Yes, sintered metal can be machined. Sintered metal parts undergo various machining processes such as threading, boring, milling, drilling, turning, tapping, and broaching. Additionally, grinding processes like honing, lapping, and polishing are also applicable to sintered metal parts. These processes allow for precise shaping, finishing, and refinement of sintered metal components to meet specific design and functional requirements.
Key Points Explained:
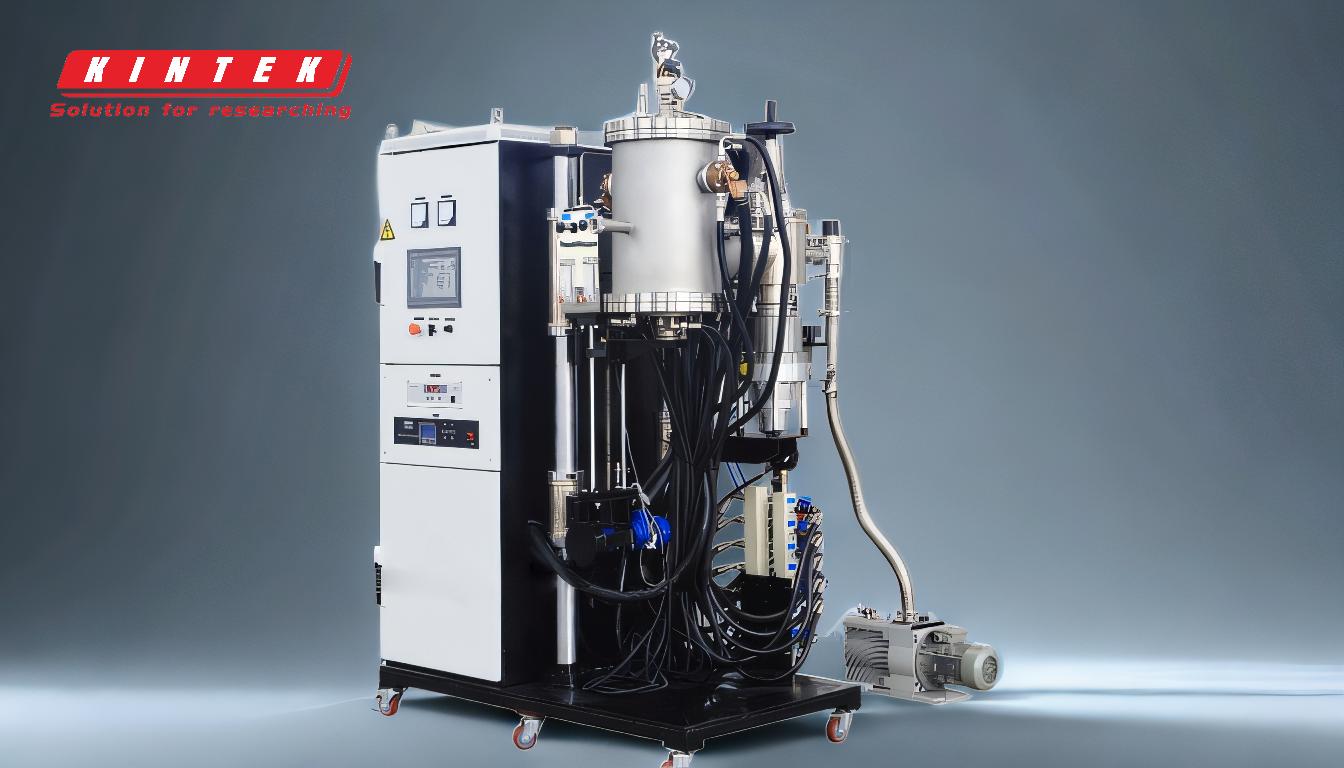
-
Machining Processes for Sintered Metal:
- Threading: This process involves cutting threads into the sintered metal part, which is essential for creating screw threads or other threaded features.
- Boring: Boring is used to enlarge or refine holes that have already been drilled or cast, ensuring precise dimensions and smooth surfaces.
- Milling: Milling is a versatile machining process that uses rotary cutters to remove material from the sintered metal part, creating complex shapes and features.
- Drilling: Drilling is the process of creating holes in the sintered metal part using a rotating drill bit.
- Turning: Turning involves rotating the sintered metal part while a cutting tool moves linearly to remove material, typically used to create cylindrical shapes.
- Tapping: Tapping is the process of cutting threads inside a hole, allowing for the insertion of screws or bolts.
- Broaching: Broaching is used to remove material in a linear motion, often to create keyways or other specific shapes.
-
Grinding Processes for Sintered Metal:
- Honing: Honing is a finishing process that uses abrasive stones to improve the surface finish and dimensional accuracy of holes in sintered metal parts.
- Lapping: Lapping involves using a loose abrasive to achieve a high degree of surface finish and flatness on sintered metal parts.
- Polishing: Polishing is used to enhance the surface finish of sintered metal parts, making them smoother and more reflective.
-
Materials Compatibility:
- Sintered metals are not the only materials that can be machined. Other materials such as quartz, ruby, glass, glass-ceramic, porous ceramics, composites, glass-filled resins, silica, carbon, machinable insulation materials, calcium silicate, mica, and aluminosilicate can also undergo similar machining processes. This indicates the versatility of machining techniques across a wide range of materials.
-
Importance of Machining Sintered Metal:
- Machining sintered metal parts is crucial for achieving the desired precision, surface finish, and functional characteristics. While sintering can produce near-net-shape parts, machining allows for the fine-tuning of dimensions and the creation of complex geometries that may not be achievable through sintering alone.
-
Considerations for Machining Sintered Metal:
- Tool Selection: The choice of cutting tools is critical when machining sintered metal. Tools must be durable and capable of withstanding the abrasive nature of sintered materials.
- Cooling and Lubrication: Proper cooling and lubrication are essential to prevent overheating and to extend the life of the cutting tools.
- Machining Parameters: Parameters such as cutting speed, feed rate, and depth of cut must be carefully controlled to achieve the desired results without damaging the sintered metal part.
In summary, sintered metal can indeed be machined using a variety of processes, including threading, boring, milling, drilling, turning, tapping, broaching, honing, lapping, and polishing. These processes are essential for achieving the precise dimensions, surface finishes, and functional characteristics required for sintered metal parts. Additionally, the compatibility of these machining processes with a wide range of materials highlights their versatility and importance in manufacturing.
Summary Table:
Process | Description |
---|---|
Threading | Cutting threads into sintered metal for screw threads or other features. |
Boring | Enlarging or refining holes for precise dimensions and smooth surfaces. |
Milling | Using rotary cutters to create complex shapes and features. |
Drilling | Creating holes with a rotating drill bit. |
Turning | Rotating the part while a cutting tool removes material for cylindrical shapes. |
Tapping | Cutting threads inside a hole for screws or bolts. |
Broaching | Removing material linearly to create keyways or specific shapes. |
Honing | Improving surface finish and dimensional accuracy of holes. |
Lapping | Achieving high surface finish and flatness with loose abrasives. |
Polishing | Enhancing surface finish for smoother, reflective surfaces. |
Need precision machining for sintered metal parts? Contact our experts today to get started!