PVD (Physical Vapor Deposition) coating is a versatile and widely used method for applying thin, durable, and protective layers to various materials, primarily metals. However, applying PVD coatings to plastics presents unique challenges due to the thermal and chemical sensitivities of plastic substrates. While PVD is traditionally used on metals, advancements in technology and process modifications have made it possible to coat certain types of plastics under controlled conditions. The process involves vaporizing a source material in a high vacuum environment and depositing it onto the substrate. For plastics, lower temperatures and specialized techniques are required to prevent damage. Below, we explore the key considerations, challenges, and potential solutions for applying PVD coatings to plastics.
Key Points Explained:
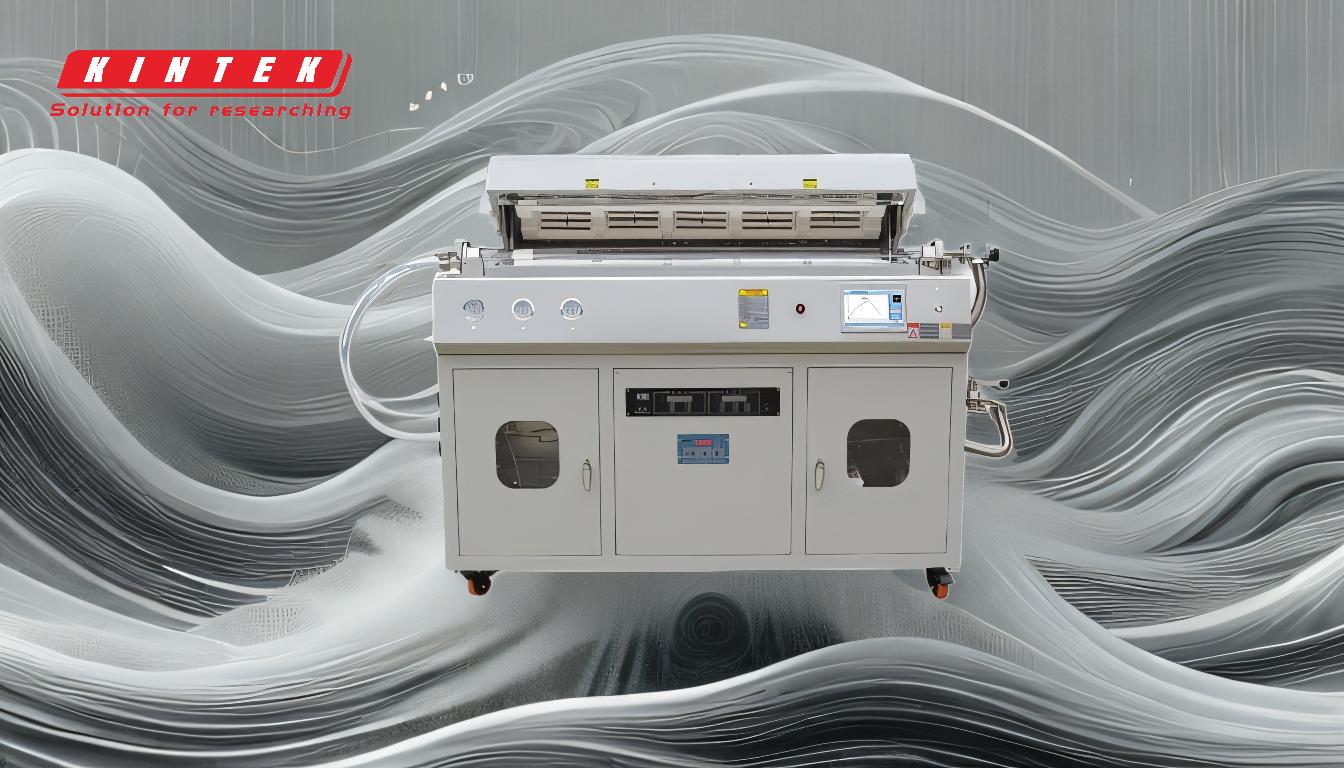
-
Understanding PVD Coating Process
- PVD coating involves vaporizing a source material (e.g., metals, ceramics) in a high vacuum chamber and depositing it onto a substrate.
- Common techniques include sputtering, thermal evaporation, and cathodic arc evaporation.
- The process typically operates at temperatures between 50°C and 500°C and requires a chemically inert atmosphere (e.g., Argon gas).
-
Challenges of Applying PVD to Plastics
- Thermal Sensitivity: Most plastics have low melting points and degrade at high temperatures, making them incompatible with traditional PVD processes.
- Adhesion Issues: Plastics often have smooth and non-reactive surfaces, which can make it difficult for the coating to adhere properly.
- Mechanical Stress: The vacuum environment and ion bombardment during PVD can cause mechanical stress or deformation in plastic substrates.
-
Solutions for PVD Coating on Plastics
- Low-Temperature PVD: Modifying the process to operate at lower temperatures (below 100°C) can prevent thermal damage to plastics.
- Surface Pretreatment: Techniques like plasma etching or chemical priming can improve adhesion by creating a rougher or more reactive surface.
- Specialized PVD Techniques: Sputtering is often preferred for plastics due to its lower energy requirements compared to other methods like cathodic arc evaporation.
-
Types of Plastics Suitable for PVD Coating
- Engineering Plastics: High-performance plastics like PEEK (Polyether Ether Ketone) and Ultem (Polyetherimide) are more heat-resistant and can withstand PVD conditions better than standard plastics.
- Thermoset Plastics: These materials are less prone to melting and may be more suitable for PVD coating.
-
Applications of PVD-Coated Plastics
- Automotive: Decorative trims and functional components benefit from the durability and aesthetic appeal of PVD coatings.
- Electronics: PVD coatings can provide electromagnetic shielding or improve surface conductivity on plastic components.
- Consumer Goods: Items like eyewear, watches, and smartphone cases can be enhanced with scratch-resistant and decorative PVD coatings.
-
Limitations of PVD on Plastics
- Complex Geometries: PVD struggles with coating deep or narrow holes, which is a common limitation regardless of the substrate material.
- Cost: The need for specialized equipment and processes can make PVD coating on plastics more expensive than traditional methods.
- Material Compatibility: Not all plastics are suitable for PVD, and extensive testing is often required to ensure compatibility.
-
Future Developments
- Research is ongoing to develop new PVD techniques and materials that are better suited for plastics.
- Innovations in surface pretreatment and low-temperature processes are expected to expand the range of plastics that can be coated using PVD.
In summary, while PVD coating is traditionally used on metals, it is possible to apply it to certain types of plastics with the right modifications and precautions. The key lies in addressing the thermal and adhesion challenges specific to plastic substrates. By using low-temperature processes, surface pretreatments, and specialized techniques, PVD coatings can be successfully applied to plastics for a variety of industrial and consumer applications. However, careful consideration of material compatibility and process limitations is essential to achieve optimal results.
Summary Table:
Aspect | Details |
---|---|
PVD Process | Vaporizes source material in a vacuum; techniques include sputtering, thermal evaporation. |
Challenges | Thermal sensitivity, adhesion issues, mechanical stress. |
Solutions | Low-temperature PVD, surface pretreatment, specialized techniques. |
Suitable Plastics | Engineering plastics (e.g., PEEK, Ultem), thermoset plastics. |
Applications | Automotive, electronics, consumer goods. |
Limitations | Complex geometries, higher costs, material compatibility. |
Future Developments | Innovations in low-temperature processes and surface pretreatment. |
Learn how PVD coatings can enhance your plastic components—contact our experts today!