Yes, you can apply PVD (Physical Vapor Deposition) coatings to stainless steel. PVD coatings are widely used to enhance the properties of stainless steel, including its resistance to corrosion, staining, and wear, as well as improving its aesthetic appearance. The process involves vaporizing a solid material in a vacuum environment and depositing it onto the stainless steel surface, creating a thin, durable, and highly adherent layer. This coating not only improves the functional properties of stainless steel but also allows for a variety of finishes, making it suitable for both industrial and decorative applications.
Key Points Explained:
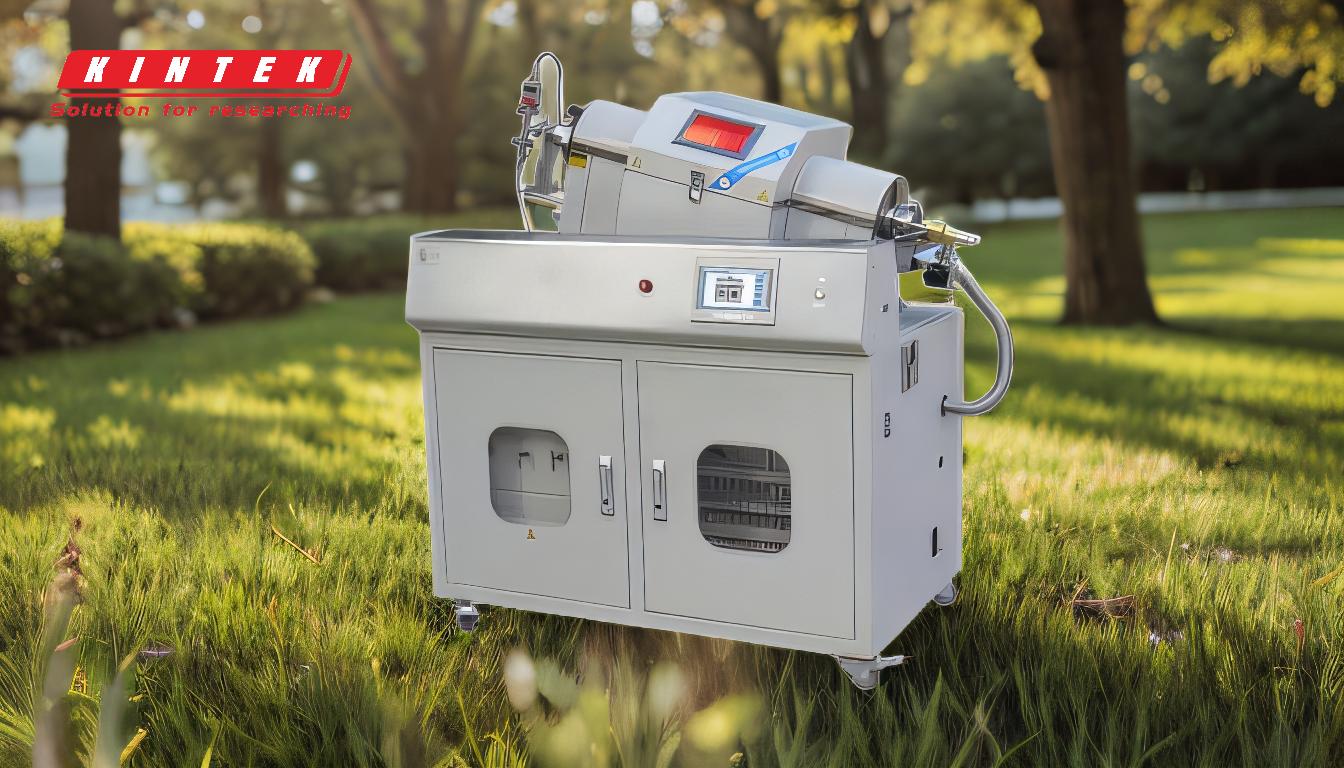
-
Improvement in Stainless Steel Properties:
- Corrosion and Staining Resistance: PVD coatings significantly enhance the resistance of stainless steel to corrosion and staining. This is particularly beneficial in environments where the material is exposed to harsh chemicals or moisture.
- Durability: The coating increases the surface hardness of stainless steel, making it more resistant to wear and tear. This extends the lifespan of the material, especially in high-use applications.
- Aesthetic Appeal: PVD coatings can be applied in various colors and finishes, improving the visual appearance of stainless steel components. This is useful in applications where both functionality and aesthetics are important, such as in architectural elements or consumer products.
-
Types of PVD Coating Processes:
- Cathodic Arc Deposition: This method uses an electric arc to vaporize the coating material, which is then deposited onto the stainless steel surface. It is known for producing high-quality, dense coatings.
- Electron Beam Physical Vapor Deposition (EB-PVD): In this process, an electron beam is used to heat and vaporize the coating material. It is particularly effective for creating uniform coatings over complex geometries.
- Thermal Evaporation Deposition: This technique involves heating the coating material until it evaporates, then condensing it onto the stainless steel surface. It is suitable for creating thin, uniform coatings.
- Sputter Deposition: This method uses a plasma to dislodge atoms from the target material, which are then deposited onto the substrate. It is widely used for its ability to produce highly adherent and uniform coatings.
- Pulsed Laser Deposition (PLD): A high-power laser is used to ablate the coating material, which is then deposited onto the stainless steel. This method is known for its precision and ability to create complex coatings.
-
Advantages of PVD Coating on Stainless Steel:
- Excellent Adhesion: PVD coatings bond strongly to the stainless steel surface due to high levels of metal ionization during the deposition process. This ensures long-lasting performance.
- Thin and Uniform Coatings: PVD coatings are extremely thin, often only a few micrometers thick, yet they provide robust protection without altering the underlying material's properties.
- Replicability of Finish: PVD coatings can replicate the original finish of stainless steel with minimal effort, making it easy to achieve consistent results across multiple components.
- Environmental Benefits: PVD coating is an environmentally friendly process that does not affect the recyclability of stainless steel, which is already a 100% recyclable material.
-
Functional Enhancements:
- Hardness: PVD coatings increase the surface hardness of stainless steel, making it more resistant to scratches and abrasions.
- Friction Reduction: The smoothness of PVD coatings reduces friction, which is beneficial in applications involving moving parts.
- Extended Lifespan: By improving resistance to wear, corrosion, and other forms of degradation, PVD coatings extend the useful life of stainless steel components.
- Essential for Functionality: In some cases, PVD coatings are critical to the functionality of the part, such as in medical devices or precision instruments where surface properties are crucial.
-
Applications of PVD-Coated Stainless Steel:
- Industrial Components: PVD-coated stainless steel is used in machinery, tools, and equipment where durability and resistance to wear are essential.
- Architectural and Decorative Uses: The aesthetic versatility of PVD coatings makes them ideal for architectural elements, such as facades, railings, and fixtures, as well as decorative items like jewelry and watches.
- Medical Devices: The biocompatibility and corrosion resistance of PVD-coated stainless steel make it suitable for medical implants and surgical instruments.
- Consumer Electronics: PVD coatings are used in electronic devices to improve durability and provide a premium finish.
In conclusion, PVD coating is a highly effective method for enhancing the properties of stainless steel. It offers a range of benefits, from improved durability and corrosion resistance to aesthetic versatility, making it suitable for a wide variety of applications. The process is environmentally friendly and does not compromise the recyclability of stainless steel, further adding to its appeal.
Summary Table:
Aspect | Details |
---|---|
Improved Properties | Corrosion resistance, durability, and aesthetic appeal. |
PVD Coating Processes | Cathodic Arc, EB-PVD, Thermal Evaporation, Sputter Deposition, PLD. |
Advantages | Excellent adhesion, thin/durable coatings, replicable finishes, eco-friendly. |
Functional Enhancements | Increased hardness, reduced friction, extended lifespan, critical functionality. |
Applications | Industrial, architectural, medical devices, consumer electronics. |
Unlock the full potential of stainless steel with PVD coatings—contact us today to learn more!