PVD (Physical Vapor Deposition) coatings are renowned for their exceptional durability, hardness, and resistance to scratching, corrosion, and wear. These coatings are applied in a vacuum environment, which ensures a strong bond with the substrate and eliminates contamination, making them highly resistant to environmental factors like oxidation and moisture. PVD coatings are significantly harder than traditional finishes, offering superior scratch resistance and longevity. Their thinness, ranging from 0.5 to 5 microns, further enhances their durability and ability to replicate the original finish of materials. Overall, PVD coatings are among the most durable and scratch-resistant options available in the market today.
Key Points Explained:
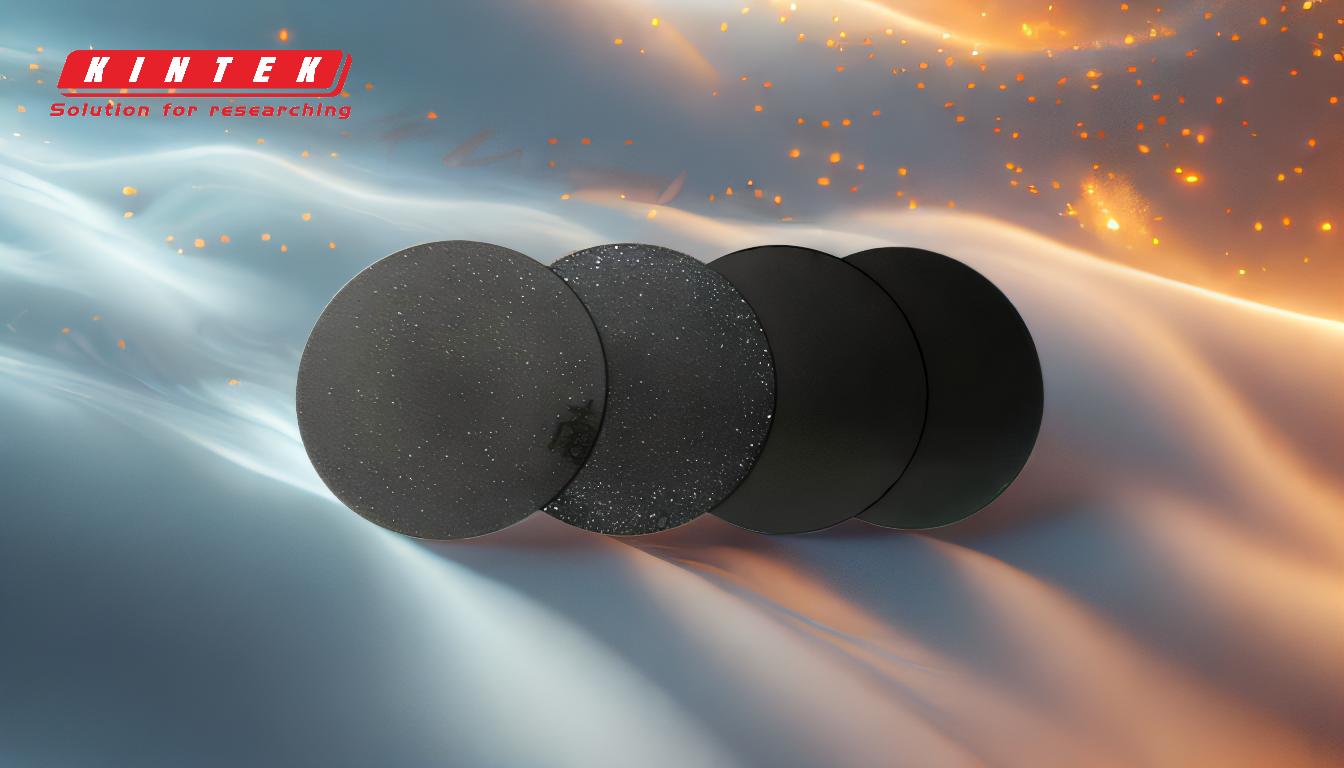
-
Superior Hardness and Durability:
- PVD coatings are considered "super-hard" and are among the most durable coatings available. Their hardness significantly reduces the likelihood of scratching, making them ideal for applications where wear resistance is critical.
- The hardness of PVD coatings is influenced by the substrate material and the specific type of coating (e.g., TiN, TiCN, etc.), which can enhance properties like fatigue limit and endurance.
-
Resistance to Scratching:
- PVD coatings are highly resistant to scratches due to their hardness and the strong bond formed with the substrate during the vacuum deposition process.
- The vacuum environment during application ensures a contamination-free coating, which further enhances scratch resistance.
-
Thin and Durable:
- PVD coatings are extremely thin, ranging from 0.5 to 5 microns. Despite their thinness, they are difficult to remove and provide excellent protection against scratches and abrasion.
- Their thinness allows them to replicate the original finish of materials with minimal effort, maintaining aesthetic appeal while providing durability.
-
Corrosion and Oxidation Resistance:
- PVD coatings offer superior resistance to corrosion and oxidation, which contributes to their overall durability and scratch resistance.
- The vacuum environment prevents oxidation and degradation caused by oxygen and moisture, ensuring long-lasting performance.
-
Applications and Suitability:
- PVD coatings are suitable for demanding applications where durability, scratch resistance, and corrosion resistance are critical. Examples include aerospace components, medical devices, and high-end consumer goods.
- Their robust temperature tolerance, impact strength, and abrasion resistance make them ideal for harsh environments.
-
Comparison to Traditional Finishes:
- PVD coatings outperform traditional finishes in terms of durability, scratch resistance, and longevity. They are designed to outlast other types of coatings, making them a cost-effective solution in the long run.
In summary, PVD coatings are highly resistant to scratching due to their superior hardness, thin yet durable nature, and strong bond with the substrate. Their resistance to corrosion, oxidation, and wear further enhances their durability, making them an excellent choice for applications requiring long-lasting protection.
Summary Table:
Key Feature | Description |
---|---|
Superior Hardness | PVD coatings are 'super-hard,' reducing scratching and enhancing wear resistance. |
Scratch Resistance | Strong bond with substrate and vacuum application ensure high scratch resistance. |
Thin and Durable | 0.5 to 5 microns thick, offering excellent protection and replicating material finish. |
Corrosion Resistance | Resists oxidation and moisture, ensuring long-lasting performance in harsh environments. |
Applications | Ideal for aerospace, medical devices, and high-end consumer goods. |
Comparison to Finishes | Outperforms traditional coatings in durability, scratch resistance, and longevity. |
Want to enhance your product's durability with PVD coatings? Contact us today to learn more!