Yes, copper can be melted in an induction furnace. Induction furnaces are highly effective for melting metals, including copper, due to their ability to generate heat directly within the metal through electromagnetic induction. The process involves creating a magnetic field using an alternating current in a coil, which induces eddy currents in the copper, generating heat and melting it. Induction furnaces are clean, efficient, and provide uniform heating, making them suitable for melting copper and other conductive metals.
Key Points Explained:
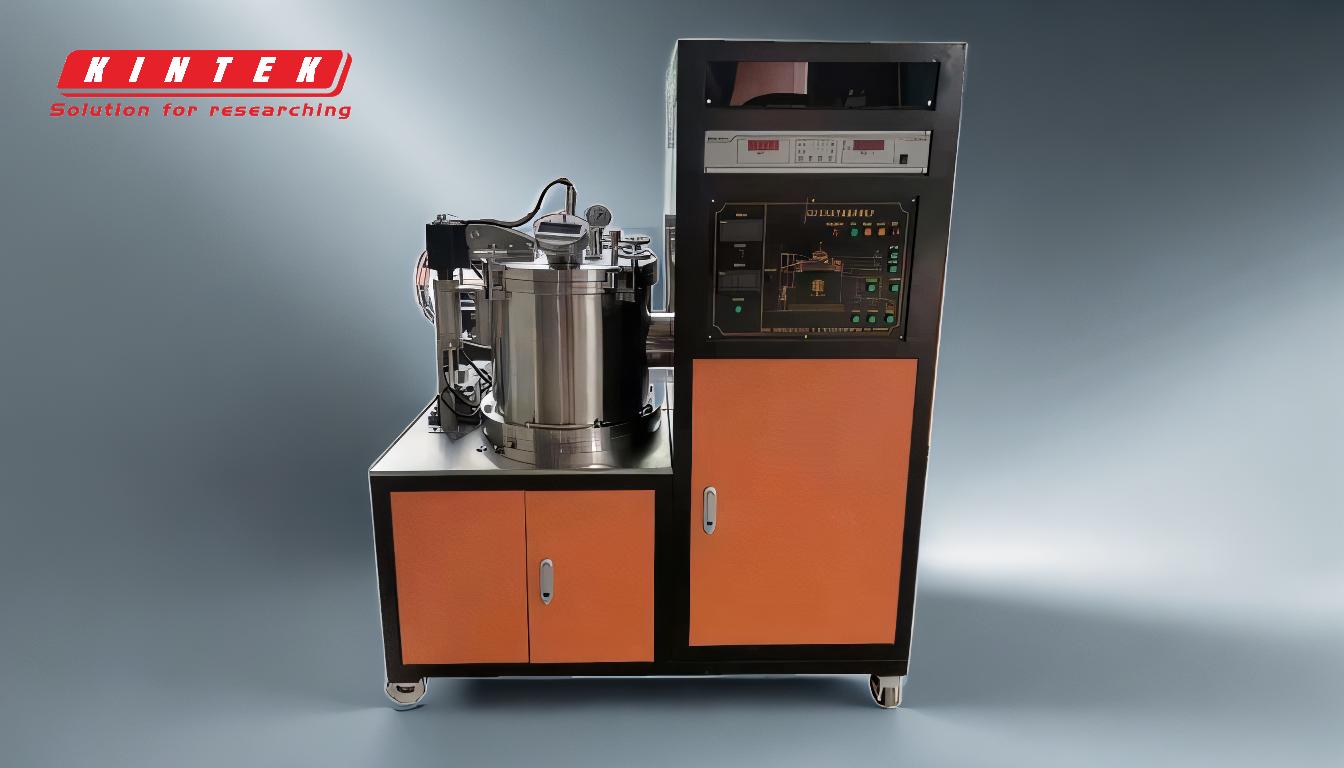
-
How Induction Furnaces Work:
- Induction furnaces use electromagnetic induction to heat and melt metals.
- An alternating current passes through a coil, creating a magnetic field.
- The magnetic field induces eddy currents in the metal (copper in this case), generating heat through resistance (Joule heating).
- The heat is produced directly within the metal, making the process efficient and clean.
-
Suitability for Melting Copper:
- Copper is a highly conductive metal, making it ideal for induction melting.
- The eddy currents induced in copper generate sufficient heat to melt it, as copper has a melting point of 1085°C (1985°F).
- Induction furnaces can reach temperatures well above this, ensuring efficient melting.
-
Advantages of Using Induction Furnaces for Copper:
- Uniform Heating: The electromagnetic stirring effect ensures even temperature distribution, reducing impurities and dross.
- Energy Efficiency: Heat is generated directly within the metal, minimizing energy loss.
- Precision and Control: Induction furnaces allow precise temperature control, which is crucial for maintaining the quality of molten copper.
- Clean Process: Since heat is generated internally, there is less contamination compared to other melting methods.
-
Inductive Stirring:
- The magnetic field causes the molten copper to move, a phenomenon known as inductive stirring.
- This stirring ensures a uniform mix, aids in alloying (if required), and prevents temperature gradients.
-
Frequency Considerations:
- The frequency of the alternating current affects the depth of current penetration into the metal.
- Higher frequencies result in shallower penetration, which is suitable for smaller batches or thin copper pieces.
- Lower frequencies are used for larger volumes of copper, ensuring deeper penetration and efficient melting.
-
Applications of Induction Melting for Copper:
- Induction furnaces are widely used in foundries and metal casting operations.
- They are ideal for producing high-quality copper alloys, electrical components, and other copper-based products.
- The process is also used for recycling copper scrap, as it ensures minimal oxidation and material loss.
-
Comparison with Other Melting Methods:
- Induction melting is faster and more energy-efficient than traditional methods like gas or coal-fired furnaces.
- It produces less environmental pollution and offers better control over the melting process.
- Unlike crucible furnaces, induction furnaces do not require external heat sources, reducing operational costs.
-
Equipment Requirements:
- A typical induction furnace for melting copper includes a copper coil, a power unit, and a crucible to hold the metal.
- The furnace must be designed to handle the high temperatures required for melting copper and ensure safety during operation.
In summary, induction furnaces are highly effective for melting copper due to their efficiency, precision, and ability to produce high-quality molten metal. Their design and operational principles make them suitable for a wide range of industrial applications involving copper and other conductive metals.
Summary Table:
Key Aspect | Details |
---|---|
How It Works | Uses electromagnetic induction to generate heat directly within the metal. |
Suitability for Copper | Ideal due to copper's high conductivity and melting point (1085°C/1985°F). |
Advantages | Uniform heating, energy efficiency, precision, and clean process. |
Applications | Foundries, metal casting, copper alloy production, and recycling. |
Frequency Considerations | Higher frequencies for small batches, lower frequencies for large volumes. |
Comparison | Faster, more efficient, and cleaner than gas or coal-fired furnaces. |
Ready to enhance your copper melting process? Contact us today to learn more about induction furnaces!