Introduction to Electrolytic Cells and Corrosion
Electrolytic cells play a pivotal role in various industrial processes, yet they are not without challenges, particularly in terms of corrosion. This article delves into the intricate workings of flat corrosion electrolytic cells, exploring their fundamental components such as the electrolyte, anode, and cathode, and the processes that lead to corrosion. Understanding these mechanisms is crucial for developing effective strategies to mitigate corrosion, ensuring the longevity and efficiency of electrolytic cells in applications ranging from metal purification to electroplating. Join us as we unravel the complexities of electrolytic cells and the critical measures needed to safeguard these essential industrial tools.
Mechanisms of Corrosion in Electrolytic Cells
Corrosion in electrolytic cells is a complex process that involves the interaction of various factors, including fluctuating potentials and the dissimilarity between metal electrodes. Understanding these mechanisms is crucial for developing effective strategies to mitigate corrosion, which can significantly impact the efficiency and lifespan of electrolytic cells.
Role of Fluctuating Potentials
Fluctuating potentials in electrolytic cells can arise from several sources, including variations in the applied voltage, changes in the electrolyte composition, and thermal fluctuations. These fluctuations can lead to localized corrosion, where certain areas of the electrode experience higher rates of oxidation or reduction than others. This non-uniform corrosion can result in pitting, crevice corrosion, and other forms of localized damage.
For instance, in a typical electrolytic cell, the anode undergoes oxidation, releasing electrons, while the cathode undergoes reduction, accepting electrons. If the potential at the anode fluctuates, it can lead to uneven oxidation rates, causing some areas to corrode more rapidly than others. Similarly, potential fluctuations at the cathode can affect the reduction process, leading to non-uniform corrosion patterns.
Interaction Between Different Metal Electrodes
The use of dissimilar metal electrodes in an electrolytic cell can also contribute to corrosion. When two different metals are in contact with each other in an electrolyte solution, they can form a galvanic cell, where one metal acts as the anode and the other as the cathode. The metal with a higher oxidation potential will corrode more rapidly, acting as the sacrificial anode.
For example, if a copper electrode is used with a zinc electrode in an acidic electrolyte, zinc will corrode more quickly due to its higher oxidation potential. This galvanic corrosion can be exacerbated by fluctuations in the electrolyte's pH, temperature, and ionic concentration, leading to accelerated degradation of the sacrificial anode.
Mitigation Strategies
To mitigate corrosion in electrolytic cells, several strategies can be employed:
-
Cathodic Protection: This involves using a more reactive metal as a sacrificial anode to protect the primary electrode from corrosion. The sacrificial anode corrodes instead of the primary electrode, thereby extending its lifespan.
-
Inhibitors: Chemical inhibitors can be added to the electrolyte to reduce the corrosion rate. These inhibitors form a protective layer on the electrode surface, preventing direct contact with corrosive species. Common inhibitors include organic compounds containing nitrogen, sulfur, or oxygen atoms.
-
Material Selection: Choosing corrosion-resistant materials for the electrodes can significantly reduce corrosion rates. For instance, platinum and gold are highly resistant to corrosion and are often used in demanding electrolytic applications.
-
Electrode Design: Optimizing the design of the electrodes can also help reduce corrosion. For example, using bipolar electrodes, which act as both anode and cathode in different cells, can minimize the potential difference between the electrodes and reduce galvanic corrosion.
-
Maintenance and Monitoring: Regular monitoring of the electrolytic cell's performance can help identify early signs of corrosion. Periodic maintenance, such as cleaning the electrodes and replacing the electrolyte, can prevent the buildup of corrosive byproducts and ensure optimal performance.
Conclusion
Corrosion in electrolytic cells is a multifaceted issue that involves the interplay of fluctuating potentials and the interaction between different metal electrodes. By understanding these mechanisms, it is possible to develop effective strategies to mitigate corrosion, thereby enhancing the efficiency and longevity of electrolytic cells. Through careful material selection, design optimization, and the use of protective measures such as inhibitors and cathodic protection, it is possible to significantly reduce the impact of corrosion on electrolytic systems.
Industrial Applications of Electrolytic Cells
Electrolytic cells play a crucial role in various industrial processes, from metal purification to chemical production. These cells utilize the principles of electrolysis, where an electric current is passed through a liquid or solution containing ions to drive non-spontaneous chemical reactions. This section delves into the specific industrial applications of electrolytic cells, focusing on copper purification, electroplating, and the production of caustic soda, while also highlighting the importance of preventing corrosion.
Copper Purification
One of the most significant applications of electrolytic cells is in the purification of copper. The process involves the use of an electrolytic cell where the anode is made of impure copper and the cathode is a thin sheet of pure copper. The electrolyte is a solution of copper sulfate (CuSO4) and sulfuric acid (H2SO4). When an electric current is applied, copper ions (Cu2+) from the anode dissolve into the electrolyte and then migrate to the cathode, where they are deposited as pure copper. This process results in copper purity levels exceeding 99.9%.
The energy consumption for copper refining by electrolytic processes ranges from 150 to 300 kilowatt-hours per tonne of refined copper. This method is highly efficient and ensures that impurities such as iron and zinc remain in the electrolyte, while valuable metals like gold and silver collect at the bottom of the cell as anode sludge, which can be recovered.
Electroplating
Electroplating is another critical application of electrolytic cells, where a thin layer of a metal is deposited onto the surface of another metal to enhance its appearance, durability, or provide corrosion resistance. Common metals used in electroplating include chromium, nickel, and gold. The process involves immersing the object to be plated (cathode) and a bar of the plating metal (anode) in an electrolyte solution containing the metal ions. When an electric current is applied, metal ions from the electrolyte are reduced at the cathode, forming a uniform coating.
Electroplating is widely used in the automotive, aerospace, and electronics industries. For example, chromium plating is used to provide a hard, shiny finish to automotive parts, while gold plating is essential for electronic components to ensure good electrical conductivity and resistance to corrosion.
Production of Caustic Soda
The production of caustic soda (sodium hydroxide, NaOH) is another significant industrial application of electrolytic cells. Caustic soda is a crucial chemical in various industries, including paper manufacturing, soap and detergent production, and water treatment. The process involves the electrolysis of a sodium chloride (NaCl) solution, commonly known as brine.
In the electrolytic cell, chlorine gas (Cl2) is produced at the anode, and sodium hydroxide is produced at the cathode. The overall reaction can be summarized as:
[ 2NaCl + 2H2O \rightarrow 2NaOH + Cl2 + H2 ]
The chlorine gas is often used in the production of other chemicals, such as PVC (polyvinyl chloride), while the caustic soda is used in numerous industrial processes. This method of production is highly efficient and is carried out on a large scale, with millions of tonnes of caustic soda produced annually worldwide.
Preventing Corrosion
Preventing corrosion is a critical aspect of many industrial applications involving electrolytic cells. Corrosion occurs when a metal reacts with its environment, leading to degradation and loss of material properties. Electrolytic cells can be used to apply protective coatings to metals, such as zinc or cadmium, which provide a barrier against environmental factors.
In addition, electrolytic cells are used in the process of cathodic protection, where a sacrificial anode is connected to the metal structure to be protected. The sacrificial anode corrodes instead of the protected structure, thereby extending its lifespan. This method is commonly used in the protection of pipelines, offshore structures, and storage tanks.
In conclusion, electrolytic cells are indispensable in various industrial processes, from metal purification and electroplating to chemical production and corrosion prevention. These applications highlight the versatility and importance of electrolytic cells in modern industry, ensuring the production of high-quality materials and the efficient operation of industrial processes.
Preventive Measures Against Corrosion
Corrosion in electrolytic cells is a significant concern due to its potential to degrade the performance and lifespan of the equipment. Various techniques have been developed to prevent or mitigate corrosion, including the use of inhibitors, cathodic protection, and the formation of passivation layers. These methods are crucial for maintaining the integrity and efficiency of electrolytic processes, which are widely used in industries such as electroplating, metal refining, and water treatment.
Use of Inhibitors
Inhibitors are chemicals that, when added to the electrolyte, can significantly reduce the corrosion rate of the electrodes. These substances work by forming a protective layer on the surface of the metal, which acts as a barrier against the corrosive environment. The effectiveness of inhibitors depends on several factors, including their concentration, the type of metal, and the composition of the electrolyte. For instance, certain organic compounds containing nitrogen, sulfur, or oxygen atoms can be highly effective as inhibitors due to their ability to adsorb onto the metal surface and block the active sites where corrosion typically occurs.
Cathodic Protection
Cathodic protection is another effective method for preventing corrosion in electrolytic cells. This technique involves making the metal surface the cathode of an electrochemical cell, thereby protecting it from oxidation. There are two main types of cathodic protection: sacrificial anodes and impressed current. In sacrificial anode systems, a more reactive metal (such as zinc or magnesium) is connected to the metal to be protected. The sacrificial anode corrodes instead of the protected metal. In impressed current systems, an external power source is used to supply a continuous current to the cathode, which prevents it from undergoing oxidation.
Formation of Passivation Layers
The formation of passivation layers is a natural process where a thin, protective layer of oxide or other compounds forms on the surface of the metal. This layer acts as a barrier that prevents further corrosion by blocking access to the underlying metal. Passivation can be enhanced through the use of specific treatments, such as anodizing for aluminum or chromating for steel. These treatments not only create a protective layer but also improve the mechanical properties of the metal, making it more resistant to wear and tear.
Electroplating
Electroplating is a process where a thin layer of metal is deposited onto another metal surface to provide protection against corrosion. This process involves immersing the metal part in a solution containing the metal to be deposited and applying an electric current. The metal ions in the solution are reduced at the cathode (the metal part), forming a protective coating. Common metals used for electroplating include chromium, nickel, and zinc. Electroplating not only provides corrosion protection but also enhances the appearance and wear resistance of the metal parts.
Electrolytic Cells in Industry
Electrolytic cells are extensively used in various industrial processes, including the production of high-purity metals such as aluminum, copper, zinc, and lead. These cells are also used in the electrorefining and electrowinning of metals, where the purity of the final product is critical. In addition, electrolytic cells are employed in water treatment processes, such as the decomposition of water into hydrogen and oxygen. The prevention of corrosion in these cells is essential to ensure the continuous and efficient operation of these processes.
Conclusion
Preventing corrosion in electrolytic cells is crucial for the longevity and performance of industrial equipment. Techniques such as the use of inhibitors, cathodic protection, and the formation of passivation layers are effective strategies for mitigating corrosion. These methods not only protect the electrodes but also ensure the efficient operation of electrolytic processes, which are vital for various industrial applications. By implementing these preventive measures, industries can reduce maintenance costs, extend the lifespan of their equipment, and maintain high-quality production standards.
Design and Materials of Electrolytic Cells
Electrolytic cells are fundamental in various industrial processes, particularly in the electrorefining and electrowinning of non-ferrous metals such as aluminum, copper, zinc, and lead. These cells are designed to facilitate the decomposition of chemical compounds through the application of electrical energy, a process that would not occur spontaneously under normal conditions. The efficiency and effectiveness of an electrolytic cell heavily depend on its design and the materials used, especially the selection of inert electrodes and the nature of the electrolyte.
Components of Electrolytic Cells
An electrolytic cell consists of three primary components: the electrolyte, the cathode, and the anode.
-
Electrolyte: This is typically a solution of water or other solvents in which ions are dissolved. Molten salts, such as sodium chloride, can also serve as electrolytes. The role of the electrolyte is crucial as it contains the ions that participate in the redox reactions when an external voltage is applied. The ions in the electrolyte move towards the electrodes of opposite charge, facilitating the charge-transferring reactions.
-
Cathode and Anode: The cathode is the negative electrode where reduction occurs, while the anode is the positive electrode where oxidation takes place. In electrolytic cells, inert electrodes are preferred to avoid any chemical reactions that might alter the electrodes themselves. Common materials for these electrodes include graphite and platinum, which are known for their stability and conductivity.
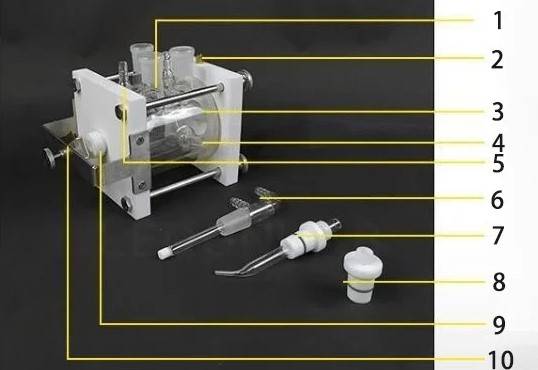
Design Considerations
The design of an electrolytic cell must consider several factors to optimize its performance:
-
Electrode Material Selection: The choice of electrode material is critical. Anodes should be efficient reducing agents with high coulombic output, good conductivity, stability, ease of fabrication, and low cost. Common anode materials include zinc and lithium. Cathodes, on the other hand, should be efficient oxidizing agents, stable in contact with the electrolyte, and have a useful working voltage. Metallic oxides are often used for this purpose.
-
Electrolyte Composition: The electrolyte must be carefully chosen to ensure that it supports the desired chemical reactions without causing unwanted side effects such as corrosion or degradation of the electrodes. The conductivity of the electrolyte is also a key factor, as it directly influences the efficiency of the cell.
-
Cell Geometry: The physical arrangement of the electrodes and the electrolyte can significantly affect the flow of ions and the distribution of current within the cell. Optimizing the cell geometry can help minimize energy losses and improve the overall efficiency of the electrolytic process.
Applications and Impact
The design and materials of electrolytic cells have a profound impact on their applications in industry. For instance, the production of high-purity metals like aluminum and copper relies heavily on the efficiency of these cells. Additionally, electrolytic cells are used in processes such as water purification and the generation of hydrogen gas, demonstrating their versatility and importance in modern technology.
In conclusion, the design and materials of electrolytic cells are critical to their function and efficiency. By carefully selecting inert electrodes and optimizing the electrolyte and cell geometry, it is possible to enhance the performance of these cells, making them more effective in a wide range of industrial applications.
Electrolytic vs. Galvanic Cells
Electrolytic and galvanic cells are fundamental components in the field of electrochemistry, each serving distinct purposes and operating under different principles. Understanding the differences and applications of these cells is crucial for various scientific and industrial processes.
Operational Differences
Electrolytic Cells: Electrolytic cells are used to drive non-spontaneous chemical reactions through the application of electrical energy. They consist of two electrodes (anode and cathode) immersed in an electrolyte solution. In these cells, the external power source forces electrons into the cathode, making it negative, and draws electrons from the anode, making it positive. This setup reverses the natural flow of electrons, enabling the occurrence of non-spontaneous reactions.
Galvanic Cells: In contrast, galvanic cells generate electrical energy from spontaneous chemical reactions. They also consist of two electrodes immersed in an electrolyte, but unlike electrolytic cells, they do not require an external power source. The anode, where oxidation occurs, is negatively charged, and the cathode, where reduction occurs, is positively charged. The flow of electrons from the anode to the cathode through an external circuit generates an electric current.
Applications
Electrolytic Cells: Electrolytic cells are extensively used in industrial processes such as electrolysis of water to produce hydrogen and oxygen, electroplating metals, and refining copper. They are also crucial in the production of chemicals like caustic soda and chlorine. The ability to drive non-spontaneous reactions makes them indispensable in various chemical synthesis and purification processes.
Galvanic Cells: Galvanic cells are the basis of batteries, where the energy from spontaneous redox reactions is harnessed to provide electrical power. Common examples include primary cells like alkaline and zinc-carbon batteries, and secondary cells like lead-acid and lithium-ion batteries. These cells are vital in powering portable electronic devices, vehicles, and backup power systems.
Impact on Corrosion Rates and Prevention Strategies
The operational differences between electrolytic and galvanic cells significantly affect corrosion rates and prevention strategies. In galvanic corrosion, two dissimilar metals in contact with each other and an electrolyte form a galvanic cell, leading to accelerated corrosion of the less noble metal. This phenomenon is exploited in sacrificial anode systems used to protect structures like ships and pipelines from corrosion.
Electrolytic cells, on the other hand, can be used in cathodic protection methods, where a metal structure is connected to a more reactive metal (sacrificial anode) and immersed in an electrolyte. The more reactive metal corrodes instead of the protected structure, effectively preventing corrosion.
Conclusion
In summary, while both electrolytic and galvanic cells involve redox reactions and have electrodes where oxidation and reduction occur, they function in opposite ways. Electrolytic cells use external electrical energy to drive non-spontaneous reactions, while galvanic cells generate electrical energy from spontaneous reactions. Understanding these differences is essential for effective application in various scientific, industrial, and engineering contexts, particularly in managing corrosion and its prevention.
Future Trends and Innovations in Electrolytic Cell Technology
The field of electrolytic cell technology is poised for significant advancements, driven by the need for more durable and efficient systems, particularly in the context of battery development and metal refining processes. These innovations aim to address critical challenges such as corrosion, energy efficiency, and the scalability of electrolytic processes.
Enhancing Durability through Material Science
Corrosion remains a significant issue in electrolytic cells, particularly in environments with fluctuating potentials and dissimilar metals. Researchers are exploring various methods to mitigate corrosion, including the use of inhibitors and the development of new materials that are inherently more resistant to corrosion. Cathodic inhibition, for instance, is a technique that forms a protective layer on the cathode, reducing the rate of corrosion. This method not only slows down the cathodic reaction but also precipitates in these areas, thereby protecting the electrode from further damage.
Innovations in Electrolytic Cell Design
The design of electrolytic cells is also undergoing significant changes. Traditional designs rely on a complete circuit with stable electrodes and a fluid electrolyte solution. However, emerging designs are exploring the use of solid electrolytes that can operate under extreme temperatures, offering stability and enhanced performance. These solid electrolytes could enable batteries with high energy densities to have much longer lifetimes, making them suitable for a wide range of applications from electric vehicles to grid storage.
Energy Efficiency and Sustainability
Improving the energy efficiency of electrolytic cells is another critical focus area. This involves optimizing the electrical and chemical processes within the cell to reduce energy losses and enhance overall performance. Researchers are also looking into more sustainable materials and processes, reducing the environmental impact of electrolytic cells. For instance, the development of bio-based electrolytes and the recycling of materials used in electrolytic cells are gaining traction as sustainable alternatives.
Conclusion
The future of electrolytic cell technology is bright, with numerous innovations on the horizon that promise to enhance durability, efficiency, and sustainability. Advancements in electrolyte development, material science, cell design, and energy efficiency are paving the way for more robust and versatile electrolytic cells. These developments not only address the technical challenges but also contribute to broader environmental goals by promoting cleaner and more sustainable energy solutions. As research continues to evolve, the impact of these innovations will be felt across various industries, from energy storage to metal refining, driving progress towards a more sustainable future.
CONTACT US FOR A FREE CONSULTATION
KINTEK LAB SOLUTION's products and services have been recognized by customers around the world. Our staff will be happy to assist with any inquiry you might have. Contact us for a free consultation and talk to a product specialist to find the most suitable solution for your application needs!