Activated charcoal, also known as activated carbon, is widely used for adsorption of contaminants in various applications such as water purification, air filtration, and industrial processes. Over time, the adsorption capacity of activated charcoal diminishes as it becomes saturated with contaminants. However, instead of disposing of the spent charcoal, it can often be regenerated to restore its adsorption properties. Regeneration involves removing the adsorbed contaminants from the charcoal, allowing it to be reused. This process is not only cost-effective but also environmentally friendly, as it reduces waste. Below, we explore the key aspects of regenerating activated charcoal, including the methods, benefits, and limitations.
Key Points Explained:
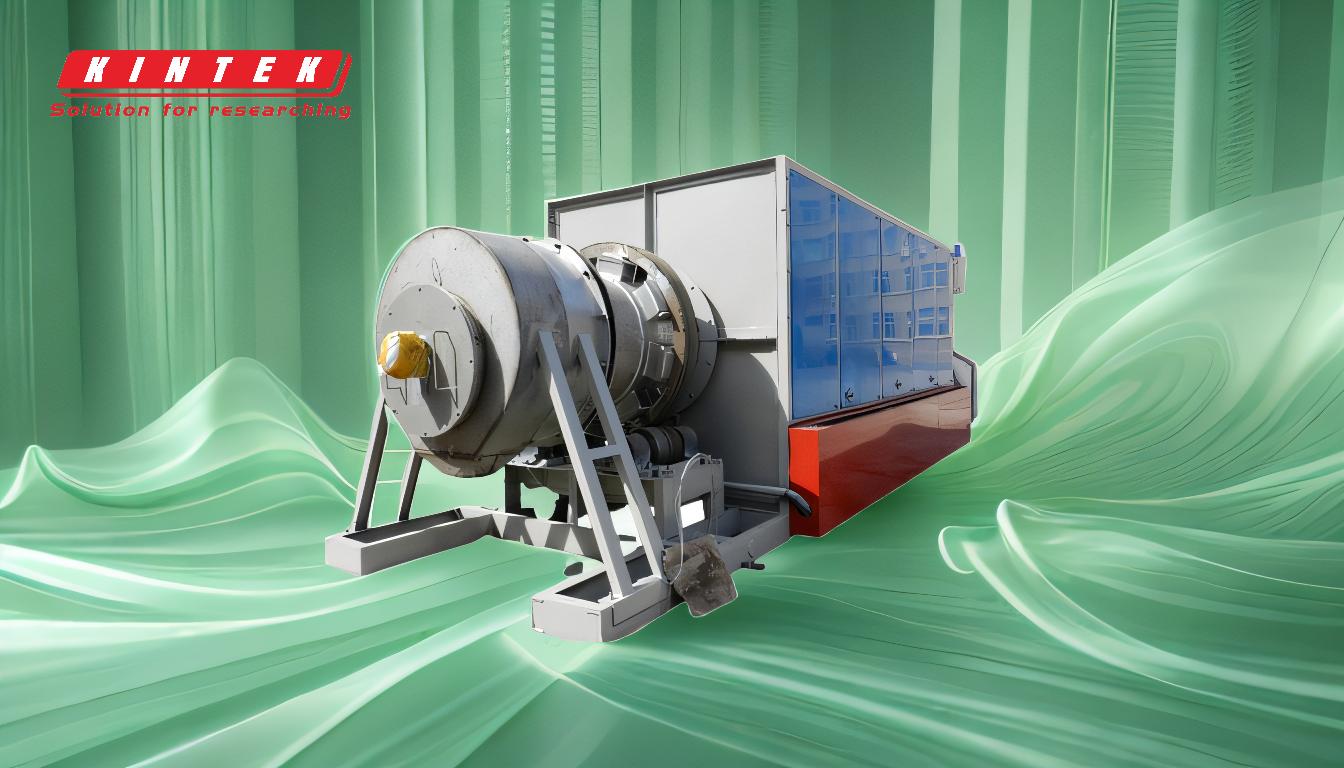
-
What is Activated Charcoal Regeneration?
- Regeneration is the process of restoring the adsorption capacity of spent activated charcoal by removing the adsorbed contaminants.
- This process allows the charcoal to be reused, extending its lifespan and reducing the need for disposal.
-
Methods of Regeneration:
-
Thermal Regeneration:
- This is the most common method, involving heating the spent charcoal in a controlled environment (e.g., a rotary kiln or furnace) at high temperatures (typically 600–900°C).
- The heat drives off the adsorbed contaminants, leaving the charcoal clean and ready for reuse.
-
Chemical Regeneration:
- In this method, chemicals are used to desorb contaminants from the charcoal. For example, acids or bases may be applied to dissolve specific contaminants.
- This method is less common and is typically used for specific applications where thermal regeneration is not suitable.
-
Steam Regeneration:
- Steam is passed through the spent charcoal at high temperatures to desorb contaminants. This method is often used in smaller-scale applications.
-
Biological Regeneration:
- Microorganisms are used to break down organic contaminants adsorbed on the charcoal. This method is still in the experimental stage and is not widely used.
-
Thermal Regeneration:
-
Benefits of Regeneration:
-
Cost Savings:
- Regenerating activated charcoal is often more cost-effective than purchasing new charcoal, especially for large-scale industrial applications.
-
Environmental Benefits:
- By regenerating and reusing charcoal, the amount of waste sent to landfills or incinerators is reduced, minimizing environmental impact.
-
Resource Efficiency:
- Regeneration conserves raw materials and energy that would otherwise be required to produce new activated charcoal.
-
Cost Savings:
-
Limitations of Regeneration:
-
Loss of Adsorption Capacity:
- Each regeneration cycle may slightly reduce the adsorption capacity of the charcoal, meaning it may not perform as well as new charcoal after multiple regenerations.
-
Contaminant-Specific Limitations:
- Some contaminants, particularly heavy metals, may not be fully removed during regeneration, limiting the effectiveness of the process.
-
Energy Requirements:
- Thermal regeneration, in particular, requires significant energy input, which can offset some of the environmental and cost benefits.
-
Loss of Adsorption Capacity:
-
Applications of Regenerated Activated Charcoal:
- Regenerated charcoal can be reused in the same applications as new charcoal, including:
- Water treatment (e.g., removing organic compounds, chlorine, and odors).
- Air purification (e.g., capturing volatile organic compounds or VOCs).
- Industrial processes (e.g., solvent recovery, gold extraction).
- Regenerated charcoal can be reused in the same applications as new charcoal, including:
-
Considerations for Purchasers:
-
Regeneration Frequency:
- Determine how often the charcoal can be regenerated before its performance degrades significantly.
-
Regeneration Costs:
- Compare the costs of regeneration versus purchasing new charcoal, including transportation and processing fees.
-
Environmental Impact:
- Evaluate the environmental benefits of regeneration, such as reduced waste and resource conservation.
-
Quality Assurance:
- Ensure that the regenerated charcoal meets the required performance standards for your specific application.
-
Regeneration Frequency:
In conclusion, regenerating activated charcoal is a viable and sustainable option for extending its usability. By understanding the methods, benefits, and limitations of regeneration, purchasers can make informed decisions that balance cost, performance, and environmental impact.
Summary Table:
Aspect | Details |
---|---|
Methods | Thermal, Chemical, Steam, Biological |
Benefits | Cost savings, environmental benefits, resource efficiency |
Limitations | Reduced adsorption capacity, contaminant-specific issues, energy-intensive |
Applications | Water treatment, air purification, industrial processes |
Considerations | Regeneration frequency, costs, environmental impact, quality assurance |
Interested in regenerating activated charcoal for your needs? Contact our experts today to learn more!