Hydraulic systems are complex and rely on the smooth operation of various components to function efficiently. Lubrication plays a critical role in ensuring the longevity and performance of these systems. While hydraulic fluid itself acts as a lubricant, additional lubrication may be required for specific components like seals, cylinders, and pumps to prevent wear, reduce friction, and maintain optimal performance. Understanding the lubrication needs of hydraulics is essential for proper maintenance and avoiding costly repairs.
Key Points Explained:
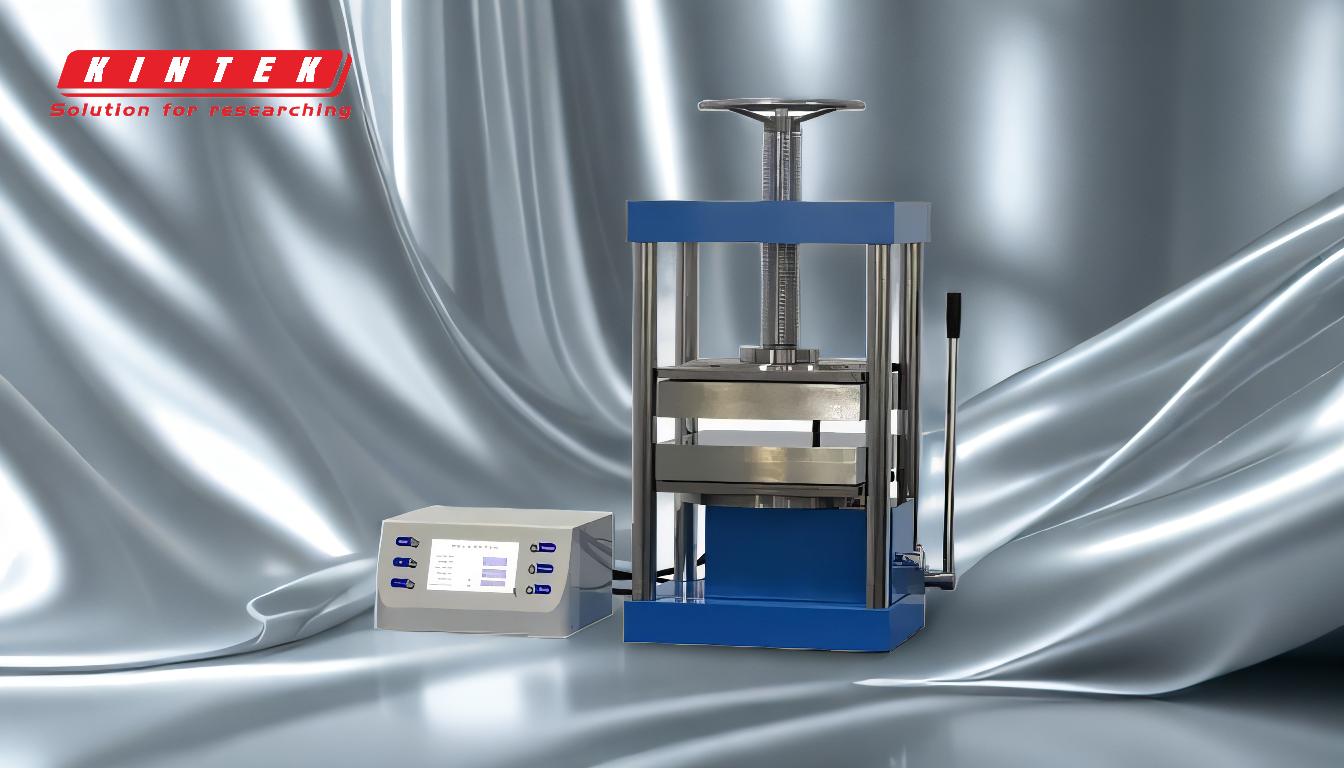
-
Hydraulic Fluid as a Lubricant
- Hydraulic fluid is the primary lubricant in hydraulic systems. It reduces friction between moving parts, prevents wear, and dissipates heat.
- The fluid must have the right viscosity and additives to ensure effective lubrication under varying operating conditions.
- Regular fluid checks and replacements are necessary to maintain lubrication efficiency.
-
Components Requiring Additional Lubrication
- While hydraulic fluid lubricates most internal components, certain parts may need additional lubrication:
- Seals and O-rings: These components can degrade over time due to friction and heat. Applying compatible grease or lubricants can extend their lifespan.
- Cylinders and Pistons: External lubrication may be needed for exposed rods to prevent corrosion and ensure smooth movement.
- Pumps and Motors: Some pumps and motors have external bearings or gears that require periodic lubrication.
- While hydraulic fluid lubricates most internal components, certain parts may need additional lubrication:
-
Importance of Proper Lubrication
- Reduces friction and wear, extending the lifespan of hydraulic components.
- Prevents overheating, which can lead to system failures.
- Ensures smooth operation, reducing energy consumption and improving efficiency.
-
Lubrication Maintenance Practices
- Regularly inspect hydraulic fluid levels and quality. Contaminated or degraded fluid can compromise lubrication.
- Use manufacturer-recommended lubricants and hydraulic fluids to avoid compatibility issues.
- Follow a maintenance schedule to lubricate external components and replace worn-out parts.
-
Consequences of Poor Lubrication
- Increased friction can lead to component wear, system inefficiency, and eventual failure.
- Overheating due to inadequate lubrication can cause hydraulic fluid breakdown and seal damage.
- Corrosion and contamination may occur, leading to costly repairs or replacements.
-
Choosing the Right Lubricant
- Select lubricants based on the operating environment, temperature, and load conditions.
- Ensure compatibility with hydraulic fluid and system materials to prevent chemical reactions or degradation.
- Consult the equipment manual or manufacturer guidelines for specific lubrication requirements.
By understanding the lubrication needs of hydraulic systems and implementing proper maintenance practices, you can ensure the longevity and reliability of your equipment. Regular checks and the use of appropriate lubricants are key to preventing downtime and costly repairs.
Summary Table:
Aspect | Details |
---|---|
Hydraulic Fluid as Lubricant | Primary lubricant; reduces friction, prevents wear, and dissipates heat. |
Components Needing Lubrication | Seals, O-rings, cylinders, pistons, pumps, and motors may require additional lubrication. |
Importance of Lubrication | Extends lifespan, prevents overheating, and ensures smooth operation. |
Maintenance Practices | Regular fluid checks, use recommended lubricants, and follow a maintenance schedule. |
Consequences of Poor Lubrication | Increased wear, overheating, corrosion, and costly repairs. |
Choosing the Right Lubricant | Consider operating environment, temperature, and compatibility with system materials. |
Ensure your hydraulic systems run smoothly—contact our experts today for tailored lubrication solutions!