Diamond-like carbon (DLC) coatings are highly versatile and can be applied to various materials, including metals, to enhance their properties. While DLC coatings are commonly applied to steel and other hard materials, applying them to aluminum presents unique challenges due to aluminum's softness and low melting point. However, with proper surface preparation and advanced deposition techniques, DLC coatings can indeed be applied to aluminum, offering benefits such as improved wear resistance, reduced friction, and enhanced corrosion resistance. The process requires careful control of parameters like temperature and adhesion layers to ensure the coating's durability and performance.
Key Points Explained:
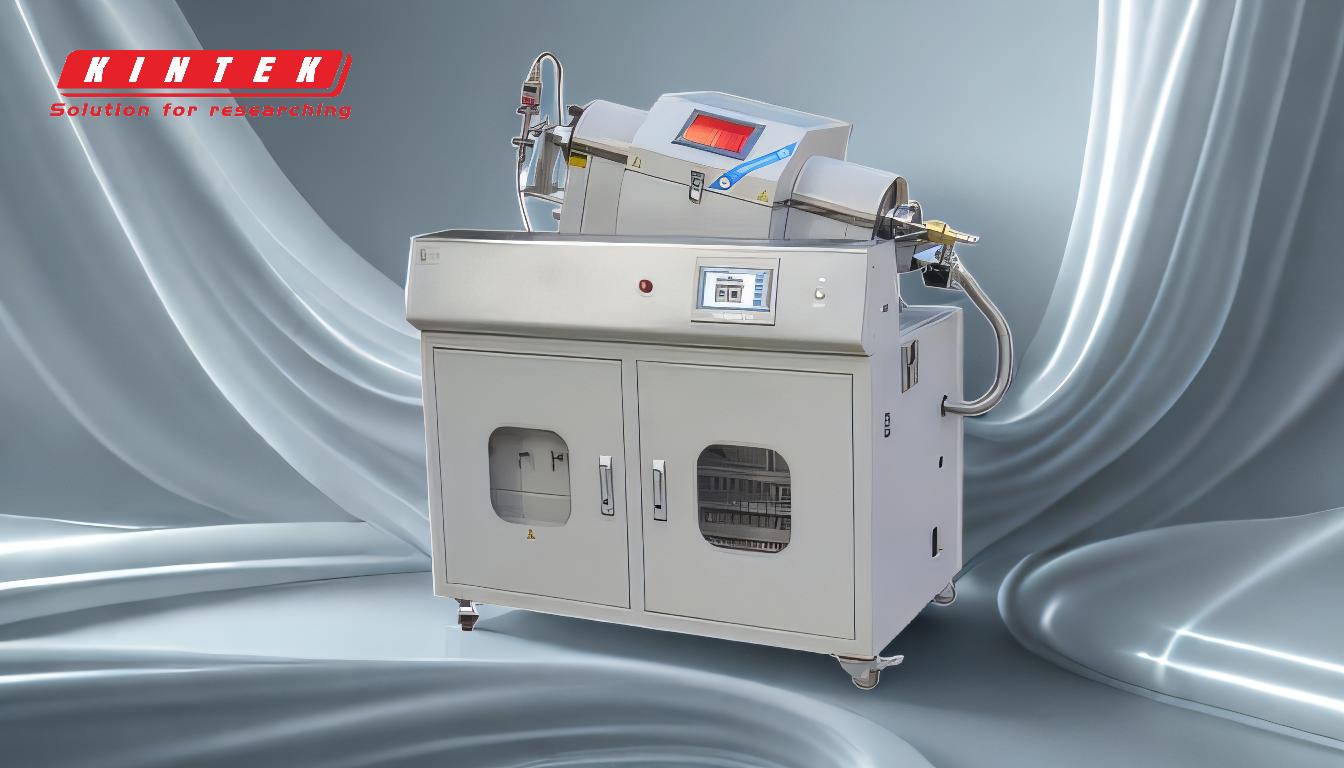
-
DLC Coating Properties and Applications:
- DLC coatings are known for their high hardness (1500–3000 HV), low coefficient of friction, and excellent wear resistance.
- They are used in industries such as automotive, machinery, medical, and decorative applications due to their tribological and chemical inertness properties.
- DLC coatings combine diamond-like hardness with graphite-like lubricity, making them ideal for sliding and rolling applications.
-
Challenges of Applying DLC to Aluminum:
- Aluminum is a soft material with a low melting point, which complicates the deposition process.
- Poor adhesion of DLC coatings to aluminum can occur due to the material's surface properties and thermal expansion mismatch.
- High deposition temperatures can damage aluminum substrates, requiring precise control during the coating process.
-
Surface Preparation and Adhesion Layers:
- To improve adhesion, aluminum surfaces often require pre-treatment, such as plasma cleaning or etching, to remove oxides and contaminants.
- Intermediate adhesion layers, such as silicon or chromium, can be applied to enhance bonding between the aluminum substrate and the DLC coating.
- These layers act as a buffer, reducing thermal and mechanical stress and improving coating durability.
-
Deposition Techniques for Aluminum:
- Plasma-assisted chemical vapor deposition (PACVD) is a common method for applying DLC coatings to aluminum.
- PACVD allows for low-temperature deposition, minimizing the risk of substrate damage.
- The process involves introducing hydrocarbon gases into a plasma environment, where they decompose and form a hard, durable carbon film on the aluminum surface.
-
Benefits of DLC-Coated Aluminum:
- Enhanced wear resistance: DLC coatings protect aluminum components from abrasion and prolong their lifespan.
- Reduced friction: The low coefficient of friction improves the efficiency of sliding and rolling components.
- Corrosion resistance: DLC coatings provide a protective barrier against chemical and environmental degradation.
- Decorative applications: The black, glossy finish of DLC coatings is aesthetically appealing for consumer products like watches and automotive trims.
-
Applications of DLC-Coated Aluminum:
- Automotive: Lightweight aluminum components with DLC coatings are used in engines, transmissions, and bearings to reduce weight and improve performance.
- Aerospace: DLC coatings on aluminum parts enhance durability and reduce maintenance requirements in harsh environments.
- Medical: Biocompatible DLC coatings on aluminum implants improve wear resistance and reduce the risk of adverse reactions.
- Consumer goods: Aluminum products like watches, smartphones, and eyewear benefit from the scratch resistance and luxurious appearance of DLC coatings.
-
Limitations and Considerations:
- The cost of applying DLC coatings to aluminum can be higher due to the need for specialized equipment and surface preparation.
- The coating thickness must be carefully controlled to avoid delamination or cracking under mechanical stress.
- While DLC coatings improve aluminum's properties, they may not be suitable for applications requiring extreme hardness or high-temperature resistance.
In conclusion, DLC coatings can be successfully applied to aluminum with the right techniques and surface preparation. The process enhances aluminum's mechanical and tribological properties, making it suitable for a wide range of industrial and consumer applications. However, careful consideration of the challenges and costs is necessary to ensure optimal performance and durability.
Summary Table:
Aspect | Details |
---|---|
DLC Coating Properties | High hardness (1500–3000 HV), low friction, wear resistance, chemical inertness |
Challenges | Aluminum's softness, low melting point, adhesion issues, temperature control |
Preparation | Plasma cleaning, etching, adhesion layers (silicon/chromium) |
Deposition Technique | Plasma-assisted chemical vapor deposition (PACVD) |
Benefits | Wear resistance, reduced friction, corrosion protection, decorative finish |
Applications | Automotive, aerospace, medical, consumer goods |
Limitations | Higher cost, thickness control, unsuitable for extreme hardness/temperature |
Interested in enhancing your aluminum components with DLC coatings? Contact us today to learn more!