to achieve optimal results.
Summary Table:
Key Aspect | Details |
---|---|
Principle of Induction | Generates heat via eddy currents in conductive materials like brass. |
Brass Composition | 60-70% copper, 30-40% zinc—highly conductive for efficient heating. |
Applications | Melting, annealing, brazing, and precision heating for industrial processes. |
Advantages | Efficiency, precision, cleanliness, and safety. |
Limitations | Depends on alloy composition, size, shape, and heater configuration. |
Industrial Use Cases | Jewelry, automotive, aerospace, and foundries. |
Ready to optimize your brass heating process? Contact our experts today to learn more about induction heating solutions!