Induction furnaces are highly efficient and clean melting systems commonly used for ferrous and non-ferrous alloys. While they excel at melting metals like iron, steel, copper, and aluminum, their ability to melt titanium depends on the furnace's design and operating conditions. Standard induction furnaces can reach temperatures up to 1800°C, which is sufficient for titanium's melting point of 1668°C. However, titanium's high reactivity with oxygen and nitrogen at high temperatures requires specialized conditions, such as a vacuum or inert gas environment, to prevent contamination. Laboratory vacuum induction furnaces, equipped with precise temperature control and protective atmospheres, are capable of melting titanium effectively, making them suitable for high-precision applications.
Key Points Explained:
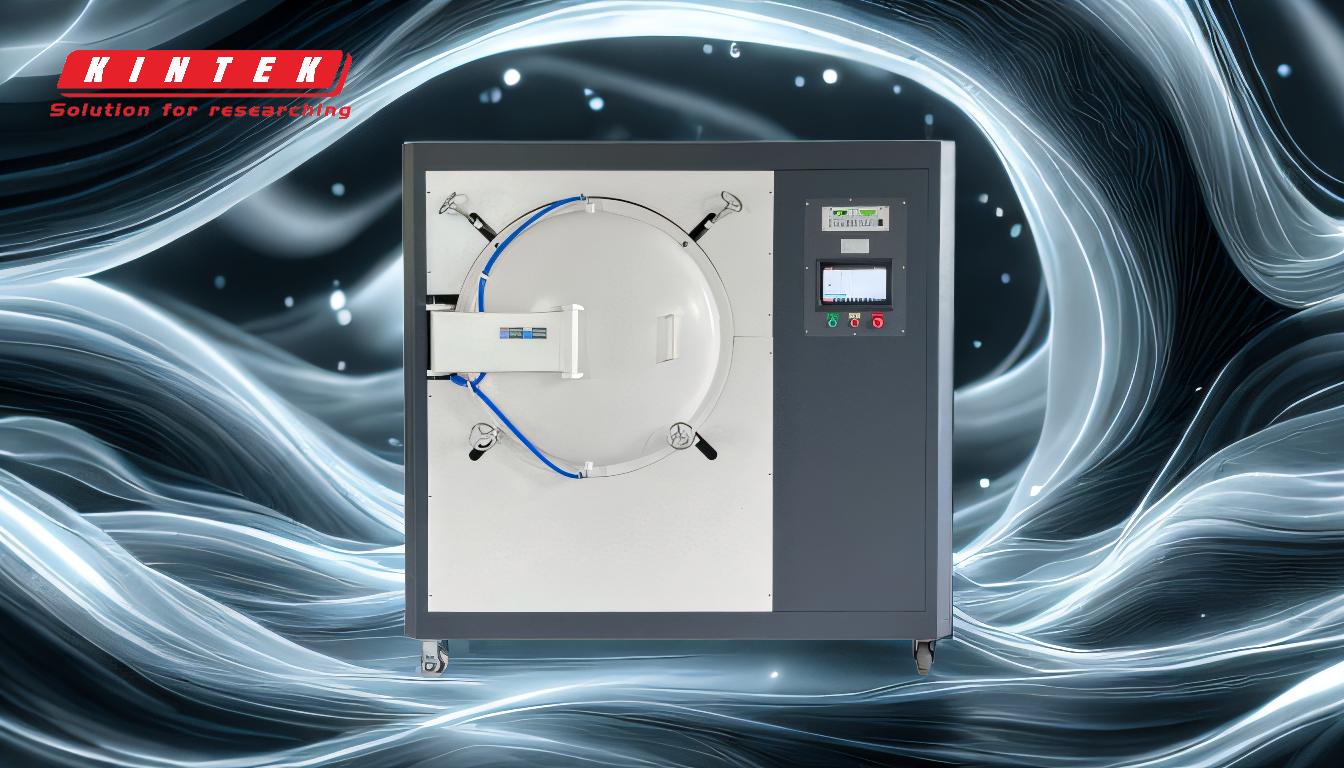
-
Induction Furnace Basics:
- Induction furnaces use electromagnetic fields to generate heat within the metal charge, making them energy-efficient and clean.
- They can reach temperatures up to 1800°C, which is sufficient for melting most metals, including titanium.
- The furnace's design includes a water-cooled copper coil, power supply, and control system, ensuring precise temperature regulation.
-
Titanium's Melting Requirements:
- Titanium has a melting point of 1668°C, which is within the operational range of most induction furnaces.
- However, titanium is highly reactive with oxygen and nitrogen at high temperatures, requiring a controlled atmosphere to prevent contamination.
- Standard induction furnaces may not provide the necessary environment for melting titanium without compromising its quality.
-
Specialized Induction Furnaces for Titanium:
- Laboratory vacuum induction furnaces are designed to melt metals under vacuum or protective gas, making them suitable for titanium.
- These furnaces feature precise temperature control, electromagnetic stirring, and high vacuum degassing capabilities, ensuring high-quality melts.
- They are ideal for processing high-purity metals and alloys, including titanium, in metallurgical and research applications.
-
Advantages of Using Induction Furnaces for Titanium:
- Clean Melting Process: Induction furnaces do not require combustion or arcs, reducing contamination risks.
- Precise Temperature Control: Ensures uniform heating and minimizes thermal stress on the material.
- Energy Efficiency: Induction heating generates heat directly within the metal, reducing energy waste.
- Controlled Atmosphere: Vacuum or inert gas environments prevent oxidation and maintain material integrity.
-
Limitations and Considerations:
- Standard induction furnaces may not be suitable for titanium without modifications to handle its reactivity.
- The cost of specialized vacuum induction furnaces can be higher, making them more suitable for high-precision applications rather than large-scale industrial use.
- Proper handling of titanium in induction furnaces requires expertise to ensure optimal results.
In summary, while standard induction furnaces can theoretically melt titanium due to their high-temperature capabilities, the metal's reactivity necessitates specialized equipment like vacuum induction furnaces. These systems provide the controlled environment needed to melt titanium without contamination, making them ideal for high-precision and research applications.
Summary Table:
Aspect | Details |
---|---|
Induction Furnace Basics | - Uses electromagnetic fields for heating - Reaches up to 1800°C |
Titanium Melting Point | 1668°C, within furnace range but requires controlled atmosphere |
Specialized Furnaces | Vacuum induction furnaces with protective gas environments |
Advantages | - Clean melting - Precise temperature control - Energy-efficient |
Limitations | - High cost - Requires expertise - Best for high-precision applications |
Need a vacuum induction furnace for titanium melting? Contact our experts today to find the perfect solution!