PVD (Physical Vapor Deposition) coatings are renowned for their durability, hardness, and resistance to wear, corrosion, and high temperatures. However, repairing a PVD coating is not straightforward due to its thinness (0.5–5 microns) and strong adhesion to the substrate. While minor surface scratches or wear can sometimes be polished out, significant damage typically requires recoating. Recoating involves stripping the damaged layer and reapplying the PVD coating, which is a complex process requiring specialized equipment and expertise. In most cases, repairing PVD coatings is impractical, and recoating or replacement is the recommended solution.
Key Points Explained:
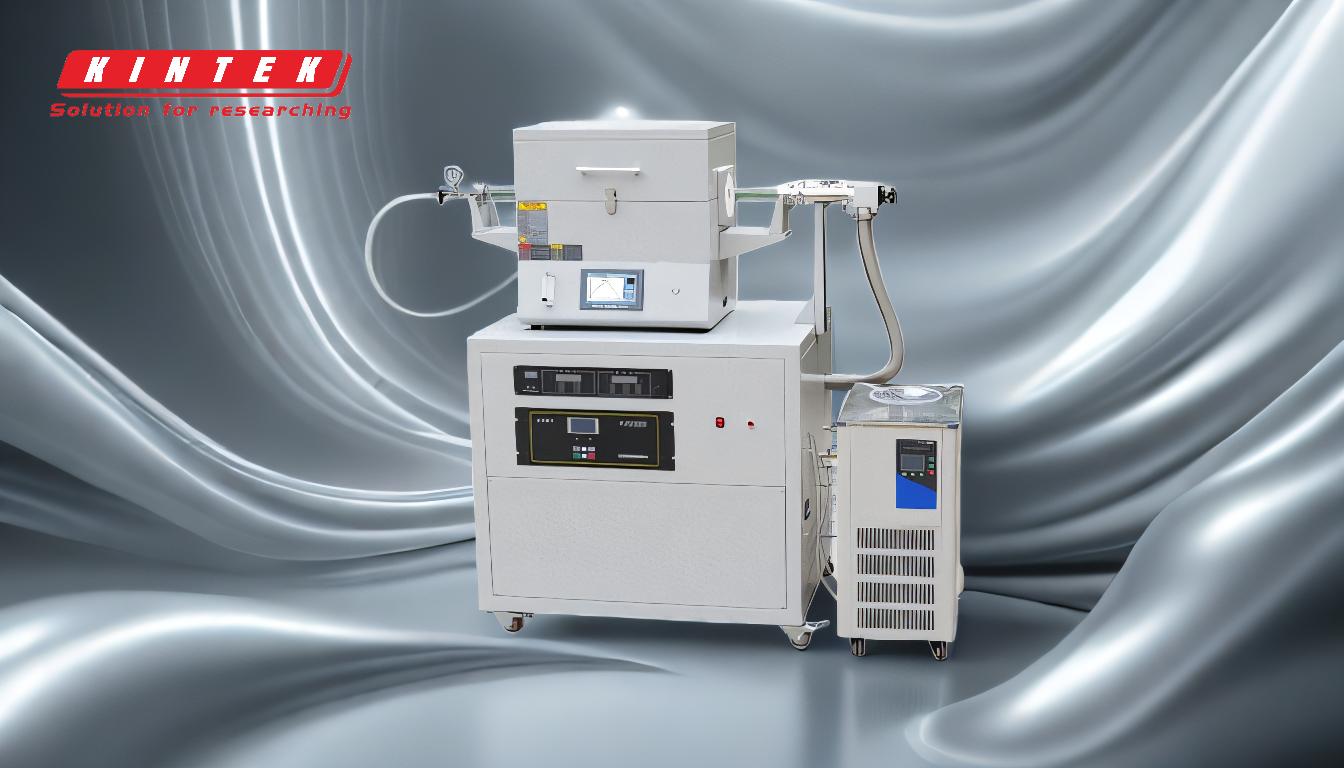
-
Nature of PVD Coatings:
- PVD coatings are extremely thin, ranging from 0.5 to 5 microns, and are highly adherent to the substrate.
- They are known for their hardness, wear resistance, corrosion resistance, and ability to withstand high temperatures.
- The coatings replicate the substrate's surface finish, making them aesthetically appealing and functional.
-
Challenges in Repairing PVD Coatings:
- Due to their thinness and strong adhesion, repairing PVD coatings is difficult.
- Minor surface imperfections, such as scratches, can sometimes be polished out, but this is limited to superficial damage.
- Significant damage, such as deep scratches, peeling, or corrosion, cannot be effectively repaired and typically requires recoating or replacement.
-
Recoating as an Alternative to Repair:
- Recoating involves stripping the damaged PVD layer and reapplying a new coating.
- This process requires specialized equipment, such as vacuum chambers, and expertise in PVD technology.
- Recoating is often more practical than attempting to repair the existing coating, especially for critical applications where performance and durability are essential.
-
Factors Influencing Repair Feasibility:
- Extent of Damage: Minor wear or scratches may be addressable, but extensive damage usually necessitates recoating.
- Substrate Material: The underlying material's properties can affect the feasibility of repair or recoating.
- Application Requirements: For high-performance applications (e.g., aerospace or medical), recoating is often the only viable option to ensure the coating's integrity.
-
Practical Considerations for Equipment and Consumable Purchasers:
- Cost: Recoating can be expensive due to the specialized equipment and expertise required.
- Downtime: The recoating process may require significant downtime, impacting productivity.
- Quality Assurance: Ensure that the recoating service provider adheres to industry standards to maintain the coating's performance and durability.
- Preventive Maintenance: Regular maintenance and proper handling can extend the life of PVD coatings, reducing the need for repairs or recoating.
-
When to Consider Repair or Recoating:
- Repair: Only for minor surface imperfections that do not compromise the coating's functionality.
- Recoating: For significant damage, when the coating's performance is compromised, or when the substrate requires protection in demanding environments.
In conclusion, while PVD coatings are highly durable and resistant to wear and corrosion, repairing them is often impractical due to their thinness and strong adhesion. Recoating is the preferred solution for significant damage, ensuring the coating's performance and longevity. Purchasers should weigh the costs, downtime, and quality assurance factors when considering recoating options.
Summary Table:
Aspect | Details |
---|---|
PVD Coating Thickness | 0.5–5 microns |
Key Properties | Hardness, wear resistance, corrosion resistance, high-temperature tolerance |
Repair Feasibility | Minor scratches can be polished; significant damage requires recoating |
Recoating Process | Stripping damaged layer and reapplying PVD coating using specialized equipment |
Factors to Consider | Extent of damage, substrate material, application requirements |
Practical Considerations | Cost, downtime, quality assurance, preventive maintenance |
Need expert advice on PVD coating repair or recoating? Contact us today for tailored solutions!