Sample Preparation Requirements
General Requirements
Samples undergoing X-ray fluorescence (XRF) spectrometry analysis must first undergo a meticulous sample preparation process. This process is essential to ensure that the sample accurately represents the overall composition of the material and can be effectively analyzed by the instrument. The prepared sample should meet several critical criteria:
- Size and Thickness: The sample should be of a specific size and thickness to fit within the sample box designated for the XRF instrument. This ensures optimal alignment and coverage of the X-ray beam.
- Flat Surface: A flat surface is crucial for uniform X-ray penetration and accurate measurement. Irregular surfaces can lead to inconsistencies in the data collected.
- Reproducibility: The sample preparation process must be highly reproducible to ensure consistent results across different analyses. Variability in preparation can introduce errors in the data.
To illustrate these requirements, consider the following table:
Requirement | Description |
---|---|
Size and Thickness | Sample must fit within the sample box and have a specific thickness for optimal X-ray coverage. |
Flat Surface | A smooth, flat surface ensures uniform X-ray penetration and accurate measurements. |
Reproducibility | The preparation process must yield consistent results to maintain data accuracy. |
By adhering to these general requirements, the prepared sample can be reliably analyzed using XRF spectrometry, providing accurate and reproducible data.
Specific Requirements
The sample volume for XRF analysis is typically substantial, making it more representative compared to other analytical techniques. This larger volume ensures a comprehensive analysis by capturing a broader range of elements and compounds present in the sample. The sample should possess a specific size and thickness, with the thickness ideally reaching what is referred to as 'infinite thickness'. This term signifies that the sample's thickness is sufficient to absorb all incident X-rays, thereby preventing any interference from the underlying material.
A flat surface is crucial for accurate XRF analysis. A smooth, flat surface minimizes the 'particle effect', which can lead to variations in the intensity of the X-rays detected. By reducing this effect, the reproducibility of the analysis is significantly improved, ensuring consistent and reliable results across multiple tests. This attention to detail in sample preparation is essential for obtaining precise and accurate data, which is fundamental to the integrity of the analysis.
Preparation Methods for Powder Samples
Direct Measurement
When employing the direct measurement method in X-ray fluorescence (XRF) spectrometry, the powder sample is meticulously placed within a liquid cup. This approach offers several distinct advantages, chief among them being the elimination of the need for extensive sample preparation. Consequently, this method is particularly convenient for quick analyses where time is of the essence. Additionally, the ability to recover the sample post-analysis is a significant benefit, allowing for further examination or reuse of the material.
However, this method is not without its limitations. One of the primary drawbacks is that the results obtained are semi-quantitative, meaning they provide a general idea of the elemental composition but lack the precision required for definitive conclusions. Furthermore, the scope of element analysis is restricted, as not all elements can be accurately measured using this technique. These limitations necessitate careful consideration when selecting the appropriate sample preparation method for specific analytical needs.
Tableting Preparation
For tableting, ensuring the sample fineness is crucial. Generally, the powder should pass through a 200 mesh sieve, which helps in achieving a homogeneous mixture and a smooth surface on the tablet. The powder samples must be thoroughly dried to prevent any moisture-induced inconsistencies or defects in the final product.
The prepared tablets should exhibit several key characteristics. They should be firm, which ensures that the tablet remains intact during handling and analysis. Additionally, the surface of the tablets should be free from cracks or delamination. These defects can lead to inconsistencies in the XRF analysis results, as they can affect the uniformity of the sample's surface and the intensity of the X-ray fluorescence.
To achieve these standards, careful attention must be paid to the tableting process. This includes using appropriate binders and grinding aids, which are discussed in detail in the subsequent sections. The choice of tableting method and the parameters of the tablet press, such as pressure and holding time, also play a significant role in determining the quality of the final tablets.
Common Grinding Aids and Binders
When preparing powder samples that are difficult to form into tablets, incorporating binders and grinding aids can significantly enhance the process. These additives are typically introduced during the grinding phase, with recommended usage ranging from 5% to 20% of the sample's mass.
Solid Grinding Aids and Binders:
- Starch: Enhances cohesiveness and aids in uniform particle distribution.
- Cellulose: Provides structural integrity and prevents particle aggregation.
- Boric Acid: Acts as a lubricant, reducing friction and improving tablet hardness.
- Yellow Wax Powder: Increases plasticity, facilitating smoother tablet formation.
- Stearic Acid: Serves as a lubricant, preventing adhesion and enhancing tablet quality.
Liquid Grinding Aids:
- Triethanolamine: Improves wetting properties and aids in particle dispersion.
- Anhydrous Ethanol: Enhances solubility and aids in uniform mixing of the sample.
By judiciously selecting and applying these additives, the efficiency and quality of the tableting process can be substantially improved.
Common Tableting Methods
When preparing samples for X-ray fluorescence (XRF) analysis, several tableting methods are commonly employed to ensure the samples are compact and uniform. These methods include the boric acid edging pad bottoming method, the plastic ring sample preparation method, aluminum cup tableting, and steel ring tableting. Each method has its own set of advantages and is chosen based on the specific characteristics of the sample material.
The boric acid edging pad bottoming method involves using boric acid as a binding agent to create a firm base for the sample, ensuring that the tablet remains intact during analysis. This method is particularly useful for samples that are prone to crumbling or breaking apart.
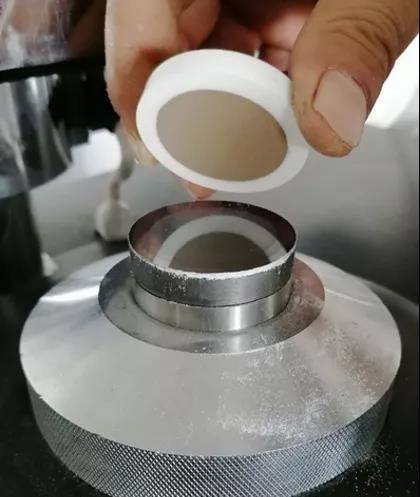
The plastic ring sample preparation method utilizes a plastic ring to contain the sample powder, which is then compressed to form a tablet. This method is advantageous for its ease of use and the ability to create uniform tablets with minimal effort.
Aluminum cup tableting is another common technique where the sample powder is placed in an aluminum cup and compressed. The aluminum material ensures that the sample remains stable and does not react with the sample material, making it suitable for a wide range of samples.
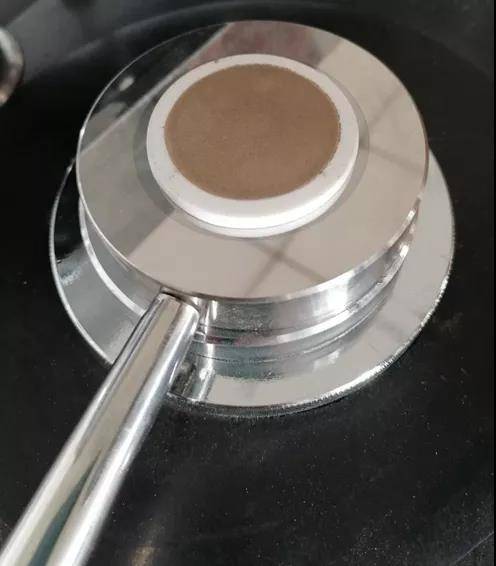
Lastly, steel ring tableting involves using a steel ring to compress the sample powder into a tablet. This method is robust and can handle high pressures, making it ideal for samples that require a stronger binding force.
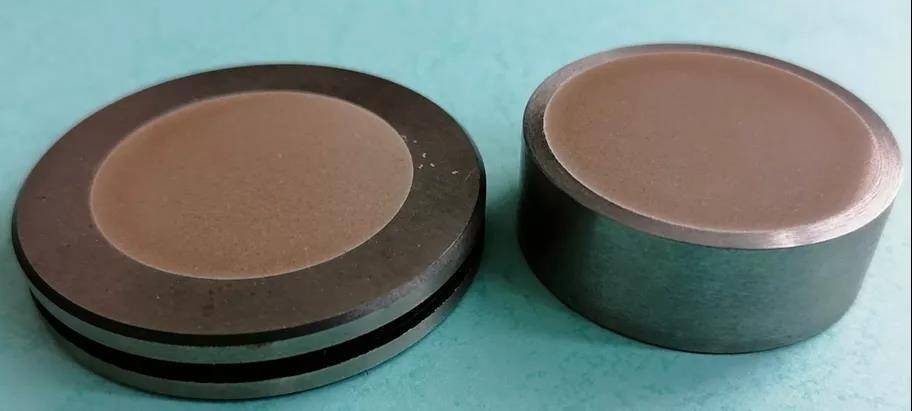
Each of these methods plays a crucial role in ensuring that the sample is prepared correctly for XRF analysis, thereby enhancing the accuracy and reliability of the results.
Tablet Press Parameters
When preparing powder samples for X-ray fluorescence (XRF) analysis, the parameters of the tablet press play a crucial role in ensuring the quality and reproducibility of the tablets. The common pressure settings typically range from 20 to 30 tons. However, adjustments are necessary based on the sample's characteristics:
- Fine and Sticky Samples: For samples that are particularly fine or sticky, the pressure should be reduced to avoid over-compacting. A recommended setting is around 10 tons.
- Ferroalloys: Conversely, for samples like ferroalloys, which require a higher degree of compaction, the pressure can be increased to approximately 40 tons.
The pressure holding time is another critical parameter. The standard holding time is 20 seconds. However, the minimum time should generally not be less than 10 seconds to ensure adequate compaction. Extending the holding time slightly beyond the standard can enhance the tableting effect, but it should not exceed 60 seconds to prevent potential damage to the tablet press or the sample.
Sample Type | Recommended Pressure (tons) | Pressure Holding Time (seconds) |
---|---|---|
Fine and Sticky | 10 | 10-20 |
General | 20-30 | 20 |
Ferroalloys | 40 | 20-30 |
These parameters are essential for producing firm tablets that are free from cracks or delamination, ensuring accurate and reproducible XRF analysis results.
CONTACT US FOR A FREE CONSULTATION
KINTEK LAB SOLUTION's products and services have been recognized by customers around the world. Our staff will be happy to assist with any inquiry you might have. Contact us for a free consultation and talk to a product specialist to find the most suitable solution for your application needs!