Induction heating does work on aluminum, and it is particularly effective for melting purposes. An induction melting furnace uses alternating current to generate heat within the aluminum, causing it to melt. The process leverages the properties of aluminum, such as its conductivity and density, to separate impurities from the pure metal. Water cooling systems are employed to manage the heat generated in the coils, ensuring precise temperature control and efficient melting. This method is widely used in industries requiring high-purity aluminum.
Key Points Explained:
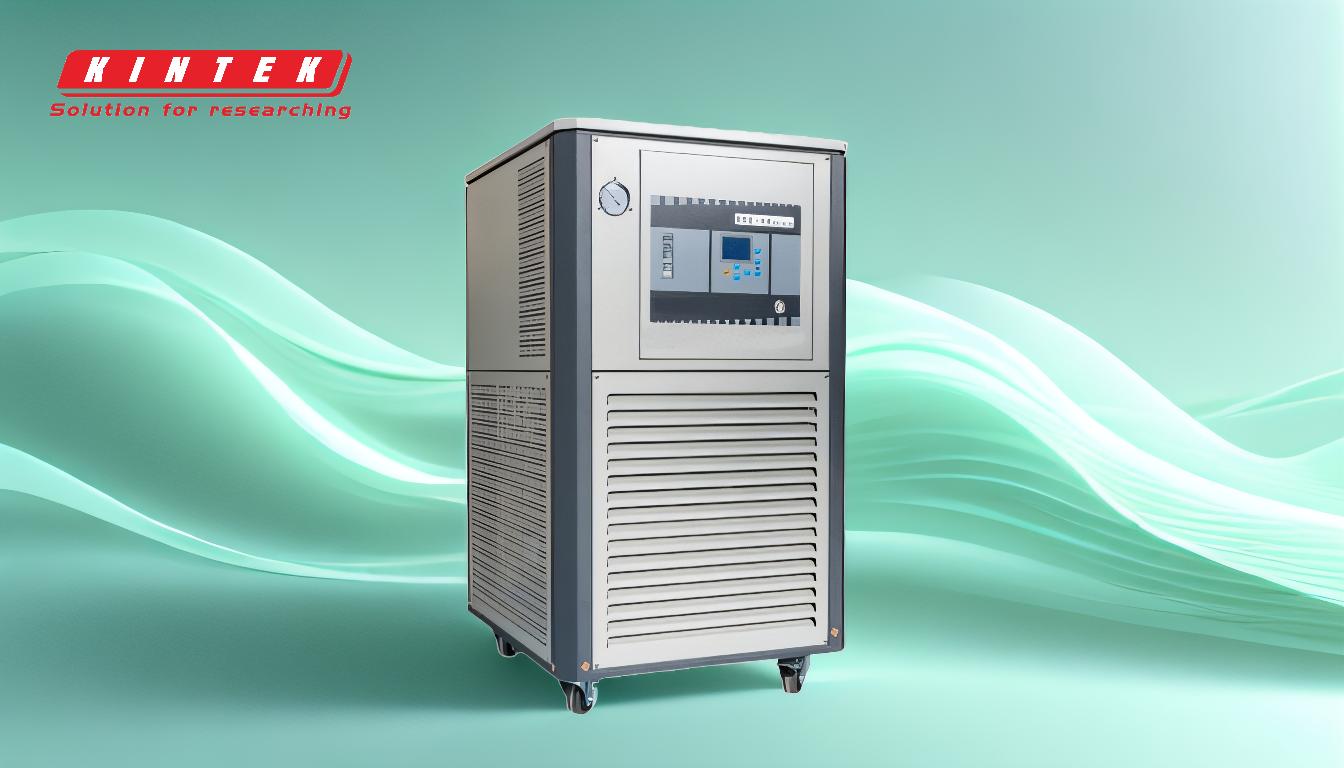
-
Principle of Induction Heating on Aluminum:
- Induction heating works by generating an alternating magnetic field, which induces eddy currents within the aluminum. These currents produce heat due to the electrical resistance of the metal.
- Aluminum, being a good conductor of electricity, heats up efficiently under induction, making it suitable for melting and other thermal processes.
-
Separation of Impurities:
- During the melting process, pure aluminum, being denser, sinks to the bottom of the furnace.
- Impurities, which are less dense, rise to the top and can be easily removed using a tilting mechanism or skimming tools. This ensures the production of high-purity aluminum.
-
Role of Water Cooling Systems:
- The coils in an induction furnace generate significant heat, which must be managed to prevent damage and maintain efficiency.
- Water cooling systems are integrated to keep the coils at an optimal temperature, enabling precise control over the melting process and faster heating rates.
-
Advantages of Induction Heating for Aluminum:
- Precision: Induction heating allows for precise temperature control, which is crucial for achieving consistent results in aluminum melting.
- Speed: The process is faster compared to traditional melting methods, reducing overall production time.
- Energy Efficiency: Induction heating is more energy-efficient as it directly heats the metal, minimizing heat loss.
-
Applications of Induction Heating in Aluminum Processing:
- Induction heating is widely used in industries such as automotive, aerospace, and construction, where high-purity aluminum is required.
- It is also employed in recycling processes to melt scrap aluminum, making it a sustainable option for metal processing.
In summary, induction heating is not only effective for aluminum but also offers significant advantages in terms of precision, speed, and energy efficiency. Its ability to separate impurities and maintain high purity levels makes it a preferred method in various industrial applications.
Summary Table:
Key Aspect | Details |
---|---|
Principle | Alternating magnetic field induces eddy currents, heating aluminum efficiently. |
Impurity Separation | Pure aluminum sinks; impurities rise and are removed for high-purity results. |
Water Cooling Systems | Maintain coil temperature, ensuring precise control and faster heating rates. |
Advantages | Precision, speed, and energy efficiency make it ideal for aluminum melting. |
Applications | Used in automotive, aerospace, construction, and aluminum recycling. |
Unlock the potential of induction heating for your aluminum processing needs—contact us today!