PVD (Physical Vapor Deposition) coating can indeed be applied to plastic materials, making it a versatile solution for enhancing the durability, aesthetics, and functionality of plastic components. This process is particularly advantageous for plastics because it can be performed at relatively low temperatures, avoiding damage to the material. Commonly coated plastics include PVC, Nylon, ABS, Polycarbonate, and others. PVD coatings improve scratch resistance, corrosion resistance, and overall longevity, making them suitable for applications in harsh environments or industries like automotive, medical, and consumer electronics. However, challenges such as coating uniformity in complex geometries may require specialized techniques like mechanical rotation during the coating process.
Key Points Explained:
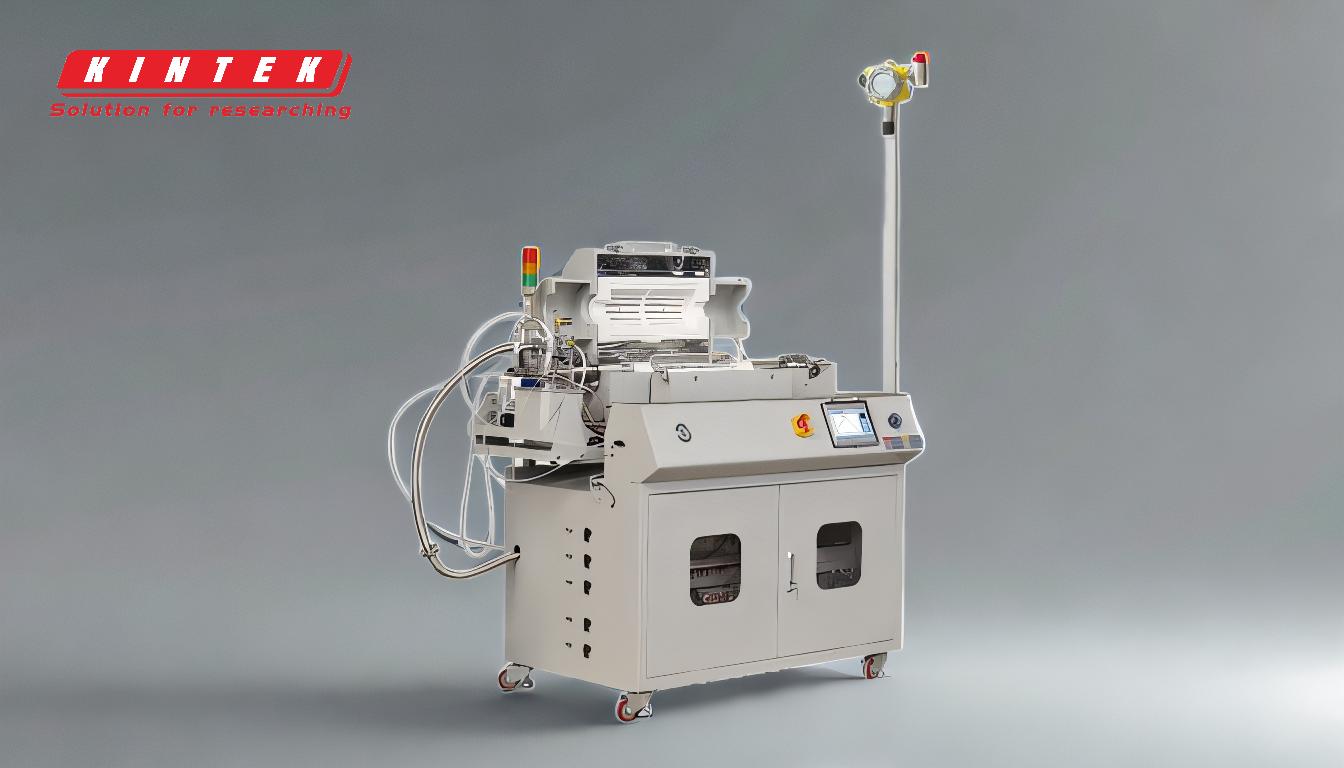
-
PVD Coating on Plastics is Feasible
- PVD coatings can be applied to a variety of plastic materials, including PVC, Nylon, ABS, Polycarbonate, and others.
- The process is compatible with plastics because it operates at low temperatures, often near room temperature, which prevents thermal degradation of the plastic substrate.
-
Advantages of PVD Coating for Plastics
- Enhanced Durability: PVD coatings are significantly harder than traditional coatings like chrome, providing superior scratch and wear resistance.
- Corrosion Resistance: The coatings protect plastic components from environmental factors, such as moisture and chemicals.
- Aesthetic Appeal: PVD coatings can create metallic finishes (e.g., gold, silver) or other decorative effects, enhancing the visual appeal of plastic parts.
- Longevity: The coatings are long-lasting, making them ideal for applications in harsh environments or near coastal areas.
-
Challenges in Coating Plastics with PVD
- Complex Geometries: Coating deep or narrow holes or ensuring uniform coverage on intricate shapes can be difficult. This is often addressed by rotating the parts on multiple axes during the coating process.
- Material Limitations: While many plastics are suitable, not all may adhere well to PVD coatings without proper surface preparation.
-
Applications of PVD-Coated Plastics
- Automotive Industry: Used for decorative trims, interior components, and functional parts requiring durability.
- Medical Devices: Coated plastics are used in surgical instruments, diagnostic equipment, and other medical tools where biocompatibility and durability are critical.
- Consumer Electronics: PVD coatings are applied to plastic casings for smartphones, laptops, and wearables to improve scratch resistance and aesthetic appeal.
- Industrial Components: Plastic parts exposed to harsh environments, such as gears or seals, benefit from PVD coatings.
-
Comparison with Other Materials
- While PVD coatings are commonly applied to metals like stainless steel, titanium, and copper alloys, plastics offer unique advantages such as lightweight and design flexibility.
- Unlike metals, plastics do not require high-temperature processing, making PVD coating more accessible for a broader range of applications.
-
Surface Preparation and Adhesion
- Proper surface preparation is crucial for ensuring strong adhesion of PVD coatings to plastic substrates. Techniques like plasma treatment or chemical priming may be used to enhance bonding.
- The choice of PVD material (e.g., titanium nitride, chromium nitride) depends on the desired properties and the specific plastic being coated.
-
Environmental and Cost Considerations
- PVD coating is an environmentally friendly process, as it does not involve hazardous chemicals or produce harmful byproducts.
- While the initial cost of PVD coating may be higher than traditional methods, the long-term benefits in terms of durability and reduced maintenance often justify the investment.
In summary, PVD coating is a highly effective method for enhancing the properties of plastic materials, offering a combination of durability, aesthetic appeal, and environmental benefits. While there are challenges in coating complex geometries, advancements in techniques and surface preparation have made PVD a viable option for a wide range of plastic applications.
Summary Table:
Aspect | Details |
---|---|
Feasibility | PVD coating can be applied to plastics like PVC, Nylon, ABS, and Polycarbonate. |
Advantages | Enhanced durability, corrosion resistance, aesthetic appeal, and longevity. |
Challenges | Complex geometries require specialized techniques; surface preparation is key. |
Applications | Automotive, medical devices, consumer electronics, and industrial components. |
Environmental Impact | Eco-friendly process with no hazardous chemicals or harmful byproducts. |
Ready to enhance your plastic components with PVD coating? Contact us today to learn more!