Brazing is indeed a viable method for joining ferrous metals, such as steel and cast iron. It involves using a filler metal with a lower melting point than the base metals being joined, allowing the filler to flow into the joint by capillary action. The process requires careful selection of materials, including the filler metal and flux, to ensure a strong, durable bond. Flux plays a critical role in brazing by removing oxides and promoting wetting, but it must be compatible with both the base and filler metals to avoid issues like brittleness or corrosion. Proper post-brazing cleaning is also essential to remove excess flux and ensure the integrity of the joint.
Key Points Explained:
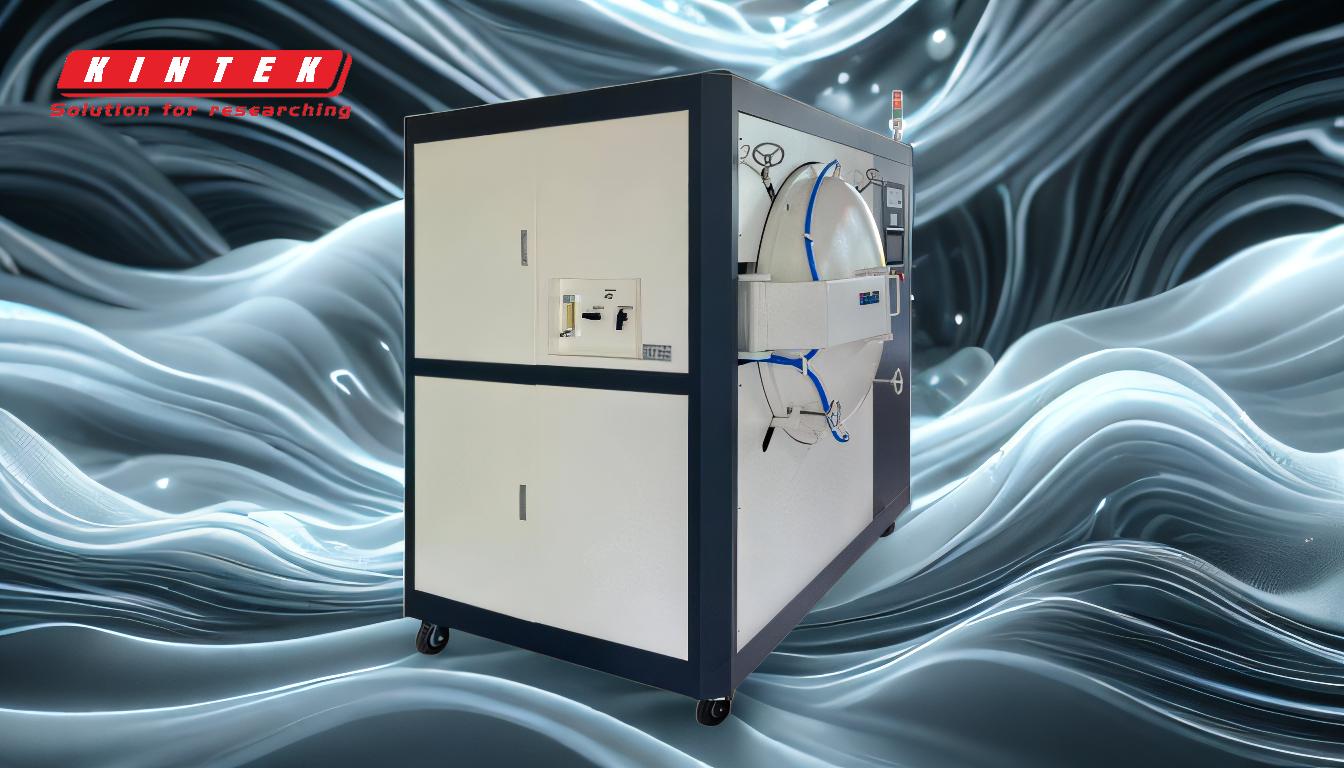
-
Brazing is Suitable for Ferrous Metals
- Brazing can be effectively used for ferrous metals, including steel and cast iron. The process relies on capillary action to draw the molten filler metal into the joint, creating a strong bond without melting the base metals. This makes it an excellent choice for joining ferrous materials in applications requiring high strength and durability.
-
Importance of Flux Selection
- Flux is a critical component in brazing, as it removes oxides from the metal surfaces and promotes the wetting of the filler metal. However, the flux must be chemically compatible with both the base metal and the filler metal. For example, using phosphorus-containing filler alloys on iron or nickel can lead to the formation of brittle phosphides, which weaken the joint. Therefore, selecting the right flux for the specific base metal is essential.
-
Flux Activity and Brazing Cycles
- The activity level of the flux should match the brazing cycle. Longer brazing cycles typically require less active flux, as the extended heating time allows the flux to work effectively. Conversely, shorter cycles may need more active flux to ensure proper oxide removal and wetting within the limited time frame.
-
Post-Brazing Cleaning
- Excess flux must be removed after brazing to prevent potential issues. Residual flux can cause corrosion, hinder joint inspection, and interfere with further surface finishing processes. Proper cleaning ensures the joint's integrity and longevity.
-
Advantages of Brazing Ferrous Metals
- Brazing offers several advantages for ferrous metals, including the ability to join dissimilar metals, minimal distortion of the base materials, and the creation of leak-tight joints. These benefits make brazing a preferred method for many industrial applications involving ferrous metals.
By carefully selecting the appropriate filler metal and flux, and following proper brazing and cleaning procedures, ferrous metals can be successfully joined using brazing techniques. This method provides a reliable and efficient solution for a wide range of applications.
Summary Table:
Key Aspect | Details |
---|---|
Suitable for Ferrous Metals | Effective for steel and cast iron, using capillary action for strong bonds. |
Flux Selection | Critical for oxide removal and wetting; must be compatible with base metals. |
Flux Activity | Match flux activity to brazing cycle length for optimal results. |
Post-Brazing Cleaning | Essential to remove excess flux and prevent corrosion or joint issues. |
Advantages | Joins dissimilar metals, minimizes distortion, and creates leak-tight joints. |
Learn how brazing can enhance your metal joining processes—contact our experts today for tailored solutions!