Determining the temperature of a vacuum, particularly in the context of a vacuum cleaning furnace, involves understanding the mechanisms of temperature control, measurement, and uniformity within the furnace. Vacuum furnaces are designed to operate under controlled conditions, where temperature is a critical parameter. The temperature in a vacuum furnace is measured using thermocouples and regulated by advanced control systems such as PID controllers, touch screens, or PLC systems. Temperature uniformity is essential for consistent results, and modern furnaces are equipped with multiple temperature recorders to monitor and ensure even heating. Additionally, the temperature can be adjusted and maintained at a constant level, with improvements in heating speed and uniformity achieved through gas circulation and advanced control systems. Failures in temperature control are typically addressed by repairing or replacing faulty components like thermocouples or control instruments.
Key Points Explained:
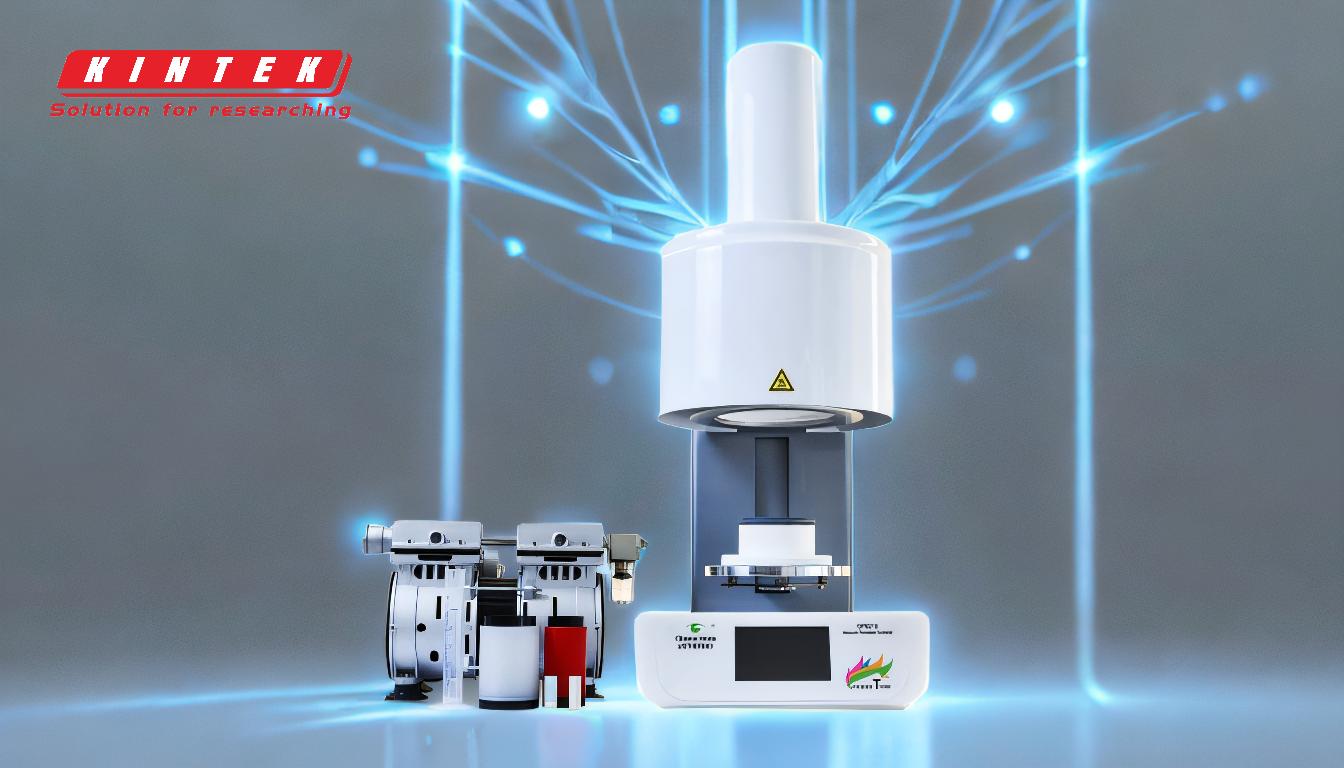
-
Temperature Measurement and Control in Vacuum Furnaces:
- Vacuum furnaces use thermocouples to measure temperature and advanced control systems like PID controllers, touch screens, or PLC systems to regulate it. These systems ensure precise temperature management, which is crucial for processes such as annealing, sintering, or brazing. For example, a vacuum cleaning furnace might employ a PID programmable controller to maintain consistent temperatures during operation.
-
Temperature Uniformity and Its Importance:
- Temperature uniformity refers to the consistency of temperature across the furnace's operating range. This is particularly important in lower temperature ranges, where even slight variations can affect the outcome of processes. Standards such as AMS 2750D specify acceptable uniformity ranges, such as +/- 20°F at 300-600°F, +/- 15°F at 600-900°F, and +/- 10°F at 900-2500°F. Achieving uniformity ensures that all parts of the workpiece are heated evenly, preventing defects.
-
Multiple Temperature Recorders for Monitoring:
- Modern vacuum furnaces, such as vacuum annealing furnaces, are equipped with multiple temperature recorders to monitor the working conditions of the furnace. For instance, six temperature recorders might simultaneously track the temperature in six different control areas. This setup helps avoid large deformations in the vacuum tank caused by uneven heating.
-
Adjustable and Maintainable Temperature:
- The temperature in a vacuum furnace is adjustable and can be maintained at a constant level for extended periods. This capability is essential for processes that require precise thermal conditions, such as sintering or heat treatment. For example, a vacuum hot press furnace can maintain a specific temperature for the duration of a sintering cycle.
-
Improving Heating Speed and Uniformity:
- The heating speed and temperature uniformity in a vacuum furnace can be enhanced by introducing inert gases or hydrogen during the early stages of sintering. Additionally, using circulating gas cooling methods can improve cooling rates. Pre-burning briquettes before vacuum sintering helps exclude forming agents, preventing contamination of the vacuum system.
-
Addressing Temperature Control Failures:
- Temperature control failures in vacuum furnaces are often caused by issues such as disconnected or short-circuited thermocouple wires or faulty temperature control instruments. These problems can be resolved by replacing or reconnecting the thermocouple and repairing the control system, ensuring accurate temperature regulation.
-
Advanced Control Systems for Better Uniformity:
- Upgrading the control and heating systems in a vacuum furnace can significantly improve temperature uniformity. For example, replacing a single SCR with independent SCRs for each VRT and using advanced controllers like the SSi 9220 can reduce temperature spread and center the load TC delta around the set point. This approach ensures better scaling of outputs at specified temperatures.
-
Maximum Temperature Capability:
- Vacuum furnaces typically have a maximum temperature capability of up to 2400°F, with some models capable of reaching 2650°F. These higher temperatures are essential for clean-up cycles and specific processes that require elevated thermal conditions.
By understanding these key points, one can effectively determine and control the temperature in a vacuum furnace, ensuring optimal performance and consistent results in various industrial applications.
Summary Table:
Key Aspect | Details |
---|---|
Temperature Measurement | Thermocouples and advanced control systems (PID, touch screens, PLC). |
Temperature Uniformity | Critical for consistent results; standards like AMS 2750D specify ranges. |
Multiple Temperature Recorders | Monitor heating conditions in multiple areas to prevent uneven heating. |
Adjustable Temperature | Maintain constant temperatures for precise processes like sintering. |
Heating Speed & Uniformity | Improved via gas circulation and advanced control systems. |
Max Temperature Capability | Up to 2400°F (2650°F for some models). |
Need precise temperature control for your vacuum furnace? Contact our experts today to learn more!