Re-coating a PVD (Physical Vapor Deposition) watch is technically possible, but it is a complex and costly process, especially for assembled watches or bracelets. The PVD coating process involves evaporating a coating material in a vacuum chamber and depositing it onto the watch's surface at a molecular or atomic level, creating a durable layer. While it is more cost-effective to apply PVD coatings to batches of new components before assembly, re-coating an already assembled watch or bracelet is challenging and expensive due to the intricate disassembly, preparation, and reapplication required. Below, we explore the key considerations and steps involved in re-coating a PVD watch.
Key Points Explained:
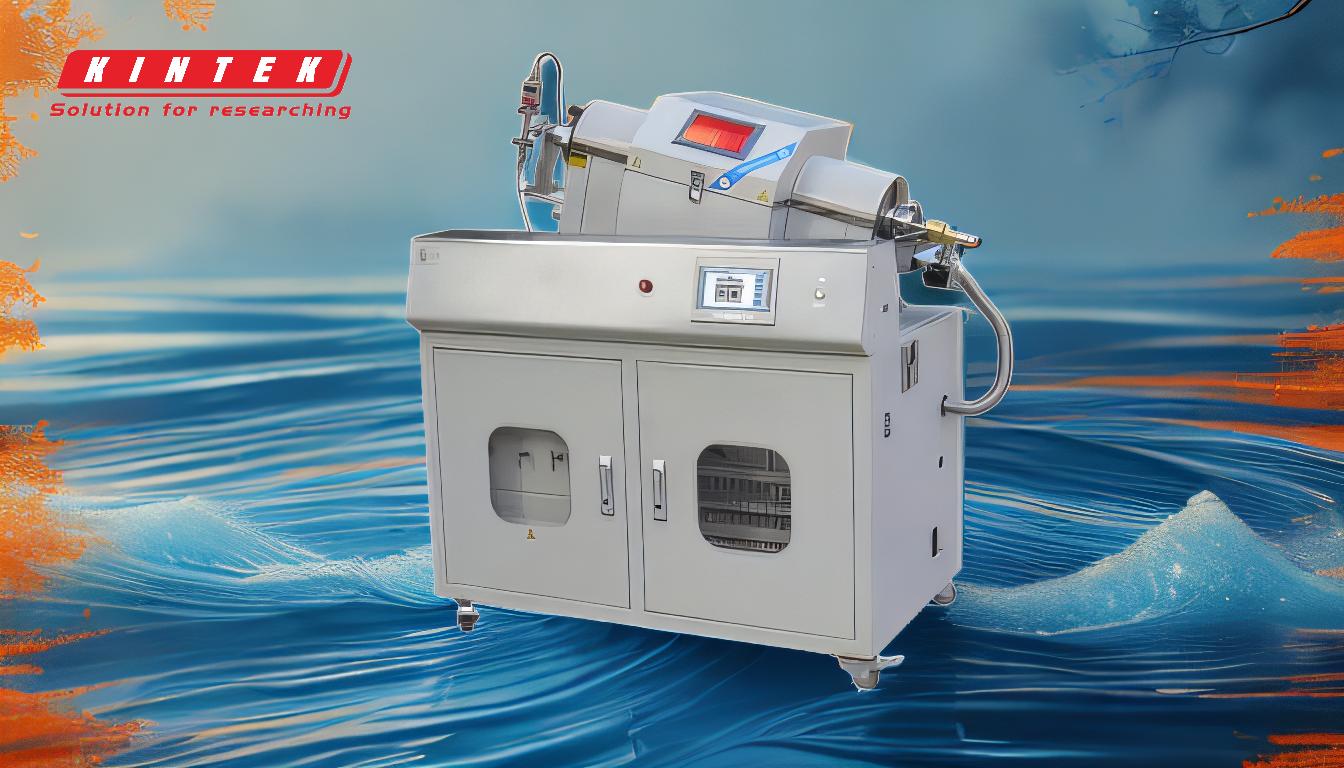
-
Understanding the PVD Coating Process
- PVD coating involves evaporating a material (e.g., titanium nitride, zirconium nitride, or DLC) in a vacuum chamber and depositing it onto the watch's surface.
- The coating bonds at a molecular or atomic level, creating a thin, durable, and scratch-resistant layer.
- This process is typically done on individual components before assembly to ensure even coverage and avoid damage to delicate parts like movements or seals.
-
Challenges of Re-coating an Assembled Watch
- Disassembly Required: To re-coat an assembled watch, it must be completely disassembled to remove the movement, crystal, and other non-metal components that cannot withstand the high temperatures and vacuum conditions of the PVD process.
- Surface Preparation: The existing PVD coating must be removed, and the surface must be meticulously cleaned and polished to ensure proper adhesion of the new coating.
- Risk of Damage: Disassembling and reassembling a watch, especially luxury or complex models, carries a risk of damaging delicate components or compromising water resistance.
-
Cost Implications
- Re-coating a PVD watch is significantly more expensive than applying the coating to new components.
- The labor-intensive process of disassembly, surface preparation, and reassembly adds to the cost.
- Bracelets, in particular, are challenging to re-coat due to their intricate links and multiple moving parts, making the process even more expensive.
-
When Re-coating Makes Sense
- Sentimental Value: If the watch holds significant sentimental or historical value, re-coating may be justified despite the cost.
- High-End Watches: For luxury or high-end watches, re-coating can restore the watch's appearance and protect its value.
- Limited Availability: If the watch model is rare or discontinued, re-coating may be the only option to maintain its original look.
-
Alternatives to Re-coating
- Touch-Up Kits: Some companies offer touch-up kits for minor scratches or wear on PVD coatings, though these are temporary solutions and may not match the original finish perfectly.
- Replacement Parts: For watches with modular designs, replacing the PVD-coated components (e.g., bezel, case, or bracelet) may be more cost-effective than re-coating.
- Customization: Some owners opt for a different finish (e.g., brushed, polished, or a different PVD color) during the re-coating process to give the watch a unique look.
-
Finding a Qualified Service Provider
- Re-coating a PVD watch requires specialized equipment and expertise.
- Look for reputable watchmakers or coating specialists with experience in PVD processes and luxury watch servicing.
- Ensure the service provider offers warranties or guarantees for their work to protect against potential issues.
-
Preventative Measures to Extend PVD Coating Life
- Avoid exposing the watch to harsh chemicals, abrasive surfaces, or extreme impacts.
- Regularly clean the watch with a soft cloth to remove dirt and oils that can degrade the coating over time.
- Store the watch in a protective case or pouch when not in use to minimize scratches and wear.
In conclusion, while re-coating a PVD watch is possible, it is a costly and labor-intensive process that requires careful consideration. For most watch owners, the decision to re-coat will depend on the watch's value, sentimental significance, and the availability of alternative solutions. If re-coating is pursued, it is essential to work with a qualified professional to ensure the best results and preserve the watch's integrity.
Summary Table:
Aspect | Details |
---|---|
PVD Coating Process | Evaporates material in a vacuum, creating a durable, scratch-resistant layer. |
Challenges | Disassembly, surface prep, and risk of damage to delicate components. |
Cost Implications | Expensive due to labor-intensive disassembly, prep, and reassembly. |
When to Re-coat | Sentimental value, high-end watches, or rare/discontinued models. |
Alternatives | Touch-up kits, replacement parts, or customization options. |
Finding a Provider | Look for experienced professionals with warranties for PVD re-coating. |
Preventative Measures | Avoid harsh chemicals, clean regularly, and store in protective cases. |
Need help restoring your PVD watch? Contact our experts today for a consultation!