Chemical Vapor Deposition (CVD) is a widely used technique for depositing thin films of materials, such as graphene, onto a substrate. The process involves the chemical reaction of gaseous precursors on the surface of a substrate, which acts as a foundation for the deposited material. Short path vacuum distillation, on the other hand, is a technique used to purify or separate compounds by distillation under reduced pressure, which lowers the boiling points of the substances involved. While these two processes are distinct, they both involve the use of substrates or surfaces for their respective operations. Below, we explore the role of substrates in CVD and how it compares to the principles of short path vacuum distillation.
Key Points Explained:
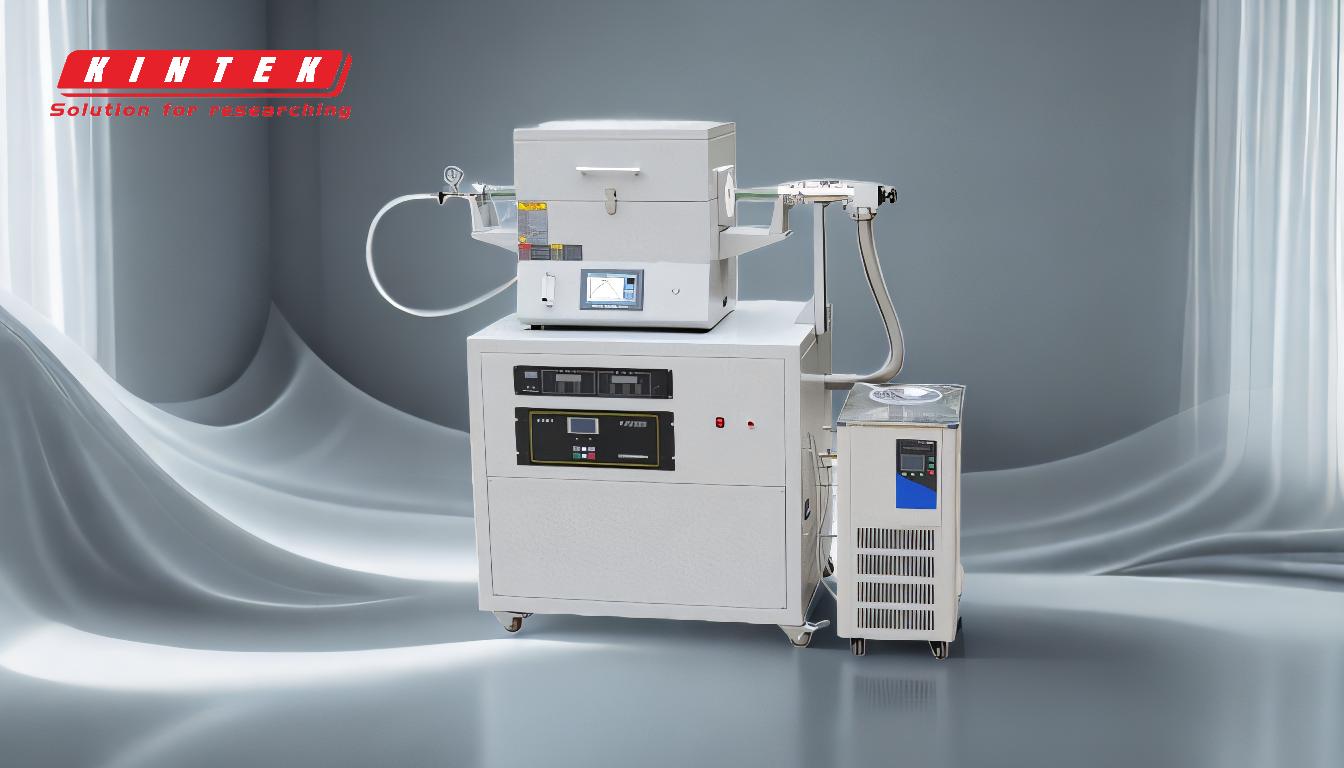
-
CVD Requires a Substrate for Deposition
- In the CVD process, a substrate is essential as it provides a surface for the chemical reaction and deposition of the material. For example, graphene is typically deposited onto a transition metal substrate, such as copper or nickel.
- The substrate not only supports the material but also influences the quality and properties of the deposited film. For instance, the crystal structure and thermal conductivity of the substrate can affect the growth of graphene.
- After deposition, the substrate can be etched or removed to transfer the deposited material (e.g., graphene) onto another surface, such as silicon dioxide, for specific applications.
-
Substrate Selection in CVD
- The choice of substrate depends on the material being deposited and the desired application. Transition metals like copper and nickel are commonly used for graphene growth due to their catalytic properties and ability to support uniform film formation.
- The substrate must be chemically compatible with the precursors and the deposition conditions, such as temperature and pressure.
- In some cases, the substrate is sacrificial, meaning it is removed after deposition to isolate the deposited material.
-
Comparison to Short Path Vacuum Distillation
- While CVD relies on a substrate for material deposition, short path vacuum distillation operates on a different principle. In this process, a vacuum is used to lower the boiling points of compounds, enabling the separation of heat-sensitive materials without degradation.
- The process does not require a substrate in the same way as CVD. Instead, it uses a distillation apparatus with a short path between the evaporator and condenser to minimize the distance vapor must travel, reducing the risk of contamination and improving efficiency.
- Short path vacuum distillation is particularly advantageous for distilling heavier molecules or heat-sensitive compounds, as it operates at lower temperatures and pressures.
-
Practical Considerations for Both Processes
- CVD: The substrate must be carefully selected and prepared to ensure high-quality deposition. Factors such as surface roughness, thermal expansion, and chemical reactivity must be considered.
- Short Path Vacuum Distillation: The focus is on optimizing the vacuum system and the distillation path to achieve efficient separation. The process is cost-effective and space-efficient, making it suitable for small-scale operations or budget-conscious setups.
-
Applications and Implications
- CVD: Used in the production of advanced materials like graphene, semiconductors, and thin-film coatings. The ability to transfer deposited materials to other substrates expands its utility in electronics, optics, and energy storage.
- Short Path Vacuum Distillation: Commonly used in the pharmaceutical, chemical, and essential oil industries for purifying compounds. Its ability to handle heat-sensitive materials makes it indispensable for high-purity applications.
-
Interplay Between Substrate and Process Efficiency
- In CVD, the substrate plays a direct role in the efficiency and quality of the deposition process. A well-chosen substrate can enhance film uniformity, adhesion, and performance.
- In short path vacuum distillation, the efficiency is determined by the vacuum system and the design of the distillation apparatus. The absence of a substrate simplifies the process but requires precise control of operating conditions.
In summary, CVD fundamentally requires a substrate to facilitate the deposition of materials, while short path vacuum distillation operates without a substrate, relying instead on vacuum conditions and optimized equipment design. Both processes are critical in their respective fields, with CVD enabling advanced material synthesis and short path vacuum distillation providing efficient purification solutions. For those interested in the technical details of short path vacuum distillation, you can explore more here.
Summary Table:
Aspect | CVD | Short Path Vacuum Distillation |
---|---|---|
Requires Substrate? | Yes, a substrate is essential for deposition and influences film quality. | No, relies on vacuum conditions and optimized equipment design. |
Key Role of Substrate | Provides a surface for chemical reactions and supports material growth. | Not applicable; focuses on vacuum and distillation path optimization. |
Applications | Graphene, semiconductors, thin-film coatings. | Purification in pharmaceuticals, chemicals, and essential oils. |
Efficiency Factors | Substrate choice, surface preparation, and chemical compatibility. | Vacuum system design and distillation path optimization. |
Discover how substrates enhance CVD processes or explore purification techniques—contact our experts today!