Yes, an induction heater can melt metal. Induction heating is a highly efficient and reliable method for melting a wide range of metals, including both ferrous and non-ferrous metals. This technology uses electromagnetic induction to generate heat through electro-thermal conversion, which is then used to melt the metal. The process involves a coil made of conductive material, such as copper, through which an electrical current flows, creating a magnetic field. This magnetic field induces eddy currents in the metal, generating heat and raising the temperature to the metal's melting point. Induction furnaces are capable of reaching extremely high temperatures, making them suitable for melting metals with high melting points, such as steel, as well as precious metals like gold and silver.
Key Points Explained:
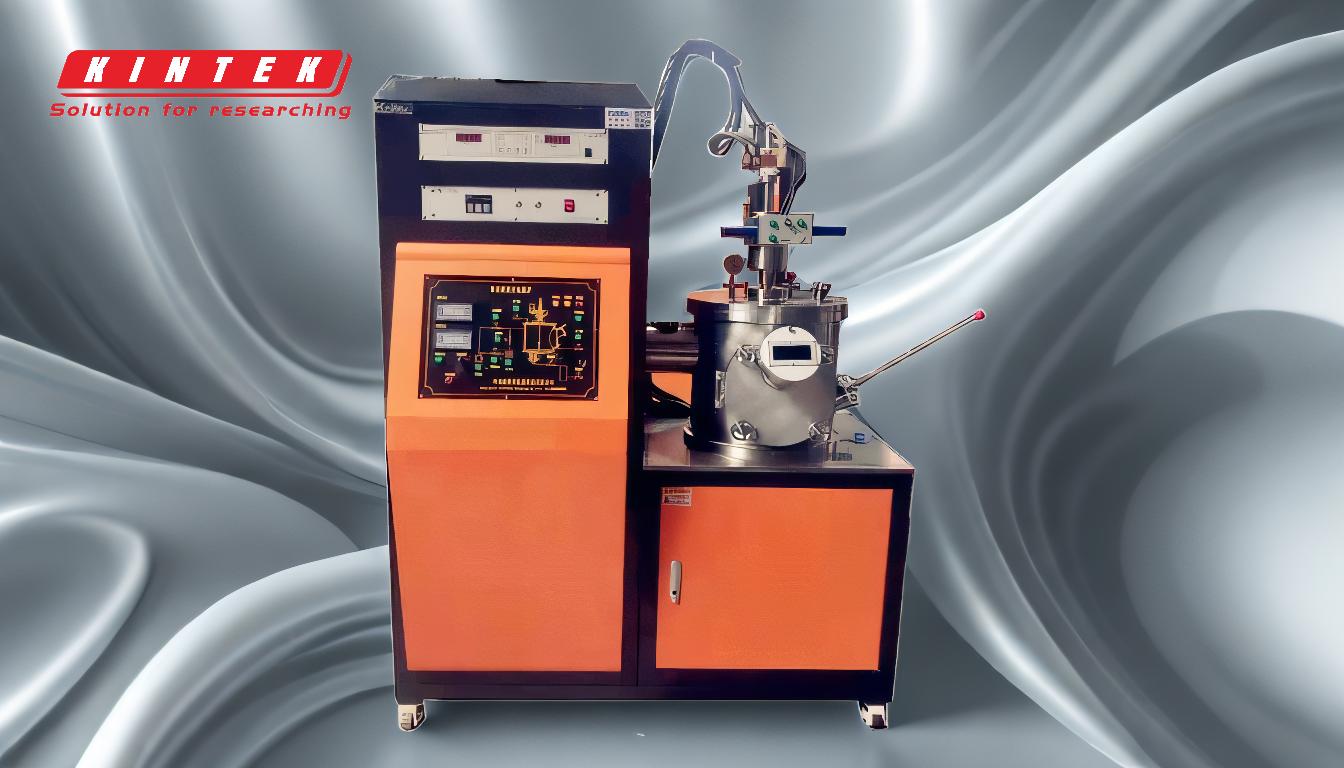
-
Principle of Induction Heating:
- Induction heating works by using electromagnetic induction to generate heat. An alternating current passes through a coil, creating a magnetic field. When a conductive metal is placed within this field, eddy currents are induced in the metal, generating heat through resistance. This process is highly efficient and allows for precise temperature control.
-
Types of Metals That Can Be Melted:
- Ferrous Metals: These include iron and its alloys, such as steel. Induction furnaces can reach temperatures high enough to melt steel, which has a melting point of approximately 1370°C (2500°F).
- Non-Ferrous Metals: These include metals like copper, aluminum, brass, and bronze. Induction heating is also effective for melting these metals, which generally have lower melting points compared to ferrous metals.
- Precious Metals: Induction heating is widely used for melting precious metals such as gold, silver, platinum, and palladium. The precise temperature control offered by induction heating is particularly beneficial for these high-value materials.
-
Components of an Induction Furnace:
- Induction Coil: Typically made of copper, the coil is the primary component that generates the magnetic field. The coil's design and the frequency of the alternating current can be adjusted to suit different types of metals and melting requirements.
- Crucible: The metal to be melted is placed inside a crucible, which is usually made of a refractory material that can withstand high temperatures. The crucible is positioned within the induction coil.
- Power Supply: The power supply provides the alternating current necessary to generate the magnetic field. The power supply can be adjusted to control the intensity of the magnetic field and, consequently, the amount of heat generated.
-
Advantages of Induction Heating for Metal Melting:
- Efficiency: Induction heating is highly efficient because it directly heats the metal, minimizing heat loss. This results in faster melting times and lower energy consumption compared to traditional melting methods.
- Precision: The temperature can be precisely controlled, which is crucial for melting metals with specific melting points or for processes that require consistent quality.
- Cleanliness: Induction melting is a clean process because it does not involve combustion, reducing the risk of contamination from by-products like soot or ash.
- Versatility: Induction furnaces can be used to melt a wide variety of metals, making them suitable for diverse applications, from industrial metalworking to jewelry making.
-
Applications of Induction Metal Melting:
- Industrial Metalworking: Induction furnaces are used in industries that require large-scale metal melting, such as steel production, automotive manufacturing, and aerospace engineering.
- Jewelry Making: The precise temperature control and clean melting process make induction heating ideal for melting precious metals used in jewelry.
- Small-Scale and Laboratory Use: Induction heaters are also used in smaller-scale applications, such as in laboratories or for custom metalworking projects, where precise control over the melting process is essential.
-
Temperature Capabilities:
- Induction furnaces can achieve extremely high temperatures, making them suitable for melting metals with high melting points. For example, steel melts at around 1370°C (2500°F), and induction furnaces can easily reach and maintain these temperatures.
In summary, induction heaters are highly effective for melting a wide range of metals, offering advantages in efficiency, precision, and cleanliness. The technology is versatile and can be applied in various industrial and small-scale settings, making it a valuable tool for metal melting processes.
Summary Table:
Key Aspect | Details |
---|---|
Principle of Induction Heating | Uses electromagnetic induction to generate heat through eddy currents. |
Types of Metals | Ferrous (e.g., steel), Non-Ferrous (e.g., copper), Precious (e.g., gold). |
Components | Induction coil, crucible, power supply. |
Advantages | High efficiency, precise temperature control, clean process, versatility. |
Applications | Industrial metalworking, jewelry making, small-scale/laboratory use. |
Temperature Capabilities | Can reach up to 1370°C (2500°F) for melting steel and other high-melt metals. |
Unlock the potential of induction heating for your metal melting needs—contact our experts today!