Overview of CVD Technologies
Introduction to LPCVD, PECVD, and ICPCVD
LPCVD, PECVD, and ICPCVD are three prevalent Chemical Vapor Deposition (CVD) technologies, each distinguished by unique material deposition methods, equipment specifications, and process conditions. These techniques play pivotal roles in various industries, particularly in semiconductor manufacturing, where precise control over film deposition is essential.
LPCVD (Low Pressure Chemical Vapor Deposition) operates under reduced pressure, enhancing gas diffusion and improving film uniformity. This method typically involves high temperatures, which facilitate the formation of dense, high-quality films. LPCVD is particularly favored for its ability to produce uniform films over large substrates, making it ideal for applications in the semiconductor industry.
PECVD (Plasma-Enhanced Chemical Vapor Deposition), on the other hand, utilizes plasma to activate gas-phase reactions at lower temperatures. This technique allows for faster deposition rates and greater process flexibility, making it suitable for a wide range of materials, including silicon nitride and silicon oxide. However, the plasma can introduce defects, affecting film density and quality.
ICPCVD (Inductively Coupled Plasma Chemical Vapor Deposition) represents an advanced form of PECVD, characterized by higher plasma density and more uniform energy distribution. This results in superior film quality and uniformity, even at lower pressures and temperatures. ICPCVD is particularly advantageous for depositing films on complex-shaped surfaces and for applications requiring high-quality, low-temperature films.
Each of these technologies offers distinct advantages and challenges, making them suitable for different applications within the semiconductor and microelectronics industries. Understanding these distinctions is crucial for selecting the most appropriate CVD method for specific manufacturing needs.
LPCVD (Low Pressure Chemical Vapor Deposition)
Principle of LPCVD
Low Pressure Chemical Vapor Deposition (LPCVD) is a specialized CVD process conducted under subatmospheric pressures. The fundamental principle involves introducing reaction gases into a vacuum or low-pressure environment within a reaction chamber. These gases are then subjected to high temperatures, causing them to decompose or react, thereby forming a solid film that is deposited onto the substrate's surface.
The process conditions are meticulously chosen to ensure that the film growth rate is primarily governed by the surface reaction rate, which is highly temperature-dependent. This temperature dependency allows for precise control, leading to exceptional uniformity across the wafer, both within a single wafer and from wafer to wafer, as well as across multiple runs. The ability to fine-tune the process temperature optimizes film quality and yield, making LPCVD a preferred method for applications requiring high-quality, uniform films.
LPCVD's versatility extends to a wide array of applications, including the creation of complex nanostructures and other advanced materials. For instance, the process can be adapted to in-situ cleaning of LPCVD tubes, where an inductive coil is employed within a quartz tube to generate a plasma. This technique, while producing thinner films, yields a higher-quality plasma compared to conventional methods.
Moreover, LPCVD films can be tailored to exhibit specific properties by adjusting the process temperatures. This customization capability ensures that the films meet the exacting standards required for various substrates and applications, from silicon wafers to more intricate designs. The process can be calibrated to achieve desired film thicknesses, further enhancing its utility in precision engineering and material science.
Features of LPCVD
LPCVD operates within a temperature range of 500°C to 900°C and utilizes low-pressure environments, typically from 0.1 to 1 Torr. This combination of high temperature and low pressure results in several notable characteristics:
-
Film Quality: The films produced by LPCVD are of high quality, exhibiting excellent uniformity, good densification, and minimal defects. This is largely due to the controlled environment, which reduces the likelihood of impurities and inconsistencies.
-
Deposition Rate: The deposition process in LPCVD is slower, contributing to a lower deposition rate compared to other CVD methods. While this might seem like a disadvantage, it ensures that the films are more thoroughly and evenly deposited.
-
Homogeneity: LPCVD is particularly well-suited for large-area substrates, providing uniform deposition across extensive surfaces. This makes it a preferred method for applications requiring consistent film thickness over broad areas.
-
Applications: LPCVD is widely used in the semiconductor industry for depositing various layers, including oxides (SiO₂), nitrides (Si₃N₄), and polysilicon. Its ability to produce high-quality films with minimal defects makes it ideal for intricate semiconductor devices.
In summary, LPCVD's unique process conditions not only enhance the quality and uniformity of the deposited films but also make it a versatile technique for a wide array of semiconductor applications.
Advantages and Disadvantages of LPCVD
Advantages:
- High Film Quality: LPCVD operates in a low-pressure environment, which significantly enhances the uniformity and quality of the deposited films. This results in fewer defects and a denser film structure, making it ideal for applications requiring high precision and reliability.
- Strong Step Coverage: LPCVD excels in depositing films on complex three-dimensional structures, providing excellent side wall coverage. This capability is crucial for intricate semiconductor devices where uniform film deposition is essential.
- Cost Efficiency: LPCVD equipment requires lower initial investment and operating costs compared to other technologies. This makes it a cost-effective solution for high-volume production settings.
- Large Area Substrate Compatibility: The process is well-suited for large area substrates, ensuring uniform deposition across extensive surfaces, which is beneficial for mass production environments.
Disadvantages:
- High Temperature Requirement: LPCVD necessitates high temperatures, typically between 500°C and 900°C, which can be problematic for temperature-sensitive substrates. This limitation restricts its applicability in certain material processing scenarios.
- Lower Productivity: The deposition rate of LPCVD is relatively slow, leading to lower overall productivity. This can be a significant drawback in fast-paced manufacturing environments where high throughput is critical.
- High Energy Consumption: The need to maintain a low-pressure environment during the process results in higher energy consumption, adding to the operational costs.
- Consumables Cost: The use of numerous quartz consumables in the LPCVD process increases the overall cost, as these components need periodic replacement and maintenance.
- Plating Issues: There is a risk of deposition occurring in non-target areas, which can affect the consistency and quality of the final product. This necessitates careful monitoring and control during the process.
In summary, while LPCVD offers superior film quality and coverage for large substrates, its high temperature requirements and slower deposition rate pose challenges in specific manufacturing contexts.
PECVD (Plasma-Enhanced Chemical Vapor Deposition)
Principle of PECVD
PECVD (Plasma Enhanced Chemical Vapor Deposition) employs low-temperature plasma to facilitate gas-phase reactions, thereby enabling the deposition of thin films on substrate surfaces at reduced temperatures. This process involves generating a glow discharge within the process chamber under low air pressure, typically at the cathode where the sample is placed. The glow discharge serves to heat the sample to a predetermined temperature, after which an appropriate amount of process gas is introduced. This gas undergoes a series of chemical and plasma reactions, ultimately resulting in the formation of a solid film on the sample's surface.
The key to the PECVD process lies in the plasma's ability to ionize and decompose molecules within the reaction gas. This ionization provides the necessary energy to dissociate the precursor gas, facilitating the formation of the deposit. The plasma is typically generated through a discharge mechanism, such as RF (Radio Frequency), DC (Direct Current), or pulsed DC, which ionizes the plasma gas species present in the chamber. This ionization process is crucial as it not only lowers the temperature required for film deposition but also enhances the efficiency of the chemical reactions involved.
In contrast to other CVD techniques, PECVD's use of plasma significantly alters the reaction dynamics. While traditional CVD methods rely on thermal energy to drive chemical reactions, PECVD leverages the energetic particles within the plasma to initiate and sustain these reactions. This not only allows for lower operational temperatures but also broadens the range of materials that can be deposited, making PECVD particularly suitable for temperature-sensitive substrates.
The process is illustrated in Figure 1, which provides a visual representation of how the plasma interacts with the process gas to form the desired film. This figure highlights the essential components of the PECVD system, including the electrodes, plasma generator, and the reaction chamber, each playing a critical role in the successful deposition of the film.
Features of PECVD
PECVD operates at relatively low temperatures, typically ranging from 200°C to 400°C, making it highly suitable for temperature-sensitive materials. The process is conducted under a controlled air pressure range, usually between a few hundred milliTorr (mTorr) to a few Torr, which contributes to its efficiency and versatility.
Film Quality and Uniformity
While PECVD films exhibit good uniformity, their density and overall quality are generally inferior to those produced by LPCVD. This is primarily due to the potential for defects, such as pinholes or inhomogeneities, introduced by the plasma during the deposition process. Despite these limitations, PECVD films are highly cross-linked and resistant to chemical and thermal changes, making them suitable for various applications.
Deposition Rate and Efficiency
One of the significant advantages of PECVD is its high deposition rate, which translates to higher productivity. This efficiency is attributed to the uneven electric field distribution in front of the cathode, where the highest electric field intensity occurs in the cathode drop zone. This region is the concentration domain for chemical reactions, leading to a faster deposition rate and reduced loss of reactants on the chamber walls.
Controllable Parameters
Compared to conventional thermal chemical vapor deposition, PECVD offers a broader range of controllable parameters. These include not only air pressure and temperature but also discharge methods, discharge voltage, current density, and ventilation methods. By optimizing these parameters, it is possible to achieve more excellent compound thin-film materials with specific properties such as stress, refractive index, and hardness.
Typical Applications
PECVD is widely used in the deposition of various materials, including organics, silicon nitride (Si₃N₄), and silicon oxide (SiO₂). Its low-temperature capabilities make it ideal for applications in photovoltaic devices, solar cells, and the microelectronics industry. Additionally, the low cost and high efficiency of plasma-applied polymers have expanded its use in optical coatings and dielectric films.
Advantages and Disadvantages of PECVD
Advantages
PECVD offers several compelling advantages, particularly in environments where temperature sensitivity is a critical factor. The primary benefit lies in its ability to deposit thin films at significantly lower temperatures compared to other CVD methods, typically ranging from room temperature to 350°C. This low-temperature deposition capability is particularly advantageous for temperature-sensitive materials, such as plastics, which would otherwise degrade under higher heat conditions.
Moreover, PECVD boasts high productivity due to its fast deposition rates, which enhance production efficiency and overall productivity. This rapid deposition process is facilitated by the use of plasma, which energizes gas molecules to a highly reactive state, enabling chemical reactions to occur at lower temperatures. This not only speeds up the process but also allows for in-situ doping, simplifying the overall process flow.
Another noteworthy advantage is PECVD's cost-effectiveness. Compared to LPCVD, PECVD can reduce both material and operating costs in certain applications. This is partly due to the lower energy requirements and the ability to use less expensive precursors, making it a more economical choice for many industries.
Disadvantages
Despite its numerous advantages, PECVD is not without its drawbacks. One of the significant challenges associated with PECVD is the potential for film defects, such as pinholes or inhomogeneities, which can be introduced by the plasma. These defects can compromise the overall quality and integrity of the deposited film, leading to issues in performance and reliability.
Additionally, PECVD films may suffer from stability issues, such as film bursting, which can further affect the durability and longevity of the deposited layers. The equipment used in PECVD is also relatively complex, requiring high maintenance and frequent debugging to ensure optimal performance. This complexity adds to the operational costs and can be a barrier for smaller or less technically equipped facilities.
Another disadvantage is the potential for film quality fluctuations due to plasma instability. While PECVD offers good film uniformity, the quality and density of the films are generally inferior to those produced by LPCVD. This can be a limiting factor in applications where high film density and quality are paramount, such as in the production of advanced microelectronic components.
In summary, while PECVD provides a versatile and efficient method for thin film deposition, particularly for temperature-sensitive materials, it is essential to weigh these benefits against the potential drawbacks in order to make an informed decision based on specific application requirements.
ICPCVD (Inductively Coupled Plasma Chemical Vapor Deposition)
Principle of ICPCVD
ICPCVD represents an advanced variant of PECVD technology, distinguished by its ability to generate a high-density plasma through an inductively coupled coil. This method significantly enhances the plasma density and ensures a more uniform energy distribution compared to conventional PECVD processes. The elevated plasma density in ICPCVD facilitates the deposition of high-quality films at notably lower pressures and temperatures.
In ICPCVD, the inductively coupled coil plays a crucial role in creating a robust plasma environment. This coil, typically positioned around the reaction chamber, induces a strong electromagnetic field that ionizes the reaction gases. The resulting high-density plasma not only accelerates the chemical reactions necessary for film formation but also distributes energy uniformly across the substrate surface. This uniformity is paramount for achieving consistent film properties, such as thickness, density, and adherence, across the entire substrate.
The operational parameters of ICPCVD, such as pressure and temperature, are optimized to leverage the benefits of high-density plasma. The process is conducted at pressures significantly lower than those used in traditional PECVD, often ranging between 1 and 100 mTorr. This low-pressure environment minimizes the occurrence of gas-phase reactions, thereby reducing the likelihood of defects and improving film quality. Additionally, the process temperature is kept very low, typically within the range of room temperature to 300°C, making ICPCVD highly suitable for heat-sensitive materials.
The combination of high plasma density and uniform energy distribution in ICPCVD yields several advantages over other CVD techniques. Firstly, it enables the deposition of films with superior quality and uniformity, which are essential for applications demanding high precision and reliability. Secondly, the lower operating temperatures and pressures reduce the thermal and mechanical stresses on the substrate, preserving its structural integrity and performance.
In summary, ICPCVD stands out as a sophisticated CVD technology that leverages high-density plasma and uniform energy distribution to deposit high-quality films at lower pressures and temperatures. This capability makes it an invaluable tool for applications requiring exceptional film properties, such as in optoelectronic devices and materials with low dielectric constants.
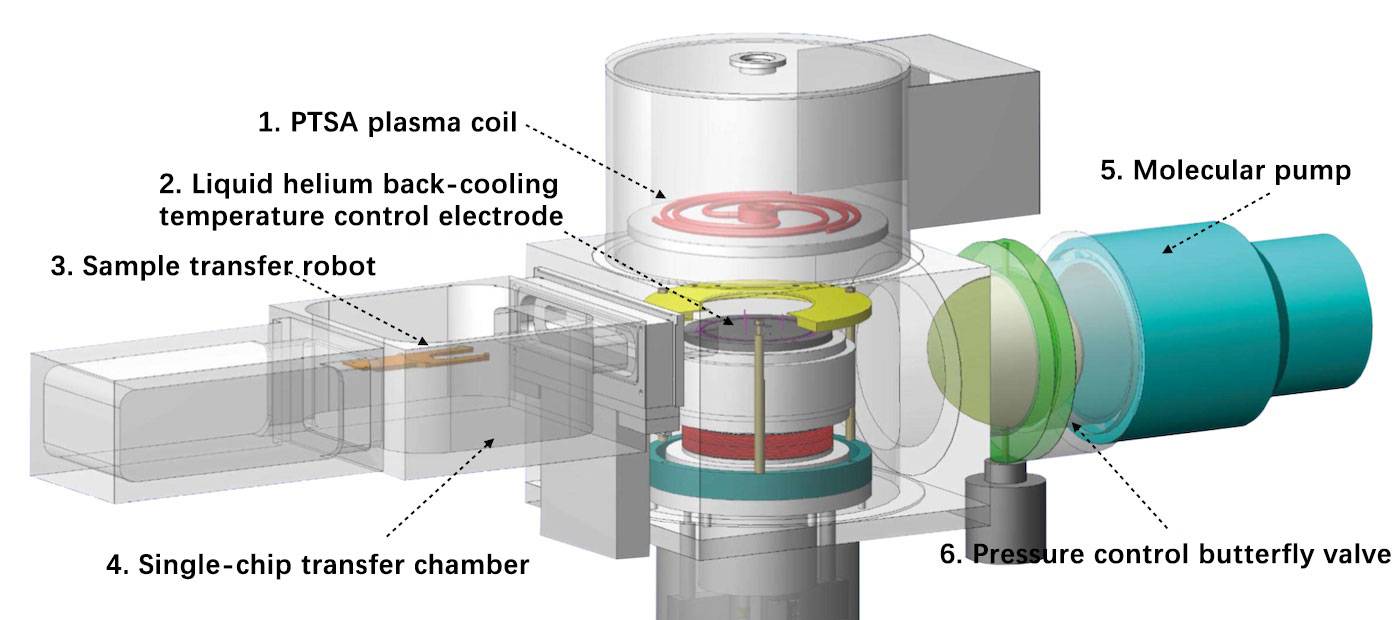
1. PTSA plasma coil 2. Liquid helium back-cooling temperature control electrode 3. Sample transfer robot 4. Single-chip transfer chamber 5. Molecular pump 6. Pressure control butterfly valve
Features of ICPCVD
The Inductively Coupled Plasma Chemical Vapor Deposition (ICPCVD) process operates at remarkably low temperatures, generally ranging from room temperature to 300°C. This low-temperature process characteristic makes it ideal for processing temperature-sensitive materials, enabling the deposition of high-quality films without damaging the substrate.
In terms of air pressure range, ICPCVD typically operates between 1 and 100 mTorr, which is lower than PECVD. This low-pressure environment helps maintain a high density of plasma, which improves film quality and uniformity.
Film quality is a major benefit of ICPCVD, which deposits films of higher quality and uniformity due to the high density plasma. This high quality film is ideal for use on complex shaped surfaces and ensures uniform distribution of the film on a variety of substrates.
In terms of deposition rate, ICPCVD falls between and slightly above LPCVD and PECVD, and although the deposition rate is not the fastest, the quality of the films deposited makes up for it.
Typical applications for ICPCVD include the deposition of demanding films in optoelectronic devices, such as anti-reflective films, and the deposition of materials with low dielectric constants. These applications demonstrate the importance of ICPCVD in advanced materials science and the microelectronics industry.
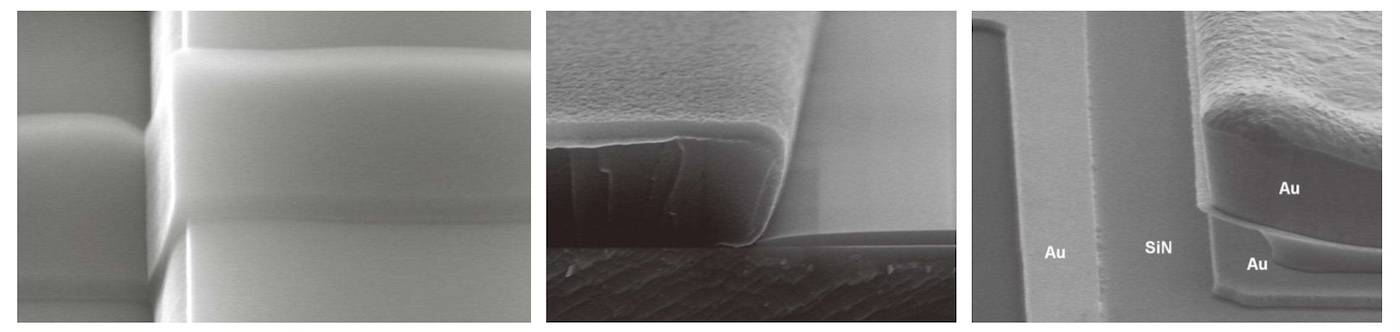
Advantages and Disadvantages of ICPCVD
Advantages:
-
Low-Temperature Deposition: One of the standout features of ICPCVD is its ability to deposit high-quality films at extremely low temperatures, typically ranging from room temperature to 300°C. This makes it an ideal choice for heat-sensitive materials, which would otherwise degrade or lose functionality at higher temperatures.
-
Superior Film Quality: The process yields films with excellent uniformity, density, and surface smoothness. This is largely due to the high plasma density generated by the inductively coupled coil, which ensures a more controlled and uniform deposition process.
-
Enhanced Deposition Uniformity: The high plasma density not only improves the uniformity of the deposited films but also enhances their overall properties. This makes ICPCVD particularly suitable for coating complex-shaped surfaces and non-uniform substrates, overcoming some of the limitations faced by other CVD methods.
Disadvantages:
-
Complicated Equipment and Higher Cost: The sophisticated nature of ICPCVD equipment, which includes the inductively coupled plasma system, makes it more complex and expensive to set up and maintain compared to other CVD techniques.
-
Slower Deposition Rate: While ICPCVD offers many advantages, it is not without its drawbacks. One of the significant limitations is its slower deposition rate, which can impact the overall efficiency of the process, especially in high-volume production environments.
-
Potential for Plasma-Induced Damage: The higher plasma energy used in ICPCVD, while beneficial for achieving high-quality films, can sometimes introduce a small amount of damage to the deposited materials. This is a trade-off that must be carefully managed to ensure the integrity of the final product.
CONTACT US FOR A FREE CONSULTATION
KINTEK LAB SOLUTION's products and services have been recognized by customers around the world. Our staff will be happy to assist with any inquiry you might have. Contact us for a free consultation and talk to a product specialist to find the most suitable solution for your application needs!