Vacuuming a furnace, particularly a vacuum furnace, is not a standard maintenance practice and can potentially harm the equipment if not done correctly. Vacuum furnaces are designed to operate under specific conditions, including maintaining a controlled environment free from contaminants. Regular maintenance, such as cleaning the muffle chamber and replacing worn-out components, is crucial for extending the furnace's lifespan and ensuring consistent performance. However, vacuuming the furnace is not typically recommended unless specified by the manufacturer. Instead, focus on following proper maintenance protocols, monitoring the equipment's technical status, and adhering to operating rules to ensure optimal performance and longevity.
Key Points Explained:
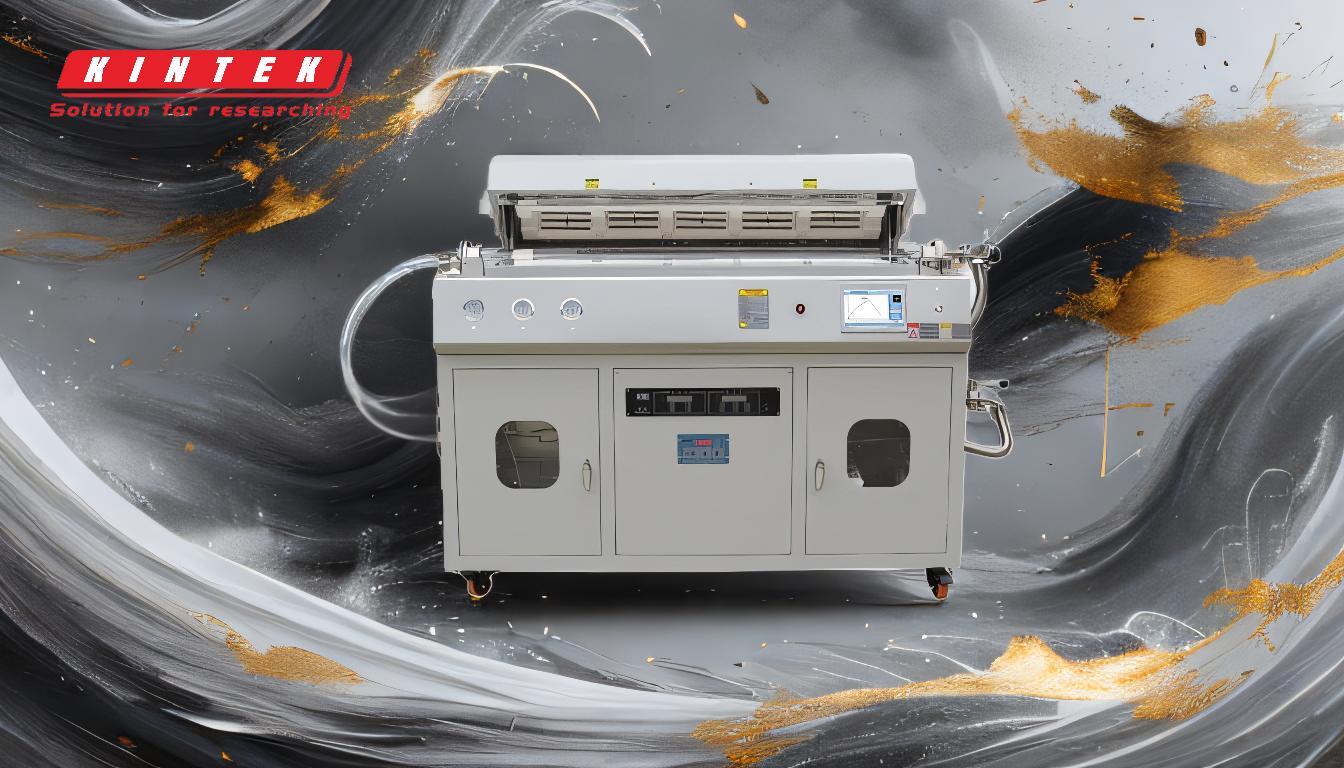
-
Understanding Vacuum Furnace Characteristics:
- Vacuum furnaces operate at high temperatures (800–3,000 °C) and extremely low vacuum levels (as low as 1×10−11 torrs). They are designed to minimize contamination and ensure precise temperature control.
- These furnaces are highly efficient, with quick cooling capabilities and computer-controlled processes for repeatability. Their design ensures low contamination and uniform heating, making them ideal for sensitive applications.
-
Maintenance Practices for Vacuum Furnaces:
- Regular maintenance is essential to ensure the furnace operates efficiently. This includes cleaning the muffle chamber and replacing damaged or worn-out components.
- Establishing operating rules, maintaining detailed records, and preparing spare parts in advance are critical for long-term performance.
- Monitoring the equipment's technical status helps detect early signs of failure and prevents unexpected downtime.
-
Why Vacuuming a Furnace is Not Recommended:
- Vacuum furnaces are designed to maintain a controlled environment. Introducing external vacuuming methods can disrupt this environment and potentially damage sensitive components.
- Instead of vacuuming, focus on manufacturer-recommended cleaning methods, such as using appropriate tools and materials to remove debris or contaminants.
-
Best Practices for Cleaning and Maintenance:
- Use soft brushes or compressed air to remove dust or debris from the furnace chamber.
- Avoid using abrasive materials or harsh chemicals that could damage the furnace's interior.
- Regularly inspect and replace gaskets, seals, and other components to maintain the furnace's vacuum integrity.
-
Ensuring Safety and Efficiency:
- Vacuum furnaces often have safety features, such as automatic power-off when the furnace door is opened. Always follow safety protocols during maintenance.
- Proper maintenance not only extends the furnace's lifespan but also ensures consistent and accurate results, reducing operational costs in the long run.
By adhering to these guidelines, you can maintain your vacuum furnace effectively without resorting to unnecessary or potentially harmful practices like vacuuming. Always consult the manufacturer's manual for specific maintenance instructions tailored to your equipment.
Summary Table:
Key Topic | Details |
---|---|
Vacuum Furnace Characteristics | Operates at 800–3,000 °C, low vacuum levels (1×10−11 torrs), precise control. |
Maintenance Practices | Clean muffle chamber, replace worn parts, monitor technical status. |
Why Vacuuming is Harmful | Disrupts controlled environment, risks damaging sensitive components. |
Best Cleaning Methods | Use soft brushes, compressed air; avoid abrasives or harsh chemicals. |
Safety and Efficiency | Follow safety protocols, ensure consistent performance, reduce costs. |
Need expert advice on maintaining your vacuum furnace? Contact us today for tailored solutions!