PVD (Physical Vapor Deposition) coatings are renowned for their exceptional durability and resistance to wear, corrosion, and chipping. These coatings bond at the molecular level with the substrate, creating a strong, thin layer that is highly resistant to external forces. Due to their hardness, wear resistance, and low friction properties, PVD coatings are less likely to chip compared to traditional coatings. Their ability to withstand harsh environments, including high temperatures and corrosive conditions, further enhances their durability. While no coating is entirely immune to damage, PVD coatings are among the most durable options available, making them ideal for demanding applications in industries such as automotive, aerospace, and medical.
Key Points Explained:
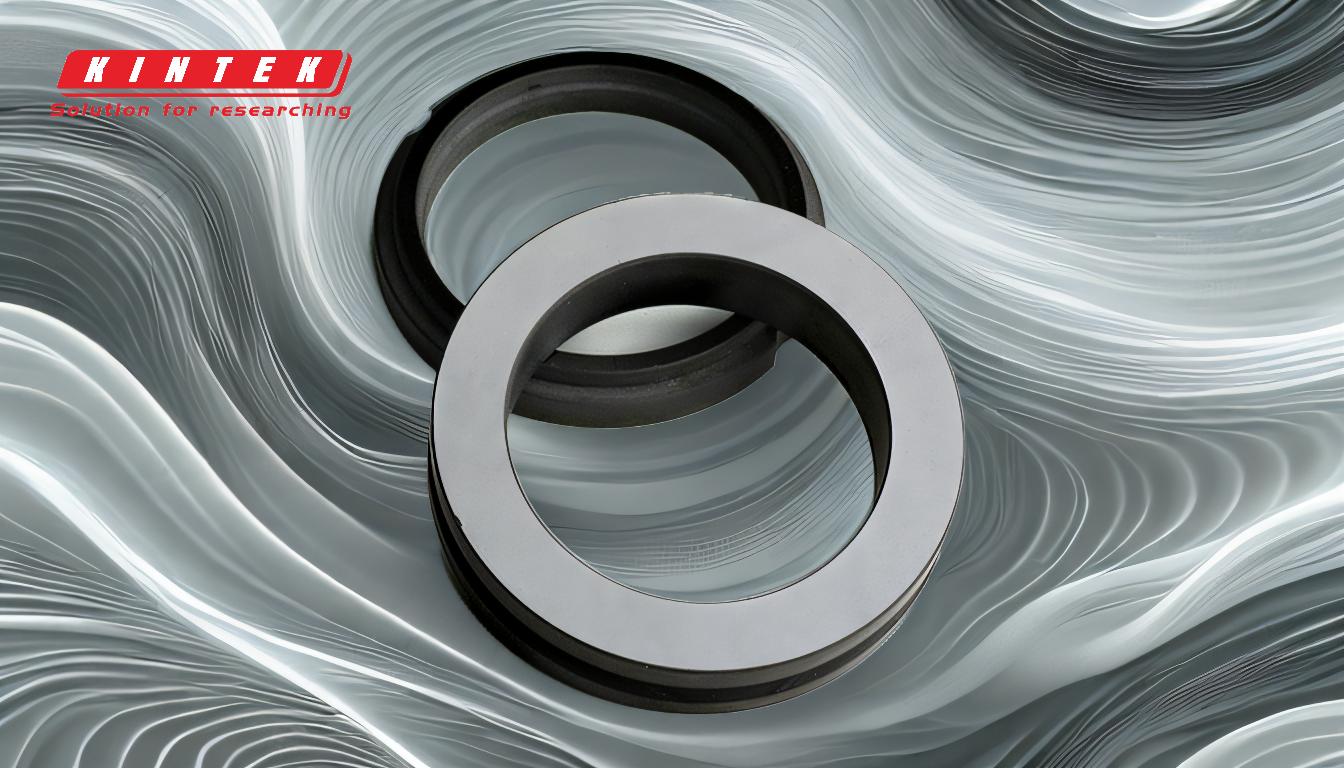
-
Molecular Bonding and Adhesion
- PVD coatings form a molecular-level bond with the substrate, creating a strong and durable connection.
- This bonding mechanism ensures that the coating adheres tightly to the surface, making it resistant to chipping even under mechanical stress or impact.
-
Hardness and Wear Resistance
- PVD coatings are known for their high hardness, often exceeding that of traditional coatings.
- The hardness of the coating contributes to its ability to resist wear, abrasion, and chipping, even in high-stress environments.
-
Thin and Durable Layer
- PVD coatings are extremely thin, typically ranging from 0.5 to 5 microns.
- Despite their thinness, these coatings are highly durable and difficult to remove, further reducing the likelihood of chipping.
-
Resistance to Corrosion and Oxidation
- The vacuum environment during the PVD process eliminates contamination and prevents oxidation, resulting in a coating that is highly resistant to corrosion and environmental degradation.
- This resistance enhances the coating's overall durability and longevity, reducing the risk of chipping over time.
-
Applications in Demanding Industries
- PVD coatings are widely used in industries such as automotive, aerospace, and medical, where durability and resistance to wear are critical.
- Their ability to withstand harsh conditions and mechanical stress makes them less prone to chipping compared to other coatings.
-
Comparison to Traditional Coatings
- Unlike traditional finishes, PVD coatings are significantly harder and more resistant to wear and corrosion.
- This superior durability makes them less likely to chip, even when subjected to rough handling or extreme conditions.
-
Real-World Performance
- PVD coatings have been shown to improve the fatigue limit and endurance of materials, such as Ti-6Al-4V alloy, by significant percentages.
- These performance enhancements further demonstrate the coating's ability to resist damage, including chipping, under real-world conditions.
In summary, while no coating is entirely immune to damage, PVD coatings are among the most durable and chip-resistant options available. Their molecular bonding, hardness, thinness, and resistance to corrosion and wear make them an excellent choice for applications where durability and longevity are paramount.
Summary Table:
Key Feature | Description |
---|---|
Molecular Bonding | Forms a strong, molecular-level bond with the substrate, reducing chipping risks. |
Hardness & Wear Resistance | Exceeds traditional coatings, offering superior resistance to wear and abrasion. |
Thin & Durable Layer | Extremely thin (0.5–5 microns) yet highly durable, minimizing chipping. |
Corrosion Resistance | Resists corrosion and oxidation, enhancing longevity in harsh environments. |
Industry Applications | Widely used in automotive, aerospace, and medical for durability and performance. |
Real-World Performance | Improves fatigue limits and endurance, reducing damage under extreme conditions. |
Want to enhance your materials' durability with PVD coatings? Contact us today to learn more!