Producing carbon nanotubes (CNTs) is a complex process that involves advanced techniques and technologies. While traditional methods like laser ablation and arc discharge were initially used, chemical vapor deposition (CVD) has become the dominant commercial process due to its scalability and efficiency. Emerging methods, such as using green or waste feedstocks, are being explored to make the production process more sustainable. However, these methods face challenges related to material quality and environmental impact. The difficulty in producing CNTs lies in achieving precise control over their structure, purity, and scalability while minimizing costs and environmental harm.
Key Points Explained:
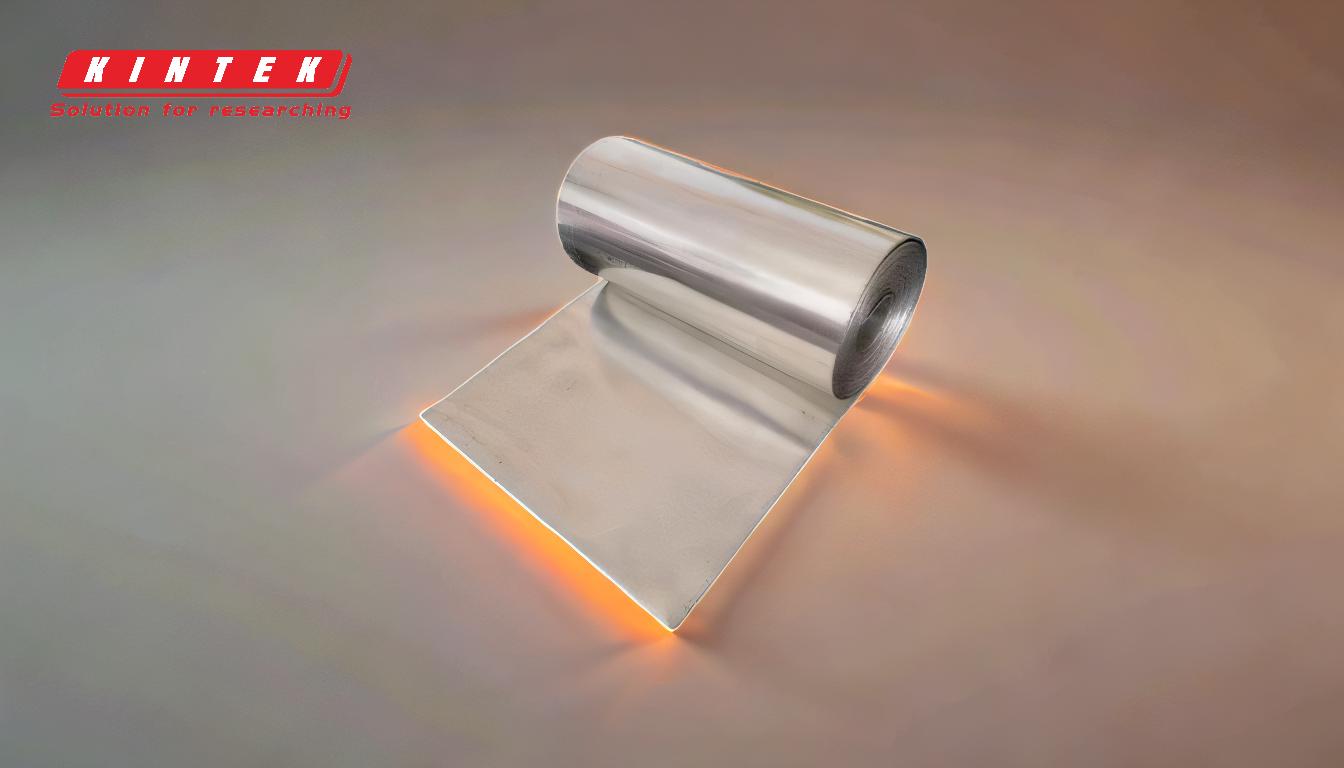
-
Traditional Production Methods:
- Laser Ablation and Arc Discharge: These were among the earliest methods used to produce carbon nanotubes. They involve using high-energy lasers or electric arcs to vaporize carbon and form nanotubes. While effective, these methods are less scalable and more energy-intensive compared to modern techniques.
- Chemical Vapor Deposition (CVD): CVD is the most widely used commercial method today. It involves decomposing carbon-containing gases at high temperatures in the presence of a catalyst to grow nanotubes. CVD offers better control over the size, structure, and purity of CNTs, making it more suitable for large-scale production.
-
Emerging Production Methods:
- Green Feedstocks: Researchers are exploring the use of sustainable feedstocks, such as carbon dioxide captured by electrolysis in molten salts, to produce CNTs. This approach aims to reduce the environmental impact of production. However, there are concerns about the quality and consistency of CNTs produced from such feedstocks.
- Methane Pyrolysis: This method involves breaking down methane into hydrogen and solid carbon, which can then be used to synthesize CNTs. While promising, methane pyrolysis requires careful handling to avoid greenhouse gas emissions, making it a challenging process to implement on a large scale.
-
Challenges in Production:
- Quality Control: Achieving consistent quality in terms of size, structure, and purity is a significant challenge in CNT production. Variations in these parameters can affect the performance of CNTs in various applications.
- Scalability: While CVD is scalable, other methods like laser ablation and arc discharge are less so. Emerging methods using green feedstocks also face scalability issues due to the complexity of the processes involved.
- Environmental Impact: Traditional production methods can be energy-intensive and produce harmful by-products. Emerging methods aim to address these issues but still face challenges in terms of material quality and process efficiency.
-
Applications and Demand:
- Lithium-Ion Batteries: CNTs are used in both cathodes and anodes to improve conductivity and energy density. The growing demand for high-performance batteries in electric vehicles and electronics drives the need for high-quality CNTs.
- Composite Materials: CNTs are used in conductive polymers, fiber-reinforced composites, and other materials to enhance mechanical and electrical properties. This includes applications in concrete, asphalt, and tires.
- Other Applications: CNTs are also used in transparent conductive films, thermal interface materials, and sensors, further increasing the demand for high-quality production.
-
Future Prospects:
- Innovation in Production: Ongoing research focuses on improving production methods, including the use of alternative feedstocks and hybrid products. These innovations aim to make CNT production more sustainable and cost-effective.
- Functionalization and Integration: Beyond production, there is a growing emphasis on functionalizing CNTs to enhance their properties and integrating them into various applications. This includes creating highly conductive continuous yarns and hybrid materials with other additives.
In conclusion, while producing carbon nanotubes is challenging due to the need for precise control over their structure and quality, advancements in production methods like CVD and emerging green technologies are making it more feasible. However, challenges related to scalability, environmental impact, and material quality remain, requiring continued innovation and development in the field.
Summary Table:
Aspect | Details |
---|---|
Traditional Methods | Laser ablation, arc discharge, and CVD (Chemical Vapor Deposition). |
Emerging Methods | Green feedstocks, methane pyrolysis, and sustainable production techniques. |
Challenges | Quality control, scalability, and environmental impact. |
Applications | Lithium-ion batteries, composite materials, sensors, and more. |
Future Prospects | Innovations in production, functionalization, and hybrid materials. |
Interested in learning more about carbon nanotube production? Contact our experts today for tailored solutions!