Overview of Cold Isostatic Pressing
Table of Contents
- Overview of Cold Isostatic Pressing
- Comparison of Cold Isostatic Pressing with Die Pressing
- Cold Isostatic Pressing in Large Volume Production
- Process and Material Requirements of Cold Isostatic Pressing
- Advantages and Disadvantages of Cold Isostatic Pressing for Ceramics
- Industrial Applications of Cold Isostatic Pressing
- Comparison of Cold Isostatic Pressing with Other Compression Technologies
Cold Isostatic Pressing (CIP) is a method of processing materials by compacting powders using liquid pressure. It is similar to metal mold processing and is based on Pascal's law, which states that pressure in an enclosed fluid is transmitted equally in all directions without any change in magnitude.
Definition and description of Cold Isostatic Pressing (CIP)
Cold isostatic pressing involves enclosing powders in an elastomer mold and applying uniform liquid pressure to compress the mold. This results in a highly compact solid material. CIP can be used for various materials such as plastics, graphite, ceramics, powdered metallurgy, and sputtering targets.
Types of CIP: Wet bag and Dry bag
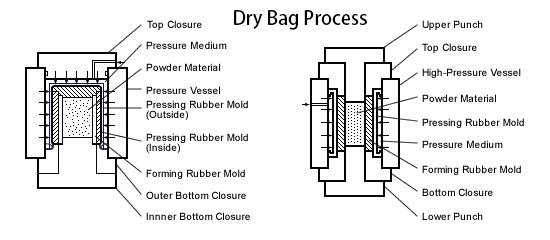
There are two types of cold isostatic pressing:
-
Wet Bag Technology: In this process, the powder is filled in a mold and sealed tightly outside the pressure vessel. The mold is then submerged in the pressure fluid within the vessel, and isostatic pressure is applied to compress the powder into a solid mass. Wet bag technology is not as common as the other type of CIP, but it can be used for various production sizes and shapes.
-
Dry Bag Technology: This process is more suitable for automation and high production rates. The powder is filled in a mold and sealed outside the pressure vessel, similar to the wet bag process. However, the dry bag process lends itself better to automation and can handle longer production runs.
Role of powder quality and tooling design
The quality of the powder used in CIP and the design of the tooling play crucial roles in the success of the process. Powder quality affects the density and integrity of the final compact, while tooling design ensures proper shaping and uniform pressure distribution.
Wet bag isostatic pressing: Concept, advantages, and process
Wet bag isostatic pressing involves submerging a sealed mold filled with powder into a pressure fluid. Isostatic pressure is then applied to compress the powder into a solid shape. This method can approach the theoretical concept of isostatic pressing, resulting in a compact with uniform density and low entrapped stress. Wet bag pressing has the advantage of producing compacts that require minimal machining and exhibit little distortion when fired.
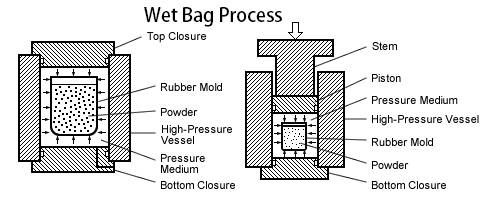
Dry bag isostatic pressing: Suitability for automation and high production rates
Dry bag isostatic pressing is more suitable for automation and high production rates compared to wet bag pressing. The process involves sealing a mold filled with powder outside the pressure vessel. The mold is then loaded into the vessel, pressurized, and unloaded for further post-processing. Although dry bag pressing may require more expensive powder and has lower production rates than other compaction methods, it excels in automation and is well-suited for longer production runs.
In summary, Cold Isostatic Pressing (CIP) is a method of compacting powdered materials using liquid pressure. There are two types of CIP: wet bag and dry bag. Wet bag pressing achieves uniform density and low distortion, while dry bag pressing is more suitable for automation and high production rates. Powder quality and tooling design are important considerations for successful CIP.
Comparison of Cold Isostatic Pressing with Die Pressing
Differences between CIP and die pressing
Cold Isostatic Pressing (CIP) and die pressing are two methods used for materials processing, each with its own advantages and limitations. Understanding the differences between these two techniques can help determine the most suitable method for specific applications.
CIP involves compressing raw powder materials in flexible molds made of elastomer materials such as urethane, rubber, or polyvinyl chloride. The compression is performed at room temperature and uses fluids like oil or water to apply pressure uniformly from all directions.
On the other hand, die pressing, also known as uniaxial pressing, involves compressing dry powders into a die cavity using a rigid mold. The compression is typically applied in a single direction, resulting in non-uniform densities and potential distortions.
Advantages of CIP over uniaxial die pressing: Complex shapes and reduced distortions
One significant advantage of CIP over uniaxial die pressing is the ability to produce complex-shaped components. The flexible molds used in CIP allow for the creation of intricate geometries that would be difficult to achieve with die pressing. This makes CIP particularly suitable for applications requiring intricate or custom-designed components.
Furthermore, CIP minimizes distortions and cracking caused by nonuniform particle packing. The uniform pressure applied from all directions in CIP results in more uniform densities and reduces the potential for structural defects. This is especially critical for complex-shaped components where distortions can compromise the functionality and structural integrity of the final product.
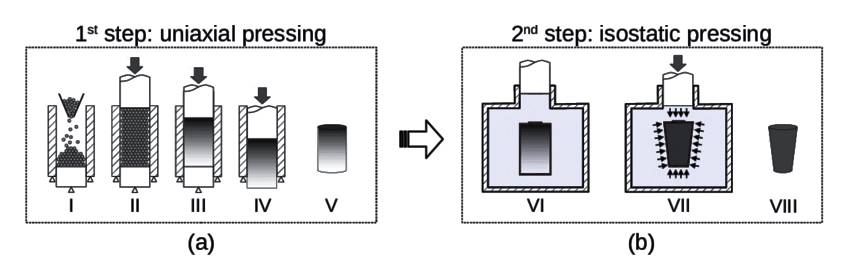
Cold isostatic pressing versus uniaxial molding
Circumstances favoring the use of CIP over uniaxial die pressing
While both CIP and die pressing have their advantages, there are specific circumstances where CIP is the preferred method:
-
Complex shapes: When producing components with intricate geometries or custom designs, CIP offers more flexibility and precision compared to die pressing.
-
Reduced distortions: If the final product requires high dimensional accuracy and minimal distortions, CIP is the preferred method due to its uniform pressure application.
-
Elimination of wax binder: Unlike die pressing, CIP does not require the use of a wax binder. This eliminates the need for dewaxing operations, simplifying the manufacturing process and reducing costs.
-
Uniform shrinkage during sintering: The uniform green density achieved through CIP results in more even shrinkage during the sintering process. This is critical for maintaining good shape control and uniform properties in the final product.
-
Large or small shapes: CIP can be used for both small and large components, making it a versatile method for a wide range of applications.
It is important to note that while CIP offers advantages in terms of shape complexity and reduced distortions, die pressing may still be more suitable for certain applications. Die pressing is often preferred for simple-shaped components, such as thin tiles, where excellent results can be achieved.
In conclusion, understanding the differences between Cold Isostatic Pressing (CIP) and die pressing is crucial for choosing the most appropriate method for specific materials processing applications. CIP excels in producing complex-shaped components with reduced distortions, offering advantages in terms of shape flexibility and dimensional control. However, die pressing may still be preferred for certain applications, especially those requiring high production rates and simple-shaped components.
Cold Isostatic Pressing in Large Volume Production
Role of CIP in the manufacturing of alumina ceramics
Cold Isostatic Pressing (CIP) is a powder-based, near-net-shape technology used for the production of metal and ceramic components. It has been commonly used for processing ceramics, particularly alumina ceramics. CIP allows for the manufacturing of complex-shaped components that are beyond the capabilities of uniaxial die pressing. The process involves sealing powder materials in a forming mold with low deformation resistance, such as a rubber bag, and applying liquid pressure to uniformly compress the molded body. CIP feedstock for alumina ceramics typically includes simple milled Bayer alumina or spray-dried Bayer alumina. This method is commonly used in the production of spark plug insulators, which are some of the largest production-volume CIPed ceramic components globally. Approximately 3 billion spark plug insulators are manufactured annually using CIP.
Use of CIP in the production of spark plug insulators
Spark plug insulators are a prime example of the successful application of CIP in large volume production. These insulators play a crucial role in the ignition process of internal combustion engines. The use of CIP allows for the production of spark plug insulators with complex shapes and high precision. This method ensures the uniform compression of the molded body, resulting in insulators with consistent density and strength. The CIP process is particularly suitable for spark plug insulator production due to the need for complex shapes and the limitations of other methods like injection molding. The high-performance properties and strength requirements of alumina ceramics make CIP an ideal choice for manufacturing spark plug insulators.
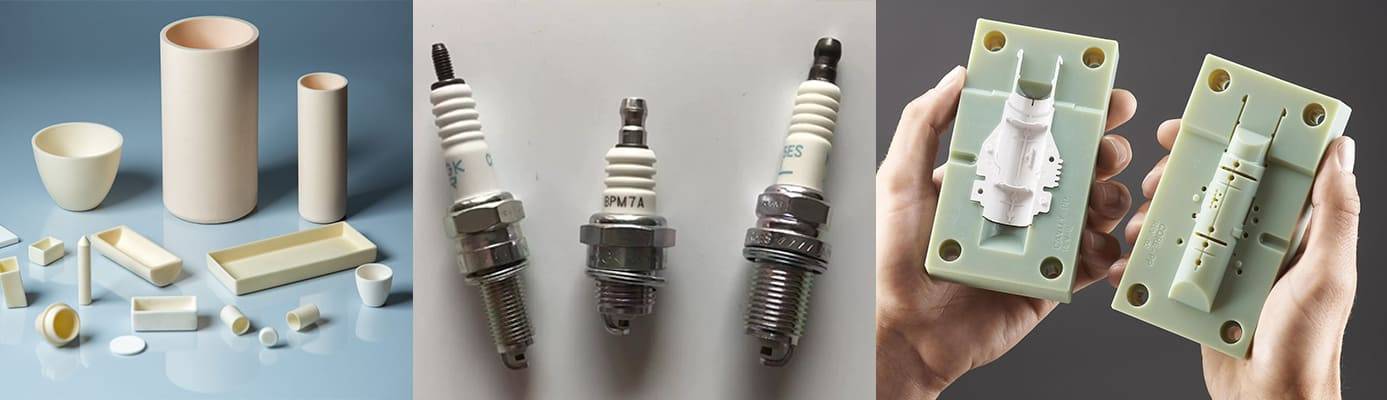
Comparison of CIP with other methods like injection molding
While CIP is an effective method for large volume production of complex-shaped components, injection molding is more commonly used industrially. Injection molding offers advantages such as faster production cycles and lower costs. However, CIP is preferred when very complex shapes are required and injection molding is not practical. CIP allows for the production of parts with concave, hollow, and slender features, making it suitable for applications where other methods may struggle. Additionally, CIP offers advantages such as solid-state processing, uniform microstructure, low tooling cost, and scalability. The ability to produce near-net-shape parts with minimal material waste makes CIP a viable processing route for metals and ceramics in niche applications like aerospace and automotive industries.
In conclusion, Cold Isostatic Pressing (CIP) is a valuable method for large volume production of complex-shaped components, particularly alumina ceramics. It offers advantages such as uniform compression, high precision, and the ability to produce near-net-shape parts. While injection molding is more commonly used, CIP is preferred when very complex shapes are required. The successful application of CIP in the production of spark plug insulators showcases its capabilities in manufacturing high-performance components. Overall, CIP is a reliable and efficient method for meeting the demands of large volume production in various industries.
Process and Material Requirements of Cold Isostatic Pressing
Mechanism of CIP involving uniform pressing
Cold-isostatic pressing (CIP) is a powder-based, near-net-shape technology used for the production of metal and ceramic components. The mechanism of CIP involves applying uniform pressure to powder materials sealed in a forming mold with low deformation resistance, such as a rubber bag. The pressure is transmitted uniformly to the entire surface of the molded body, resulting in a compacted and uniform part.
Importance of controlled rate of pressurization and depressurization
In CIP, the rate of pressurization and depressurization is crucial. A controlled rate ensures uniform compaction and minimizes the risk of defects in the final part. Rapid pressure changes can lead to uneven density distribution and structural weaknesses. Therefore, it is essential to carefully control the rate of pressurization and depressurization to achieve optimal results.
Automation and large-scale application of CIP
With advancements in process capability and powder metallurgy, CIP has become increasingly automated and suitable for large-scale applications. Automation in CIP allows for higher production volumes, improved process control, and reduced labor costs. The scalability of CIP makes it a viable option for industries such as aerospace and automotive, where the production of high-performance metal parts is required.
Cold Isostatic Pressing (CIP) Equipment: Compressing Production Cost!
CIP, or Cold Isostatic Pressing, is a material processing method used for the compaction of powders. It involves confining powders in an elastomer mold and subjecting them to high pressure from all sides. CIP can be utilized with a wide range of materials, including powdered metallurgy, cemented carbides, refractory materials, graphite, ceramics, plastics, and more.
When selecting cold isostatic pressing services, it is important to consider the material capabilities. Different materials and components can be produced using CIP, such as aluminum and magnesium alloys, carbides, cutting tools, carbon and graphite, ceramics, and composites. Some cold isostatic pressing services specialize in specific materials or processes, such as coatings, thermal spray deposits, copper alloys, diamond-like materials, and more.
The pressure range and capacity of cold isostatic pressing services are also important factors to consider. The maximum operating pressure required for part production varies depending on the material and part geometry. The chamber size, including diameter and height, determines the capacity of the service provider.
Cold isostatic pressing is performed at room temperature using a mold made from an elastomer material like urethane, rubber, or polyvinyl chloride. The fluid used in CIP is typically oil or water, and the pressure applied during the operation can range from 60,000 lbs/in2 (400 MPa) to 150,000 lbs/in2 (1000 MPa). It is important to note that CIP may have a disadvantage of low geometric accuracy due to the flexible mold. However, the powder can be compacted uniformly through CIP, and the green compact can then be conventionally sintered to produce the desired final part.
Advantages and Disadvantages of Cold Isostatic Pressing for Ceramics
Benefits of CIP for alumina ceramics compared to other methods
Cold Isostatic Pressing (CIP) is a powder-based, near-net-shape technology that offers several advantages for the production of ceramics, particularly alumina ceramics. Compared to other methods, CIP offers the following benefits:
-
More complex shapes are possible: CIP allows for the production of intricate and complex shapes that may not be achievable through other methods such as uniaxial die pressing.
-
Reduced pressing pressure gradients: CIP greatly reduces the risk of distortion and cracking during the pressing process. This is beneficial for maintaining dimensional integrity and the overall quality of the ceramic components.
-
Low mold cost: CIP is ideal for producing complex parts with small production runs, as it requires low mold cost. Additionally, there is no mold cost for post-CIP, further reducing the overall production expenses.
-
No size limitation: Unlike other ceramic forming methods, CIP does not have a size limitation other than the limits of the press chamber. This makes it suitable for producing very large components, especially those with complex shapes. CIP has been successfully used to produce components weighing over 1 ton.
-
Short processing cycle times: CIP eliminates the need for drying or binder burnout, resulting in shorter processing cycle times. This allows for faster production and increased efficiency.
Powder material pressing: including powder metallurgy, cemented carbides, refractories, graphite, ceramics, plastics, etc.
Limitations of CIP in terms of dimensional control, shape complexity, and powder requirements
While Cold Isostatic Pressing offers several advantages, it also has certain limitations, particularly in terms of dimensional control, shape complexity, and powder requirements. These limitations include:
-
Limited dimensional control: Achieving precise dimensional control can be challenging with CIP. The elastomer mold or sheath used in the process needs to be very thin and of uniform thickness, but even then, high precision is difficult to achieve.
-
Shape complexity limitations: While CIP allows for more complex shapes compared to uniaxial die pressing, it is still inferior to other methods such as Powder Injection Molding (PIM) in terms of shape complexity. PIM offers greater flexibility in producing intricate and highly complex shapes.
-
Powder flowability requirements: Powders used for CIP need to have excellent flowability. This often requires additional processes like spray drying or mold vibration during filling to achieve the necessary flowability. This can increase the overall cost and complexity of the production process.
Despite these limitations, Cold Isostatic Pressing remains a viable option for the production of ceramics, especially alumina ceramics. Its advantages in terms of shape complexity, low tooling cost, and the ability to produce large and complex components make it a desirable choice in certain applications. However, it is important to consider the specific requirements and limitations of CIP when deciding on the most suitable manufacturing method for ceramic components.
Industrial Applications of Cold Isostatic Pressing
Use of CIP for mass production of advanced, complex-shaped ceramics
Cold Isostatic Pressing (CIP) is a powder-based, near-net-shape technology used for the production of metal and ceramic components. While CIP has been commonly used for processing ceramics, recent developments in process capability and powder metallurgy have allowed it to be increasingly used for high-performance metal parts as well.
One of the main advantages of CIP is its ability to produce parts with complex shapes and high precision. This makes it suitable for mass production of advanced ceramics that require intricate designs. The process allows for solid-state processing, resulting in uniform microstructure and excellent mechanical properties.
Specific components produced through CIP
CIP can be used to produce a wide range of components for various industries. Some common examples include:
-
Compression of ceramic powders: CIP is widely used for the consolidation of ceramic powders, such as silicon nitride, silicon carbide, boron nitride, boron carbide, titanium boride, and spinel. The technology allows for the production of high-density ceramic parts with excellent strength and thermal properties.
-
Compression of sputtering targets: CIP is also used for the compression of sputtering targets, which are used in thin film deposition processes. The technology ensures uniform density and excellent adhesion of the target material, resulting in high-quality coatings.
-
Coating of valve components: CIP can be used to coat valve components used in engines to reduce cylinder wear. The process helps to improve the durability and performance of the components, making them suitable for demanding applications in automotive and aerospace industries.
Role of CIP in the alumina industry, specifically in the production of spark plug insulators
In the alumina industry, CIP plays a crucial role in the production of spark plug insulators. Spark plug insulators are critical components used in internal combustion engines to transfer high voltage electricity to the spark plugs. They need to be highly insulating and resistant to high temperatures and mechanical stress.
CIP is used to consolidate alumina powders and form complex-shaped insulators with excellent electrical and thermal properties. The process allows for the production of insulators with high-density and uniform microstructure, ensuring reliable performance in demanding engine environments.
Overall, CIP offers several advantages for industrial applications, including mass production of complex ceramics, production of specific components, and its role in the alumina industry for spark plug insulators. Its ability to produce near-net-shape parts with minimal material waste, combined with low tooling cost and process scalability, makes it a viable processing route for various industries.
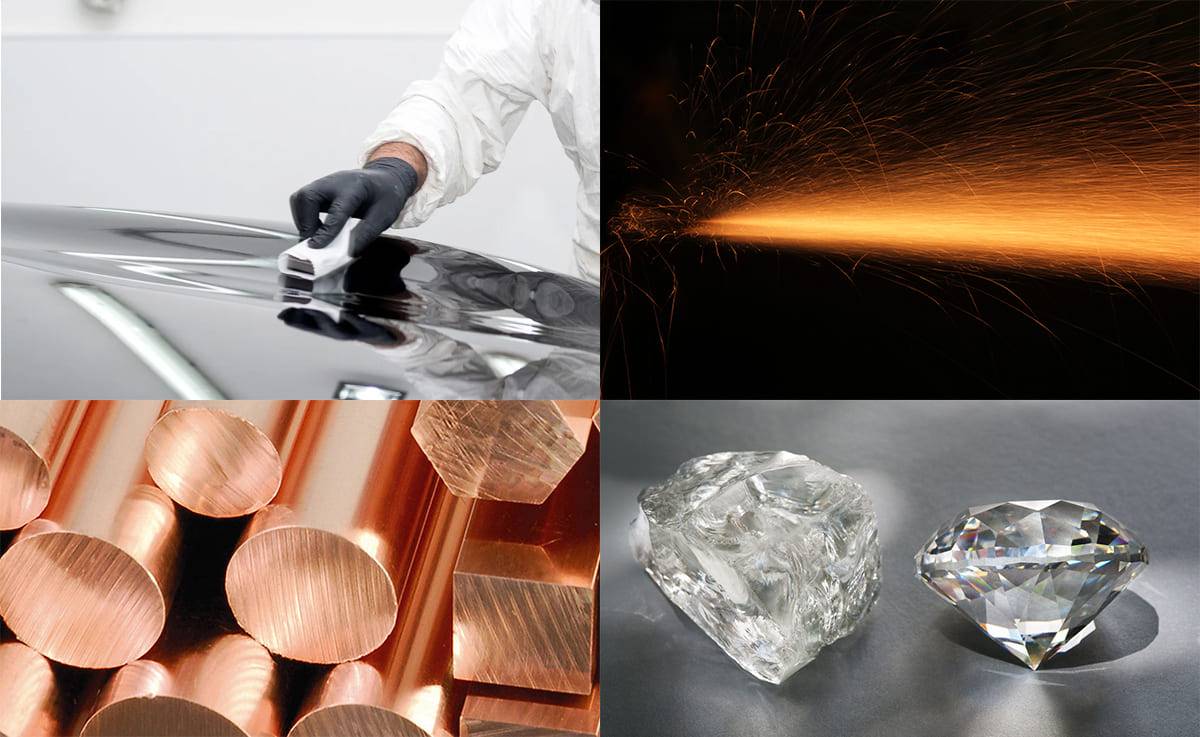
Comparison of Cold Isostatic Pressing with Other Compression Technologies
Cold Isostatic Pressing (CIP)
Cold Isostatic Pressing (CIP) is a powder-compacting process used to obtain 60 to 80% theoretically dense parts ready for sintering. It involves subjecting a material to uniform pressure from all sides by immersing it in a high-pressure fluid medium and applying hydraulic pressure. CIP is particularly effective for shaping and consolidating powdered materials, creating intricate shapes, and achieving high green density.
Cold Isostatic Pressing vs. Hot Isostatic Pressing: A Comparative Overview
In the realm of materials processing, two powerful techniques stand out: Cold Isostatic Pressing (CIP) and Hot Isostatic Pressing (HIP). While both methods share the goal of enhancing material properties, they do so under different conditions, each offering unique advantages.
Cold Isostatic Pressing (CIP) involves subjecting a material to uniform pressure from all sides, creating intricate shapes and achieving high green density. It is particularly effective for shaping and consolidating powdered materials.
Hot Isostatic Pressing (HIP) involves subjecting a material to both high temperature and pressure simultaneously to obtain fully dense parts. It is mainly used for engineered ceramics requiring optimum properties for high-performance applications.
The decision between Cold Isostatic Pressing and Hot Isostatic Pressing depends on the specific goals of your project and the characteristics of the materials involved.
Introduction of Alternative Compression Technologies like Shock Compression
Hot pressing, hot isostatic pressing, and hot extrusion can generate products that are almost fully dense. However, these methods tend to lead to nanograin coarsening, especially during the preparation of compressed MA powders. To overcome this, alternative compression technologies with very short heating times, such as shock compression or shock-wave compaction, have been developed and have achieved some success.
Shock compression involves the generation of a shock wave, characterized by very high pressures, medium temperatures, very short reaction times, and very high strain rates. This technique can severely deform particles, even causing local melting, resulting in fully dense and compacted samples without grain growth. Methods such as air guns and explosive shock waves, previously used for compression of micron-sized powders, are now being used to compress nanopowders.
Application of Shock Compression in the Compaction of Nanopowders
Shock compression technology has proven to be effective in compacting nanopowders. By subjecting the powders to short, high-pressure shock waves, the particles can be fully dense and compact without grain growth. This method offers a promising solution for the compression of nanopowders, allowing for the production of high-quality, fully dense products.
In conclusion, Cold Isostatic Pressing (CIP) offers unique advantages in shaping and consolidating powdered materials, while Hot Isostatic Pressing (HIP) is suitable for obtaining fully dense parts. Alternative compression technologies like shock compression provide a solution for the compaction of nanopowders, ensuring high density and quality in the final products. The choice of compression technology depends on the specific requirements of the project and the materials involved.
CONTACT US FOR A FREE CONSULTATION
KINTEK LAB SOLUTION's products and services have been recognized by customers around the world. Our staff will be happy to assist with any inquiry you might have. Contact us for a free consultation and talk to a product specialist to find the most suitable solution for your application needs!