Yes, aluminum can be melted in an induction furnace. Induction furnaces are specifically designed to handle lower-density metals like aluminum, offering precise temperature control and even heat distribution, which are crucial for maintaining the metal's quality. The process is highly efficient, reducing energy consumption and oxidation losses, making it ideal for both pure aluminum and aluminum alloy production.
Key Points Explained:
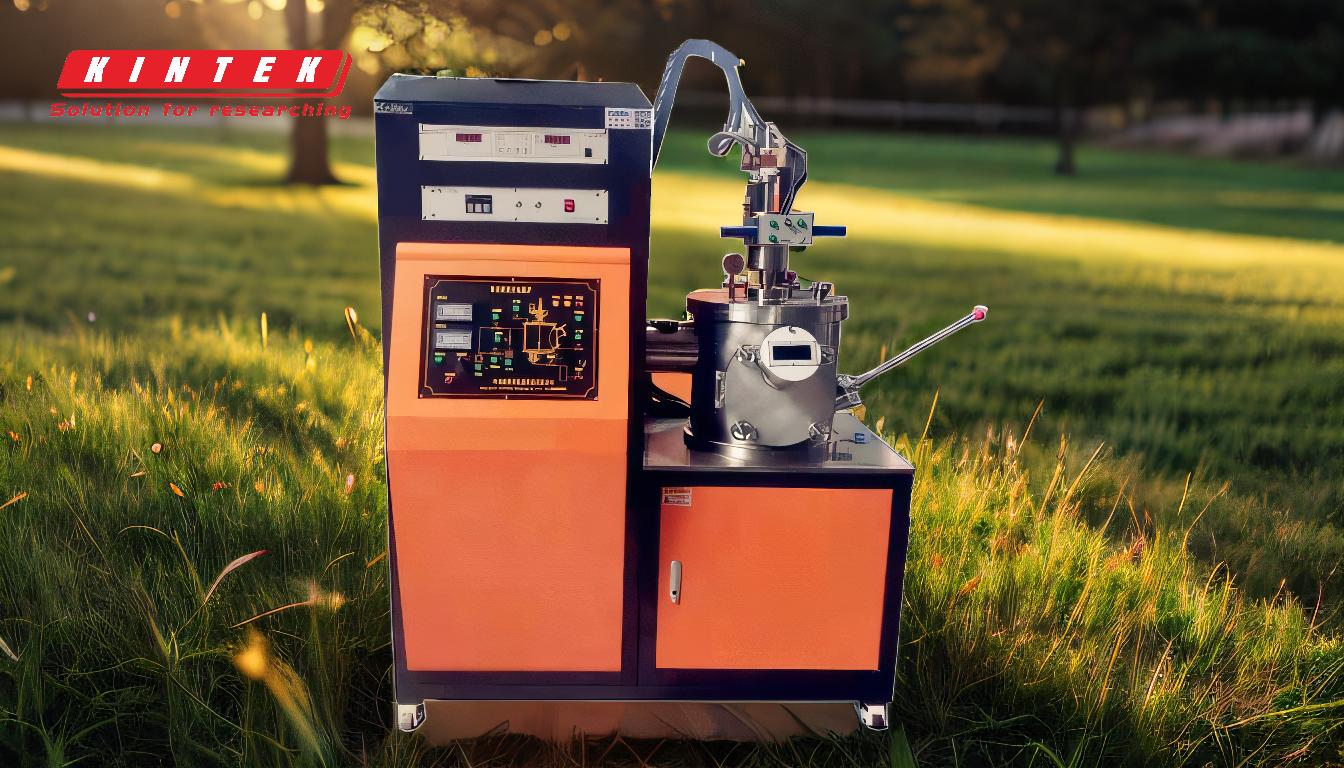
-
Energy Efficiency and Suitability for Aluminum Melting:
- Induction furnaces are highly energy-efficient, which is particularly beneficial for melting aluminum, a process that typically consumes a lot of energy.
- The design of induction furnaces is optimized for lower-density metals like aluminum, ensuring that the metal is heated evenly and efficiently.
-
Mechanism of Induction Melting:
- Induction melting works by passing an alternating electric current through a coil, creating a rapidly reversing magnetic field.
- This magnetic field induces eddy currents within the aluminum, which generate heat through Joule heating. The heat is produced directly within the metal, making the process clean and efficient.
- The frequency of the electric current affects the depth of penetration, with higher frequencies resulting in shallower penetration, which is suitable for aluminum's properties.
-
Temperature Control and Heat Distribution:
- Induction furnaces provide precise temperature control, which is essential for maintaining the quality of aluminum during the melting process.
- The even heat distribution ensures that the aluminum is uniformly heated, reducing the risk of hotspots and preserving the metal's expected lifetime.
-
Stirring Effect and Uniform Mixing:
- The eddy currents not only heat the aluminum but also cause a stirring effect in the molten metal.
- This stirring ensures proper mixing, which is particularly important when producing aluminum alloys, as it ensures that the alloying elements are evenly distributed throughout the molten metal.
-
Reduction of Oxidation Losses:
- Using an induction furnace for melting aluminum can significantly reduce oxidation losses, which is a common issue in traditional melting processes.
- The efficiency of induction melting can lead to a reduction in oxidation losses by 60% to 75%, making it a more cost-effective and environmentally friendly option.
-
Separation of Impurities:
- During the melting process, pure aluminum sinks due to its higher density, while impurities rise to the surface.
- These impurities can be easily removed using a tilting mechanism, leaving behind high-purity aluminum, which is essential for producing quality aluminum products.
In summary, induction furnaces are not only capable of melting aluminum but are also highly efficient and effective for this purpose. They offer precise temperature control, even heat distribution, and reduced oxidation losses, making them an excellent choice for both pure aluminum and aluminum alloy production.
Summary Table:
Key Benefits of Induction Furnaces for Aluminum Melting |
---|
Energy Efficiency |
Precise Temperature Control |
Even Heat Distribution |
Stirring Effect |
Reduced Oxidation Losses |
Impurity Separation |
Ready to enhance your aluminum melting process? Contact us today to learn more about induction furnace solutions!