PVD (Physical Vapor Deposition) coatings are renowned for their exceptional durability, hardness, and resistance to scratching, corrosion, and oxidation. These coatings are applied in a vacuum environment, which ensures a strong bond with the substrate and eliminates contamination, further enhancing their durability. While PVD coatings are extremely hard and resistant to scratches, they are not entirely scratch-proof. Their resistance to scratching depends on factors such as the hardness of the coating material, the substrate, and the force applied. However, compared to traditional finishes, PVD coatings are far more durable and less prone to scratching.
Key Points Explained:
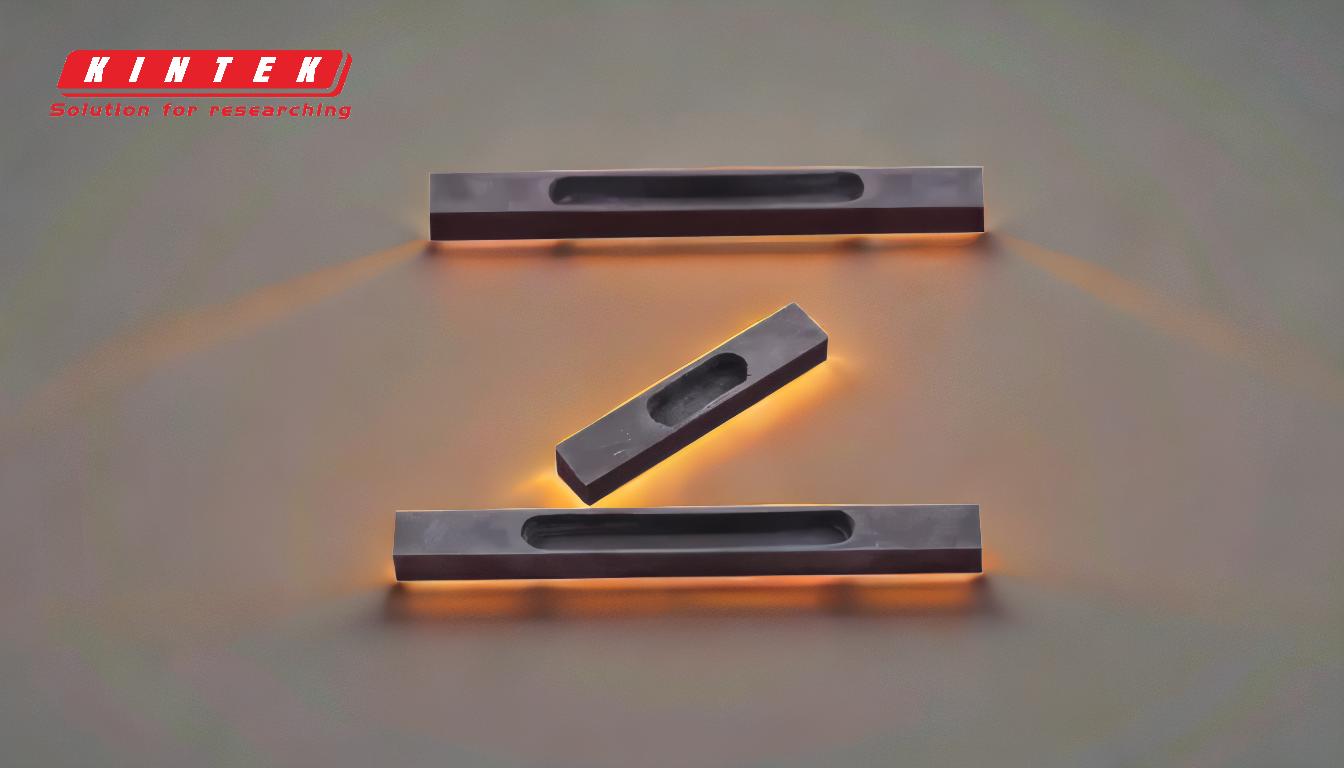
-
What is PVD Coating?
- PVD coating is a thin film deposition process where materials are vaporized in a vacuum and then deposited onto a substrate. The resulting coating is extremely hard, durable, and resistant to wear, corrosion, and scratching.
- The thickness of PVD coatings typically ranges from 0.5 microns to 5 microns, making them very thin yet highly effective.
-
Hardness and Durability of PVD Coatings
- PVD coatings are considered super-hard, often surpassing the hardness of traditional finishes. This hardness contributes significantly to their scratch resistance.
- The durability of PVD coatings is further enhanced by their strong bond with the substrate, which is achieved through the vacuum application process. This bond prevents delamination and ensures long-lasting performance.
-
Scratch Resistance of PVD Coatings
- While PVD coatings are highly resistant to scratches, they are not completely scratch-proof. Their scratch resistance depends on the hardness of the coating material (e.g., TiN, TiCN, CrN) and the force applied.
- For example, a TiN (Titanium Nitride) coating can significantly improve the wear resistance and hardness of the substrate, but it can still be scratched by materials or forces that exceed its hardness.
-
Factors Influencing Scratch Resistance
- Coating Material: Different PVD coatings (e.g., TiN, TiCN, CrN) have varying levels of hardness and scratch resistance.
- Substrate Material: The underlying material plays a role in determining the overall durability and scratch resistance of the coated product.
- Application Environment: PVD coatings are highly resistant to corrosion and oxidation, which can indirectly affect their scratch resistance over time.
-
Comparison with Traditional Finishes
- PVD coatings outperform traditional finishes in terms of scratch resistance, durability, and longevity. Traditional finishes are more prone to wear and scratching, especially in demanding environments.
- The vacuum application process of PVD coatings ensures a cleaner, more uniform finish with fewer defects, further enhancing their resistance to scratches.
-
Practical Considerations for Scratch Resistance
- While PVD coatings are highly durable, they are not indestructible. In applications where extreme wear or scratching is expected, additional protective measures may be necessary.
- For most everyday applications, PVD coatings provide sufficient scratch resistance to maintain the appearance and functionality of the coated product.
-
Applications of PVD Coatings
- PVD coatings are widely used in industries where durability and scratch resistance are critical, such as automotive, aerospace, medical devices, and consumer electronics.
- Their ability to replicate the original finish of materials with minimal effort makes them ideal for decorative applications as well.
In summary, PVD coatings are highly resistant to scratching due to their super-hard nature and strong bond with the substrate. However, they are not entirely scratch-proof and can be damaged under extreme conditions. Their superior durability and resistance to wear make them a preferred choice over traditional finishes in many demanding applications.
Summary Table:
Aspect | Details |
---|---|
Coating Process | Thin film deposition in a vacuum environment |
Thickness | 0.5 to 5 microns |
Hardness | Super-hard, surpassing traditional finishes |
Scratch Resistance | High resistance but not entirely scratch-proof |
Key Factors | Coating material, substrate, and application environment |
Applications | Automotive, aerospace, medical devices, consumer electronics, decorative |
Comparison | Outperforms traditional finishes in durability and scratch resistance |
Want to enhance your product's durability with PVD coatings? Contact our experts today to learn more!