Yes, PVD (Physical Vapor Deposition) coating can be applied to aluminum. PVD is a versatile coating technique that deposits thin films of material onto a substrate, such as aluminum, to enhance its properties like durability, corrosion resistance, and aesthetic appeal. Aluminum is a lightweight and widely used material, and PVD coatings can significantly improve its performance in various applications, including automotive, aerospace, and consumer electronics. The process involves vaporizing the coating material in a vacuum environment and depositing it onto the aluminum surface, resulting in a strong, durable, and visually appealing finish.
Key Points Explained:
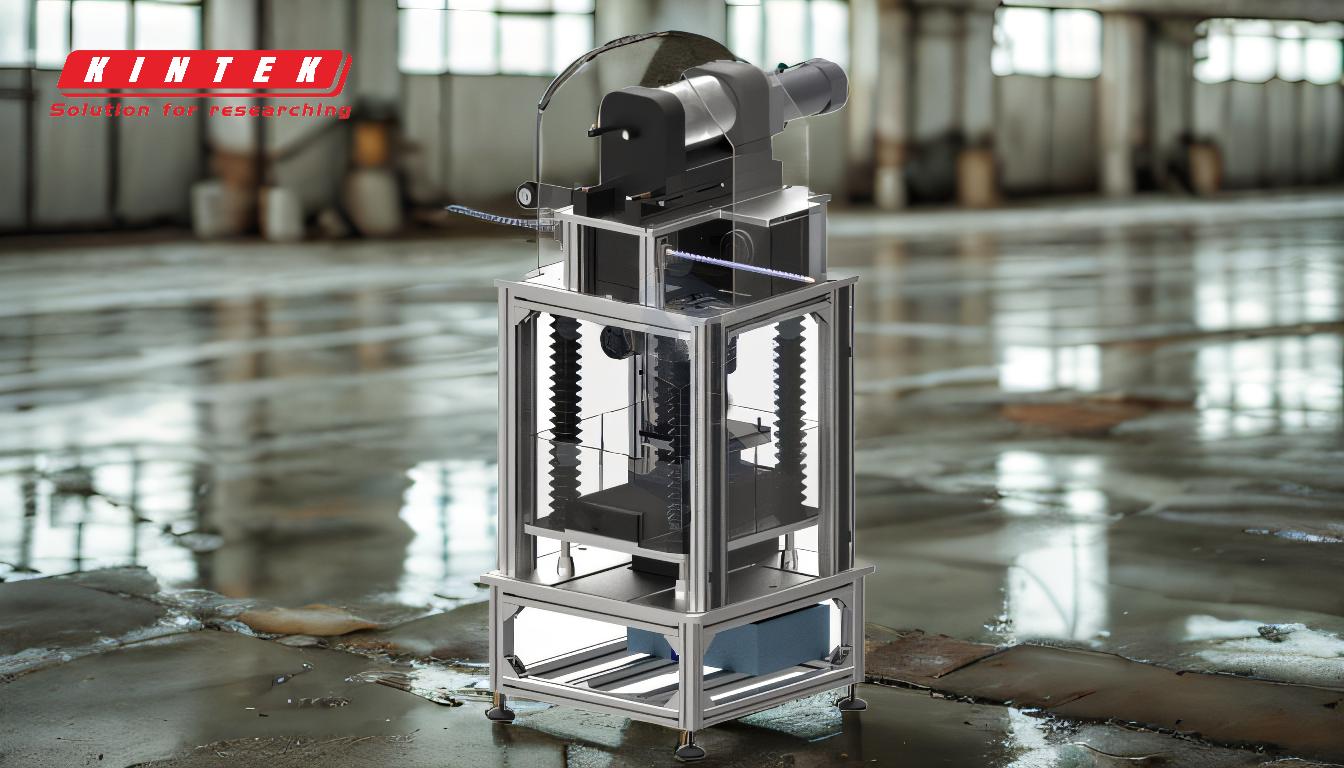
-
PVD Coating Process on Aluminum:
- PVD coating involves vaporizing a solid material in a vacuum chamber and depositing it onto the aluminum substrate. This process creates a thin, uniform layer that adheres strongly to the surface.
- Aluminum is an excellent candidate for PVD coating due to its lightweight nature and widespread use in industries requiring enhanced surface properties.
-
Benefits of PVD Coating on Aluminum:
- Durability: PVD coatings improve the hardness and wear resistance of aluminum, making it suitable for high-stress applications.
- Corrosion Resistance: The coating acts as a barrier, protecting aluminum from environmental factors like moisture and chemicals.
- Aesthetic Appeal: PVD coatings can provide a variety of finishes, including metallic, matte, or glossy, enhancing the visual appeal of aluminum products.
-
Key Considerations for PVD Coating on Aluminum:
- Coat Thickness: Thicker coatings generally offer better durability but may require more precise control during the deposition process.
- Finish Type: Matte finishes are less durable but wear off more slowly, while metallic finishes enhance appearance but may require more maintenance.
- Color Options: PVD coatings can produce a wide range of colors, allowing for customization to meet specific design requirements.
-
Applications of PVD-Coated Aluminum:
- Automotive Industry: Used for decorative trims, engine components, and lightweight structural parts.
- Aerospace: Enhances the performance of aluminum components in aircraft by improving wear and corrosion resistance.
- Consumer Electronics: Provides a durable and attractive finish for aluminum casings in devices like smartphones and laptops.
-
Advantages of PVD Coating Machines:
- Computer-Controlled Precision: Modern PVD coating machines are computer-controlled, ensuring consistent and high-quality results.
- Cost Efficiency: These machines reduce production costs and turnaround time, making them suitable for both large-scale manufacturing and small batch production.
By leveraging PVD coating technology, aluminum can be transformed into a more robust, durable, and visually appealing material, suitable for a wide range of industrial and consumer applications.
Summary Table:
Aspect | Details |
---|---|
PVD Coating Process | Vaporizes material in a vacuum, depositing a thin, uniform layer on aluminum. |
Benefits | - Durability: Enhances hardness and wear resistance. |
- Corrosion Resistance: Protects against moisture and chemicals. | |
- Aesthetic Appeal: Offers metallic, matte, or glossy finishes. | |
Key Considerations | - Coat Thickness: Thicker coatings improve durability. |
- Finish Type: Matte for slow wear, metallic for enhanced appearance. | |
- Color Options: Wide range available for customization. | |
Applications | Automotive, aerospace, and consumer electronics. |
Advantages of Machines | - Computer-controlled precision. |
- Cost-efficient for large-scale and small batch production. |
Transform your aluminum products with PVD coating—contact us today to learn more!