Description and Applications of Warm Isostatic Press
Table of Contents
Explanation of Warm Isostatic Press (WIP)
Warm Isostatic Press (WIP) equipment, also known as Warm Isostatic Laminator, is a cutting-edge technology that combines isostatic pressing with a heating element. It utilizes warm water or a similar medium to apply uniform pressure to powdered products from all directions. The process involves shaping and pressing the powder material using flexible materials as a jacket mold and hydraulic pressure as a pressure medium.
WIP systems can be gas or liquid pressurized and are often used for plastics and laminated products. These systems can be custom-built to meet specific requirements and can operate at various temperatures and pressures. Liquid WIP systems can reach temperatures up to 250°C, while gas WIP systems can go up to 500°C. Both cold and hot wall versions are available.
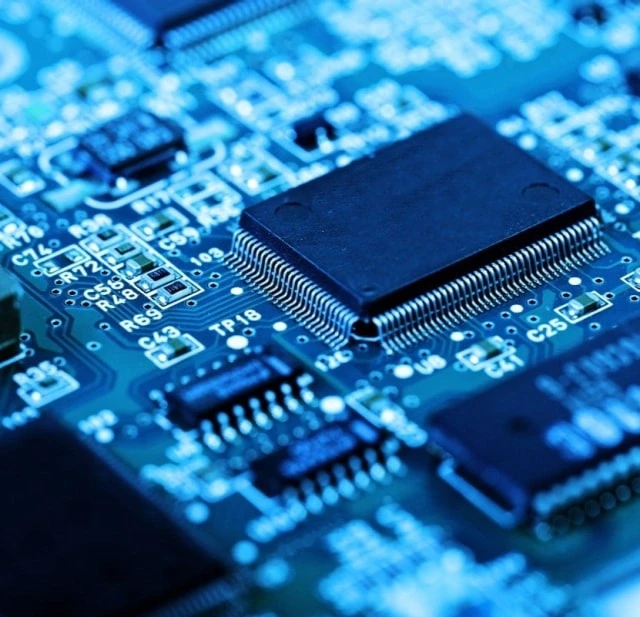
Use of WIP in the production of high-quality monolithic multilayer ceramic electronic components
One of the primary applications of Warm Isostatic Press is in the production of high-quality monolithic multilayer ceramic electronic components. These components include MLCC, MLCI, LTCC, HTCC, MCM, Piezoelectric, Filter, Varistor, Thermistor, and more.
Warm Isostatic Laminators are best suited for compressing green sheets to produce these electronic components. Compared to conventional uniaxial press methods, WIP delivers compressed bodies of higher quality. As a result, WIP has become the de facto standard system for manufacturing these components.
The process involves heating the liquid medium, such as water or oil thermal fluid, and continuously injecting it into a sealed pressing cylinder through a booster source. The pressing cylinder is equipped with a heating element to ensure accurate temperature control. The warm isostatic pressing process allows for isostatic pressing at a temperature that does not exceed the boiling point of the liquid medium.
In conclusion, Warm Isostatic Press (WIP) is a versatile technology with applications in various industries. Its ability to provide uniform pressure from all directions makes it ideal for producing high-quality monolithic multilayer ceramic electronic components. Whether for plastics, laminated products, or electronic components, WIP offers a cost-effective and efficient solution for achieving optimal results.
Comparative Analysis between WIP and Conventional Uniaxial Press Method
Superiority of WIP in delivering higher quality compressed bodies
A minimum of three cassettes (each cassette typically consisting of the mandrel, mold, and powder) are in motion simultaneously; one is pressed, one is filled with powder, and one is de-bagged. The cycle time is 1 min or less, which calculates to 120,000 cycles/year on a 1-shift, 8-h basis. This rate of cycling places a much higher demand on the pressure vessel fatigue, and proper design is critical to withstand the higher pressures. The dry-bag method is preferred over the wet-bag for automated production of same-size or same-shape parts in lots of about 50 parts per hour or above.
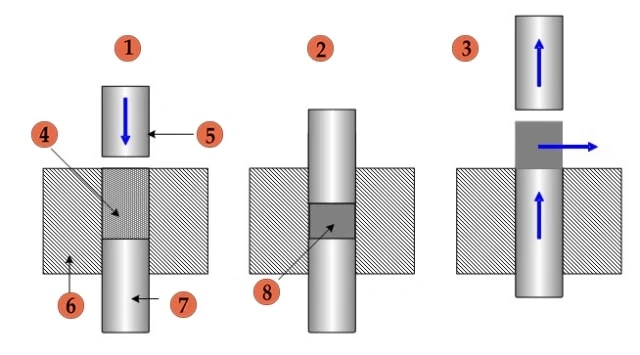
Warm Isostatic Pressing (WIP) follows the same path as CIP except the parts are compacted both at pressure and low temperature to 100°C. The pressing fluid water may be substituted with oil. To date, there are a few applications for manufacturers in the electronics industry as a cost-effective means of compacting different shaped parts.
WIP units are designed for other applications requiring artificial pressure. They offer custom modes when special functions are required. WIP systems for production use water or oil thermal fluid and are heated using external circulation heaters. They feature a touch screen with computer-based graphical operation and have a standard interface.
The advantages of Warm Isostatic Pressing (WIP) include:
- More uniform product properties, greater homogeneity, and more precise control of the finished product dimensions.
- Greater flexibility in the shape and size of the finished product.
- Longer aspect ratios possible, allowing for the production of long thin pellets.
- Improved compaction of the powder, leading to improved densification.
- Ability to process materials with different characteristics and shapes.
- Reduced cycle times and improved productivity.
Widespread use of WIP as the de facto standard system in electronics manufacturing
Warm Isostatic Laminators, also known as Warm Isostatic Press (WIP), are best suited for compressing Green sheets to produce high-quality monolithic multilayer ceramic electronic components. These laminators deliver compressed bodies of higher quality than those manufactured by the conventional uniaxial press method. As a result, WIP has become the de facto standard system widely used in electronics manufacturing.
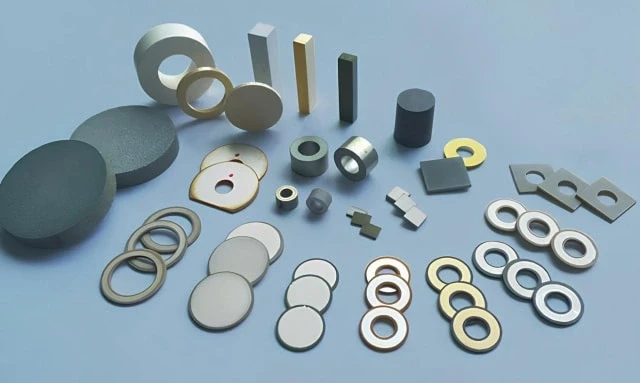
Both uniaxial pressing and Cold Isostatic Pressing (CIP) are methods for compacting powder samples. Uniaxial pressing applies force along one axis and is used for pressing simple shapes with fixed dimensions. It requires a mold and a hydraulic press and is relatively inexpensive. However, it has limitations such as short aspect ratio requirements and the ability to produce only simple shapes.
On the other hand, CIP is slower but can be used for small or large, simple or complex shapes. It offers more uniform green density, which leads to more even shrinkage during sintering and better shape control and uniform properties. CIP also eliminates the need for a wax binder, unlike uniaxial pressing.
In terms of isostatic pressing methods, low-cost elastomer tooling is used for iso-static pressing, but close tolerances can only be obtained for surfaces that are pressed against a highly accurate steel mandrel. Surfaces in contact with the elastomer tooling may require post-machining when tight tolerances and good surface finishes are specified.
Overall, Warm Isostatic Pressing (WIP) stands out in delivering higher quality compressed bodies and has become the preferred system in electronics manufacturing due to its effectiveness and cost-efficiency.
CONTACT US FOR A FREE CONSULTATION
KINTEK LAB SOLUTION's products and services have been recognized by customers around the world. Our staff will be happy to assist with any inquiry you might have. Contact us for a free consultation and talk to a product specialist to find the most suitable solution for your application needs!