Induction melting is a highly efficient and versatile method for melting a wide range of metals, including ferrous metals like steel and iron, as well as non-ferrous metals such as aluminum, copper, and precious metals like gold and silver. This process utilizes electromagnetic induction to generate heat, which is then used to melt the metal. Induction furnaces are favored in modern foundries due to their ability to create high temperatures, ensure uniform mixing of alloying elements, and provide a cleaner and more controlled melting process compared to traditional methods like reverberatory furnaces or cupolas. This method is particularly beneficial for melting refractory metals and is widely used in industries requiring precise temperature control and high-quality metal melts.
Key Points Explained:
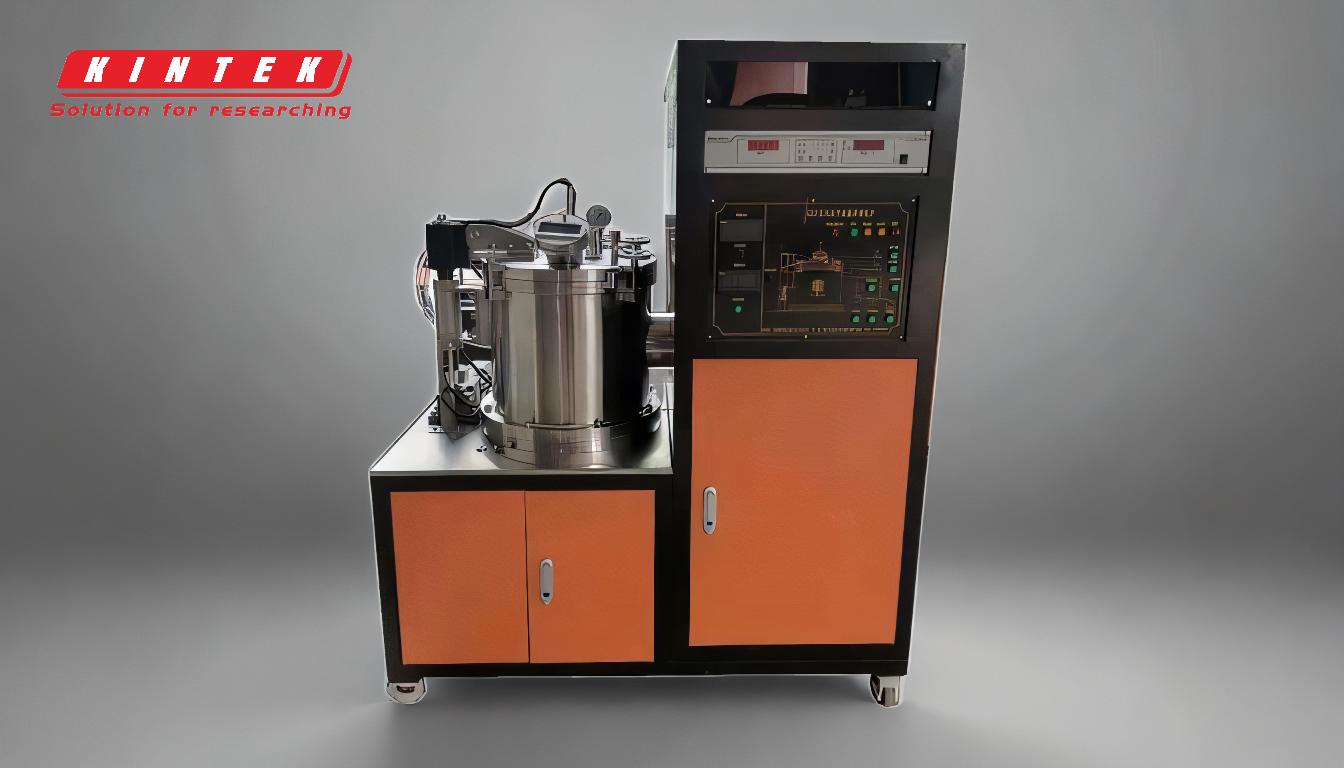
-
How Induction Melting Works:
- Induction melting relies on electromagnetic induction to generate heat. A high-frequency alternating current is passed through a coil, creating a magnetic field. When a conductive metal is placed within this field, eddy currents are induced in the metal, generating heat through resistance. This heat raises the metal's temperature to its melting point.
- The process is highly efficient because the heat is generated directly within the metal, minimizing energy loss and ensuring rapid heating.
-
Types of Metals That Can Be Melted:
- Ferrous Metals: Induction furnaces are capable of melting iron and its alloys, such as steel. These metals are commonly used in industries like construction, automotive, and manufacturing.
- Non-Ferrous Metals: The process is also suitable for non-ferrous metals like aluminum, copper, brass, and bronze. These metals are often used in electrical, aerospace, and decorative applications.
- Precious Metals: Induction melting is widely used for precious metals such as gold, silver, platinum, and palladium. This is particularly important in jewelry making, electronics, and other high-precision industries.
- Refractory Metals: Induction furnaces are ideal for melting refractory metals, which have high melting points and require precise temperature control.
-
Advantages of Induction Melting:
- Clean and Efficient: Induction furnaces produce fewer emissions and waste compared to traditional melting methods like cupolas or reverberatory furnaces. This makes them environmentally friendly and cost-effective.
- Precision and Control: The process allows for precise temperature control, which is crucial for achieving consistent metal quality and avoiding defects.
- Uniform Mixing: The high-frequency magnetic field not only melts the metal but also stirs it, ensuring that alloying elements are evenly distributed throughout the melt. This results in a homogeneous final product.
- Rapid Heating: Induction heating is faster than conventional methods, reducing production time and increasing throughput.
-
Applications of Induction Melting:
- Foundries: Induction furnaces are widely used in modern foundries for melting and casting metals. They are particularly favored for their ability to handle a variety of metals and alloys.
- Jewelry Making: The precision and cleanliness of induction melting make it ideal for working with precious metals in jewelry production.
- Electronics and Aerospace: Induction melting is used to produce high-quality metals and alloys required in electronics, aerospace, and other high-tech industries.
- Recycling: Induction furnaces are also used in metal recycling processes, where they efficiently melt down scrap metal for reuse.
-
Comparison with Traditional Melting Methods:
- Cupolas: Cupolas are traditional furnaces used primarily for melting iron. They are less efficient and produce more emissions compared to induction furnaces.
- Reverberatory Furnaces: These furnaces use combustion to generate heat, which is then transferred to the metal. They are less precise and have higher energy losses compared to induction furnaces.
- Electric Arc Furnaces: While electric arc furnaces are also used for melting metals, they are typically more suitable for large-scale operations and may not offer the same level of precision as induction furnaces.
-
Indirect Heating for Non-Conductive Materials:
- While induction heating is primarily used for conductive materials like metals, it can also be applied to non-conductive materials indirectly. For example, a conductive metal inductor can be heated using induction, and the heat can then be transferred to a non-conductive material like plastic. This method is useful in applications where direct heating of non-conductive materials is not possible.
In conclusion, induction melting is a highly effective and versatile method for melting a wide range of metals. Its advantages in terms of efficiency, precision, and environmental impact make it a preferred choice in various industries, from foundries to jewelry making and beyond.
Summary Table:
Aspect | Details |
---|---|
How It Works | Uses electromagnetic induction to generate heat directly within the metal. |
Metals Melted | Ferrous (steel, iron), non-ferrous (aluminum, copper), precious (gold, silver), and refractory metals. |
Advantages | Clean, efficient, precise temperature control, uniform mixing, rapid heating. |
Applications | Foundries, jewelry making, electronics, aerospace, and metal recycling. |
Comparison | More efficient and precise than cupolas, reverberatory, and electric arc furnaces. |
Learn how induction melting can optimize your metal processing—contact us today!