Induction furnaces are highly effective for melting aluminum, offering significant advantages such as high efficiency (60-75%), reduced oxidation losses, and improved purity and uniformity of the final product. The heat source does not directly contact the aluminum, and the electrical field stirs the molten metal, making it ideal for producing aluminum alloys. However, induction furnaces lack refining capacity, meaning charge materials must be free of oxides and of known composition. Some alloying elements may be lost due to oxidation, requiring re-addition to the melt. Despite this, induction furnaces are more efficient and environmentally friendly compared to other melting methods like resistance or industrial frequency furnaces.
Key Points Explained:
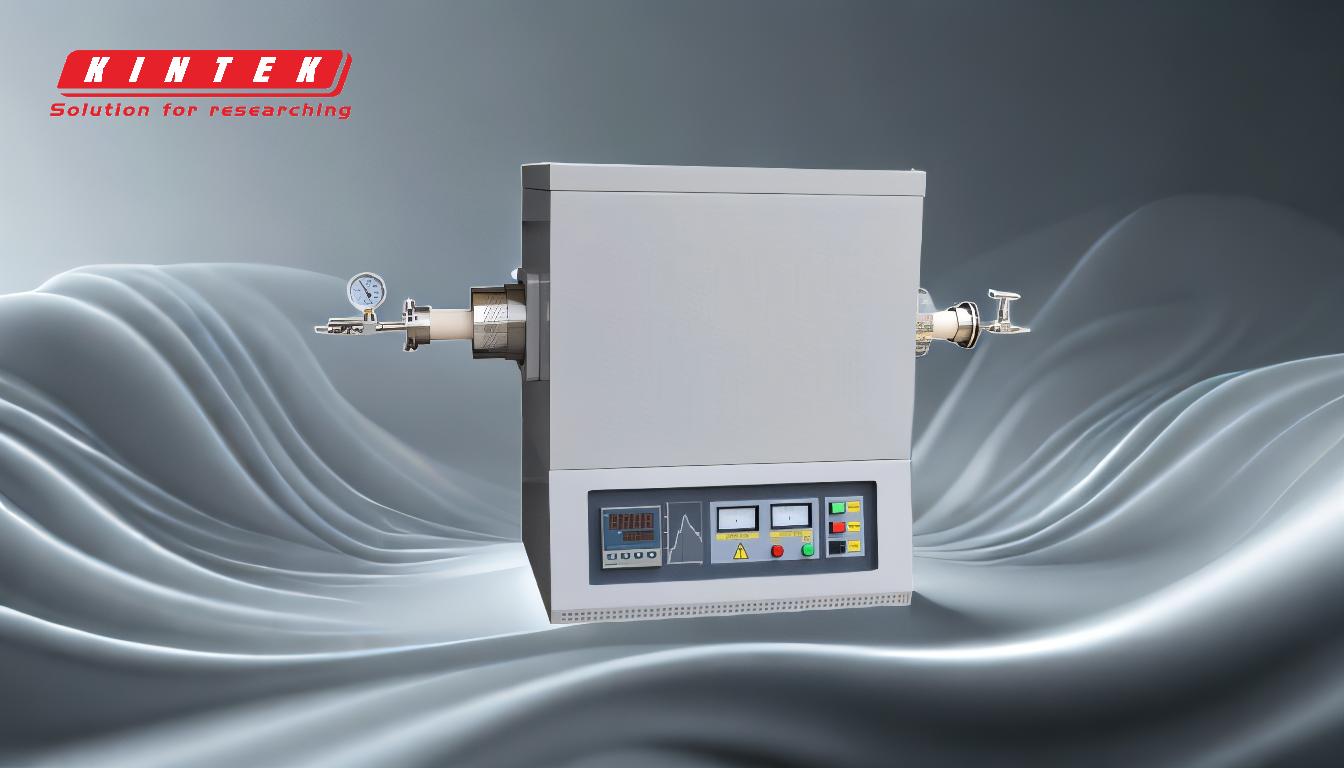
-
Efficiency and Performance:
- Induction furnaces for aluminum melting achieve an efficiency rate of 60-75%, making them highly energy-efficient.
- They reduce oxidation losses, ensuring a higher purity and uniformity in the final aluminum product.
- The heat source does not directly contact the aluminum, which minimizes contamination and allows for precise temperature control.
-
Advantages Over Other Furnace Types:
- Induction furnaces are more efficient than resistance furnaces and industrial frequency furnaces.
- They produce less noise, smoke, and dust pollution compared to power frequency furnaces, making them more environmentally friendly.
- The melting rate can be increased by simply increasing the power, providing flexibility in production.
-
Stirring Effect and Alloy Production:
- The electrical field in an igbt induction furnace stirs the molten metal, ensuring a homogeneous mix and making it ideal for producing aluminum alloys.
- This stirring effect also helps in achieving a uniform temperature distribution, which is crucial for high-quality aluminum production.
-
Limitations:
- Induction furnaces lack refining capacity, meaning the charge materials must be free of oxides and of a known composition.
- Some alloying elements may be lost due to oxidation, necessitating their re-addition to the melt, which can increase operational complexity and cost.
-
Environmental and Operational Benefits:
- Induction furnaces produce low emissions and reduce losses due to oxidation, contributing to a cleaner and more sustainable melting process.
- The absence of direct contact between the heat source and aluminum minimizes contamination, ensuring a higher quality end product.
In summary, induction furnaces, particularly those utilizing IGBT technology, are highly effective for melting aluminum, offering numerous advantages in terms of efficiency, environmental impact, and product quality. While they do have some limitations, such as the need for pre-refined materials and potential loss of alloying elements, their benefits make them a preferred choice for aluminum melting in various industrial applications.
Summary Table:
Aspect | Details |
---|---|
Efficiency | 60-75% energy efficiency, precise temperature control |
Advantages | Reduced oxidation, uniform heating, environmentally friendly |
Stirring Effect | Ensures homogeneous mixing, ideal for aluminum alloys |
Limitations | Requires pre-refined materials, potential loss of alloying elements |
Environmental Impact | Low emissions, minimal contamination, sustainable melting process |
Ready to optimize your aluminum melting process? Contact us today to learn more about induction furnaces!