PVD (Physical Vapor Deposition) coatings are highly durable and do not fall off on their own due to their hardness and strong adhesion to the substrate. These coatings are created through a vacuum-based process where a solid material is vaporized and deposited onto a target surface, forming a thin, hard layer. While PVD coatings are resistant to scratching and wear, they can be removed using specific techniques, such as mechanical abrasion, chemical stripping, or thermal methods. However, removing PVD coatings requires careful consideration of the substrate material and the potential impact on its integrity.
Key Points Explained:
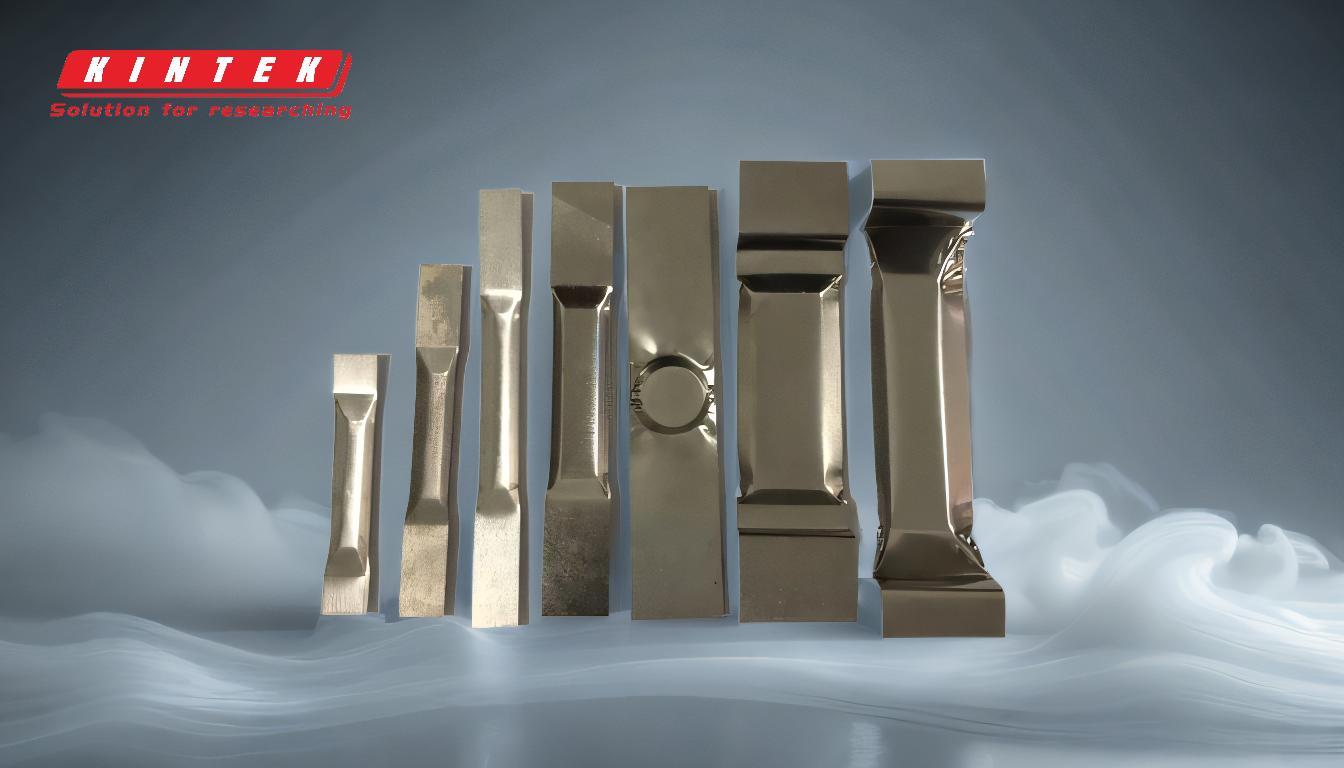
-
Durability and Adhesion of PVD Coatings
- PVD coatings are known for their exceptional hardness, often compared to diamonds, making them resistant to scratches and wear.
- The coating process involves vaporizing a solid material in a vacuum chamber and depositing it onto the target material, ensuring strong adhesion.
- Due to their robust nature, PVD coatings do not naturally degrade or fall off over time.
-
Challenges in Removing PVD Coatings
- The hardness and strong bond of PVD coatings make them difficult to remove without specialized methods.
- Improper removal techniques can damage the underlying substrate, so caution is required.
-
Methods for Removing PVD Coatings
- Mechanical Abrasion: This involves using abrasive tools or techniques, such as sandblasting or grinding, to physically remove the coating. However, this method risks damaging the substrate if not done carefully.
- Chemical Stripping: Certain chemical solutions can dissolve or weaken the PVD coating, allowing it to be removed. This method requires selecting chemicals that do not harm the substrate.
- Thermal Methods: High temperatures can sometimes be used to break down the coating, but this depends on the thermal stability of both the coating and the substrate.
-
Considerations for Coating Removal
- The substrate material must be evaluated to ensure it can withstand the chosen removal method.
- The intended use of the substrate after coating removal should be considered to avoid compromising its functionality.
- Professional expertise is often recommended to ensure the process is carried out safely and effectively.
-
Applications and Implications
- In industries where PVD coatings are used, such as aerospace, automotive, and medical devices, removing coatings may be necessary for rework or recycling purposes.
- Understanding the removal process is crucial for maintaining the quality and longevity of coated components.
In summary, while PVD coatings are highly durable and resistant to wear, they can be removed using specialized techniques. However, the process requires careful planning and execution to avoid damaging the substrate.
Summary Table:
Aspect | Details |
---|---|
Durability | PVD coatings are highly durable, resistant to scratches, and do not degrade. |
Removal Methods | Mechanical abrasion, chemical stripping, or thermal methods. |
Challenges | Risk of substrate damage; requires careful execution. |
Applications | Aerospace, automotive, and medical industries. |
Expert Recommendation | Professional expertise is advised for safe and effective removal. |
Need help removing PVD coatings? Contact our experts today for professional guidance!