Yes, steel can be PVD coated. The Physical Vapor Deposition (PVD) process is highly effective for coating steel, as it creates a thin, durable, and highly adherent layer that enhances the material's properties. PVD coatings are applied in a vacuum environment, where a solid material is vaporized and then deposited onto the steel surface atom by atom. This results in a uniform, high-quality coating that improves the steel's hardness, wear resistance, corrosion resistance, and aesthetic appeal. The process is environmentally friendly and suitable for a wide range of steel applications, including tools, automotive components, and decorative items.
Key Points Explained:
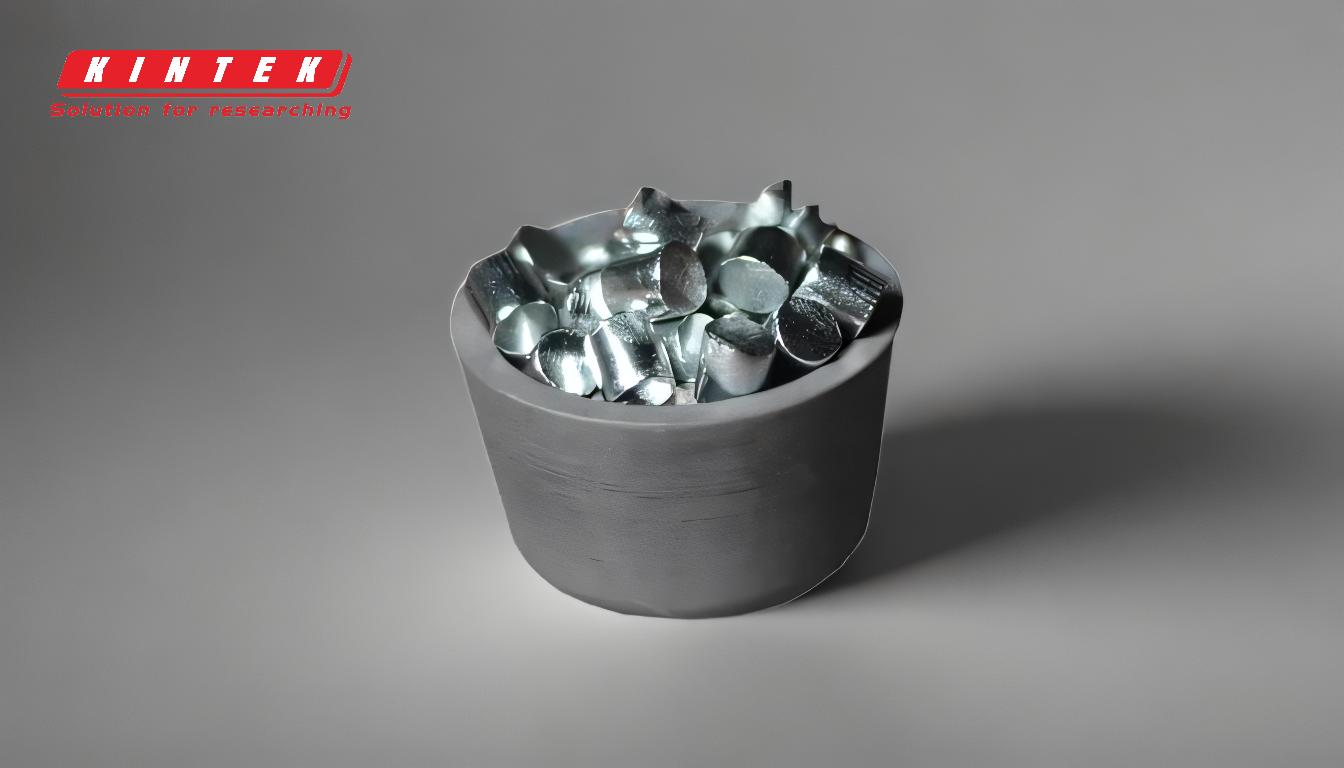
-
PVD Coating Process Overview:
- PVD coating involves vaporizing a solid material in a vacuum and depositing it onto a substrate (e.g., steel) in thin layers.
- The process consists of key steps: evaporation, transportation, reaction (optional), and deposition.
- It is carried out in a vacuum chamber at extremely low pressures (10^-3 to 10^-9 Torr) to ensure a clean and controlled environment.
-
Why Steel is Suitable for PVD Coating:
- Steel is an ideal substrate for PVD coating due to its smooth surface and ability to bond well with the vaporized material.
- The process enhances steel's surface properties, making it harder, more durable, and resistant to wear, corrosion, and oxidation.
- PVD coatings can also improve the aesthetic appeal of steel, providing a variety of colors and finishes.
-
Steps to PVD Coat Steel:
- Preparation: The steel substrate is cleaned and placed in the vacuum chamber to remove contaminants.
- Evaporation: A high-energy source (e.g., electron beam or ion bombardment) vaporizes the target material (e.g., titanium, chromium, or aluminum).
- Transportation: The vaporized atoms travel through the vacuum and reach the steel surface.
- Reaction (Optional): Reactive gases (e.g., nitrogen or oxygen) can be introduced to form compounds like metal nitrides or oxides.
- Deposition: The vaporized material condenses on the steel surface, forming a thin, uniform, and highly adherent coating.
-
Benefits of PVD Coating on Steel:
- Enhanced Durability: The coating increases surface hardness, making the steel more resistant to scratches, abrasion, and wear.
- Corrosion Resistance: PVD coatings provide a barrier against environmental factors, protecting the steel from rust and degradation.
- Aesthetic Versatility: PVD coatings can produce a range of colors and finishes, such as gold, black, or bronze, enhancing the steel's appearance.
- Environmental Friendliness: The process uses fewer harmful chemicals compared to traditional coating methods, making it more sustainable.
-
Applications of PVD-Coated Steel:
- Tools and Machinery: PVD-coated steel is used in cutting tools, molds, and industrial equipment to improve performance and longevity.
- Automotive Industry: Components like engine parts, decorative trim, and fasteners benefit from PVD coatings due to their durability and corrosion resistance.
- Decorative Items: PVD-coated steel is popular in jewelry, watches, and architectural elements for its aesthetic appeal and durability.
- Medical Devices: Surgical instruments and implants use PVD coatings for biocompatibility and resistance to wear.
-
Considerations for PVD Coating Steel:
- Surface Preparation: Proper cleaning and polishing of the steel surface are critical to ensure strong adhesion and a high-quality coating.
- Coating Thickness: PVD coatings are typically thin (microns thick), so the application must be precise to achieve the desired properties.
- Material Compatibility: The choice of target material (e.g., titanium, chromium) and reactive gases (e.g., nitrogen) depends on the desired coating properties and application requirements.
In summary, PVD coating is a highly effective method for enhancing the properties of steel. It provides a durable, corrosion-resistant, and aesthetically pleasing surface that is suitable for a wide range of applications. The process is precise, environmentally friendly, and capable of producing coatings with exceptional performance characteristics.
Summary Table:
Aspect | Details |
---|---|
Process | Vaporization and deposition in a vacuum environment. |
Key Benefits | Enhanced hardness, wear resistance, corrosion resistance, and aesthetics. |
Applications | Tools, automotive components, decorative items, medical devices. |
Environmental Impact | Fewer harmful chemicals, sustainable process. |
Coating Thickness | Thin, precise layers (microns thick). |
Surface Preparation | Critical for strong adhesion and high-quality coating. |
Transform your steel with PVD coating—contact our experts today to learn more!